Precursor Incidents – Why the TapRooT® Folks Want You to Sweat the Small Stuff
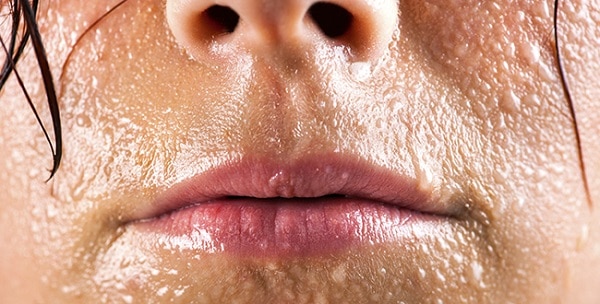
Resolve precursor incidents before they worsen.
What are precursor incidents? In a article, System Improvements CEO and TapRooT® co-creator Mark Paradies defines a precursor incident as:
PRECURSOR INCIDENTS
Minor incidents that could have been a major accident
if one or two more Safeguards would have failed.
Why are precursor incidents investigations important?
If another Safeguard fails, if the sequence is slightly different, or if your luck proves worse, the precursor incident becomes a major accident, a fatality, or a significant injury. Thus, a precursor incident’s potential consequences are high. Precursor incidents are sometimes called “HiPos” (High Potential Incidents) or “potential SIFs” (Significant Injury or Fatality).
TapRooT® co-creator Mark Paradies observes:
“I’ve never seen a major accident that wasn’t preceded by one or more precursor incidents. I’ve never talked to a senior manager that thought a major accident was acceptable. Most claim they are doing everything possible to prevent them. However, many senior managers don’t require advanced root cause analysis for precursor incidents. Thus incidents that don’t have current major consequences are classified as a low consequence event and only receive a cursory review. People ask “Why?” multiple times then implement ineffective corrective actions. Sometimes these minor actual consequence (but high potential consequence) precursor incidents aren’t even reported. Management lets these precursor incidents continue (repeat) until a major accident happens. Then it’s too late. You can’t turn back the hands of time.”
Success story: ROI on precursor incidents investigation
Small precursor investigations pay off for companies who learn to analyze and fix them by using TapRooT® Root Cause Analysis. A TapRooT® client, an underground coal mining company, was experiencing two to three fatalities a year. The company decided to change its approach to safety and apply TapRooT® to find the root causes of precursor incidents and serious accidents. They developed effective fixes and experienced major improvements – no fatalities for the next three years. See the company’s success story for a more detailed description of its results.
Watch the TapRooT® TV video: “How to Avoid Big Problems by Paying Attention to the Small Stuff”
Listen to TapRooT® professionals Mark Paradies and Benna Hughes discuss on TapRooT® TV “How to Avoid Big Problems by Paying Attention to the Small Stuff” — in other words, investigating precursor incidents with the focus on keeping major incidents from occurring.
Learn more about using TapRooT® Root Cause Analysis to investigate precursor incidents
How can you learn to apply TapRooT® to investigate precursor incidents? Read Using the Essential TapRooT® Techniques to Investigate Low-to-Medium Risk Incidents. Order the book set at the TapRooT® Store.
Better yet, get the book when you attend the 2-Day TapRooT® Root Cause Analysis Course. The course teaches the essential tools needed to quickly investigate a precursor incident, find the incident’s root causes, and develop effective corrective actions. The essential TapRooT® Techniques include:
- The SnapCharT® Diagram: a simple, visual technique for collecting and organizing information quickly and efficiently.
- The Root Cause Tree® Diagram and Dictionary: an easy-to-use resource to help investigators find root causes that they previously would have overlooked.
- The Corrective Action Helper® Guide: helps people develop corrective actions by seeing outside the box.
See the list of upcoming public 2-Day TapRooT® Courses.
Why TapRooT® RCA?
First, TapRooT® has an extensive development history and is being continuously improved. (See a brief description of the TapRooT® History.)
Next are the results that industry leaders are achieving in a wide variety of industries around the world. In a word, impressive. Go to the TapRooT® website. Next, look at the nav across the top and click on SOLUTIONS and then click on the INDUSTRY tabs. Pick an industry to learn about a company’s success story.
Then, there is the TapRooT® Software. We took a unique, scientific, successful RCA system and made it even easier to use with great software.
Finally, there is a worldwide network of TapRooT® Users. We have a LinkedIn Group and an annual Global TapRooT® Summit where TapRooT® Instructors, industry leaders, and professionals from around the world gather to network, listen to industry leaders, keynote speakers and to updates on best practices. You won’t find a better peer group interested in root cause analysis and performance improvement! The network created by attending the TapRooT® Summit will help you learn and solve problems, no matter where you are.
Don’t settle for less than the best root cause analysis
Some people settle for an easy, but ineffective RCA tool. They ask “Why?” or build a Fishbone Diagram. They do this because they don’t realize how important developing effective fixes for precursor incidents are. They doom their facility to future major accidents.
You don’t want to make this mistake. You need to be an effective problem-solver. You need TapRooT® Training.
- 2-DayTapRooT®Training;
- 5-Day TapRooT® Training;
- Or see the worldwide list of upcoming public courses.
Questions? Please call us at 865.539.2139.