REPOSTED: Lessons About Safety Culture from the Deepwater Horizon Accident
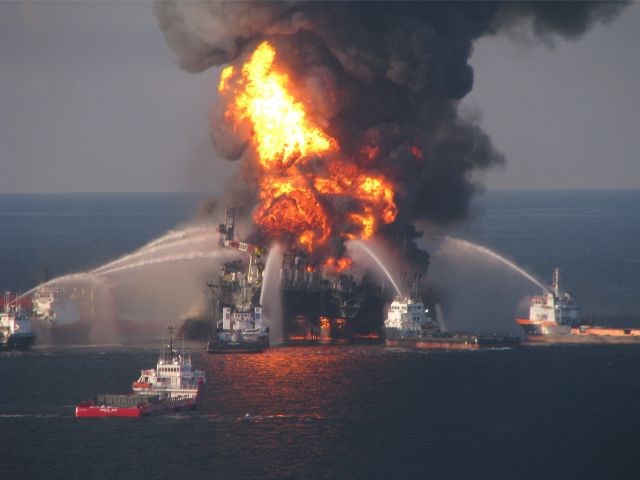
What Can We Learn NOW?
On June 14, 2010, I published this article and this question:
How Long Must We Wait To Learn?
I asked: “Do we need to wait for the completion of the Presidential Commission’s investigation to learn from the BP Deepwater Horizon Accident?”
OK … I know that asking that question before the formal investigations were complete made some people mad, but … Here’s the answer nonetheless.
NO – WE DON’T NEED TO WAIT TO LEARN.
First, let me say that as the many official investigations continue (some continued for years), we will learn more about the technical details of what happened:
- The equipment failures that cause the failure of the blowout preventer.
- The details of the reasons for replacing the mud with seawater.
- The design basis for the well design and construction decisions that turned out to be inadequate to prevent a blowout.
These are things that we should learn with time.
Thus, people aren’t entirely wrong when they say…
“Wait until the official investigations are completed.”
We don’t want to jump the gun and jump to conclusions without the facts.”
That sentiment is well and good. But they are missing my point.
We already know enough about some parts of the accident to be able to learn some important lessons. Lessons that we need to learn RIGHT NOW.
First Lesson That Should Be Learned NOW! (Safety Culture)
The first and most significant thing we can learn is that SAFETY CULTURE MAKES A DIFFERENCE.
We already knew that drilling in deepwater is dangerous before the BP Deepwater Horizon accident, and we certainly know it now.
The risk of failure in deepwater is higher than that of drilling on land or in shallow water. The deeper one goes, the more complex drilling and well design become, and the more technology is applied. These facts make it more important to understand what makes a high-reliability organization tick—what produces a good safety culture for demanding environments.
I think everyone agrees with the previous paragraph.
Yet, BP did NOT take extra precautions in designing or constructing the well being drilled by the Deepwater Horizon. In fact (and we know this to be a fact from testimony already given), they didn’t take precautions that other companies take and are “standards” for drilling in deep water.
Shortcuts

What shortcuts did they take? Here are the five that I think have already been proven:
1. BP chose the cheaper but less safe design using a single liner for well completion. BP said the design had longevity advantages but was mainly faster and cheaper. The choice was based on cost, not safety.
2. BP used too few hangers to center the casing. I’m not a drilling expert, but the expert told BP that the six hangers were WAY TOO FEW and would make it almost impossible to get a good cement job.
3. Failure to circulate the mud thoroughly before cementing. An API standard requires fully circulating the mud. Not circulating the mud fully was a safety shortcut that saved them time and money.
4. Failure to run a cement bond log. If this was a standard well and everything had gone right, you might skip this safety step. But on a deep well, with a single casing, with too few hangers, and with a bad first test, skipping this cement bond log was inexcusable. They were leaving safety to luck. And they ran out of luck that day.
These are facts.
Of course, BP argues that MMS approved these shortcuts. But MMS’s errors don’t mean that BP was right and had a safe well design. If and when they occurred, the MMS mistakes are just additional failed safeguards that allowed the accident to progress.
Plus, I’m not saying that these are all the shortcuts. There are MORE.
I’m saying that these shortcuts are sufficient to indicate that BP’s practices were NOT to make safety the highest priority, at least for this well’s safety.
What is the Safety Culture?
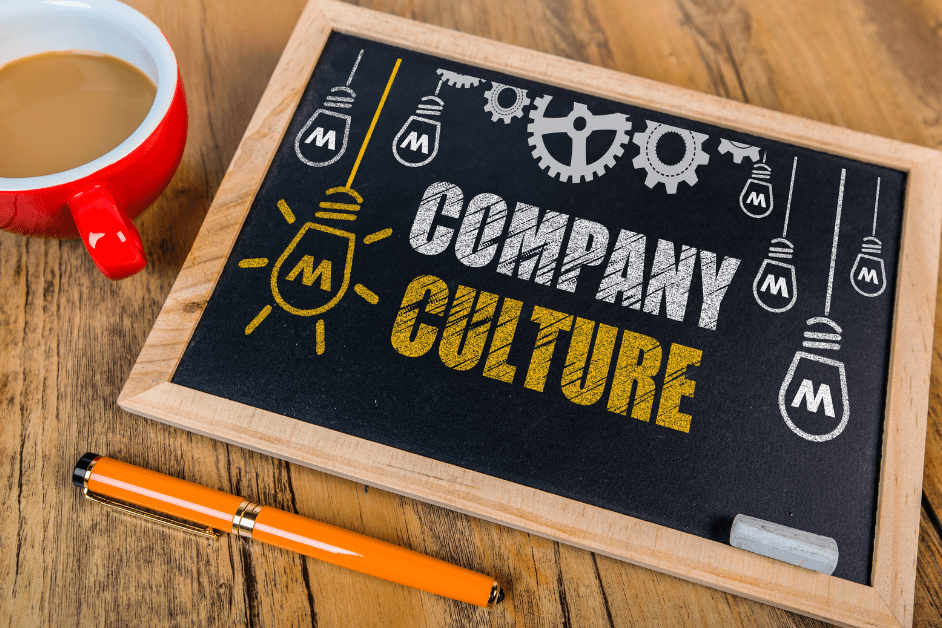
The question remaining is …
“Is this the BP culture, or were the people drilling this well ‘outliers’ –
rouge engineers and supervisors who were working outside BP’s culture.”
This is where I make a reasonably safe assumption.
This well was so deep and important that it couldn’t (and shouldn’t) slip underneath the radar of BP’s management. Fairly senior management (maybe not the CEO, but certainly some high-up folks) must have known about the design decisions. I believe investigators will be able to show significant management pressure to get the well completed and move on to the next well. This pressure – without enough consideration for safety as an overriding priority – is the safety culture at BP.
Thus, even though they talk about…
” …focusing on safety like a laser.”
and
“We don’t do anything unless it is safe.”
… the reality, which is reflected by the practices in the field, is quite different.
When I heard the BP America President say in Congressional testimony that:
“We don’t do anything unless it is safe.”
I knew that he didn’t understand safety. Why? Safety is never absolute. Everything we do involves some risk.
Therefore, we can learn NOW.
We can learn that SAFETY CULTURE IS IMPORTANT.
High-Reliability Organizations
And there are important lessons that are common practices in high-reliability organizations that all organizations facing high-risk, high-complexity operations must learn.
How do I know about these lessons?
I worked in a high-reliability organization. The Nuclear Navy. And I “got it.”

I also studied human factors and organizational design and understand why a high-reliability organization functions successfully.
But obviously, not everyone gets it.
I say obviously because repeated major accidents prove many leaders in high-risk industries don’t get it.
Does BP’s Senior Management Get It?
Therefore, from the “evidence” of their repeated severe accidents, I conclude that BP senior management doesn’t get it. They don’t understand the safety culture that they created.
Time Has Passed – What Should We Do?
Even 14 years later, there are lessons that many executives in high-risk industries need to learn. Lessons that we understand and are willing to share. So, at the 2025 Summit in Knoxville, TN, on October 1-3, We are having a whole best practice track titled:
High-Reliability Organization Best Practices
What is in the track? Here are the sessions:

CLICK HERE for more details about this track.
But There Is More!
In addition to the High-Reliability Organization Best Practices Track, we have a pre-Summit Course on September 29-30 titled:
Analyzing & Fixing Safety Culture
Find out more about this course and how you should apply it to improve safety performance HERE.
Learn NOW!
So, here is my overall advice for any major accident …
Don’t wait to learn.
Instead, attend the pre-Summit Course, Analyzing & Fixing Safety Culture, and the 2025 Global TapRooT® Summit to learn about high-reliability organizations and ways to prevent accidents, fatalities, and serious injuries by improving your safety culture.
_________________________
This article was originally published in 2010 and revised slightly to include information about the 2025 Summit. We hope that the reminder of the importance of high-reliability organizations in hazardous industries and the importance of safety culture helps prevent future process safety failures.