How to fix human error…
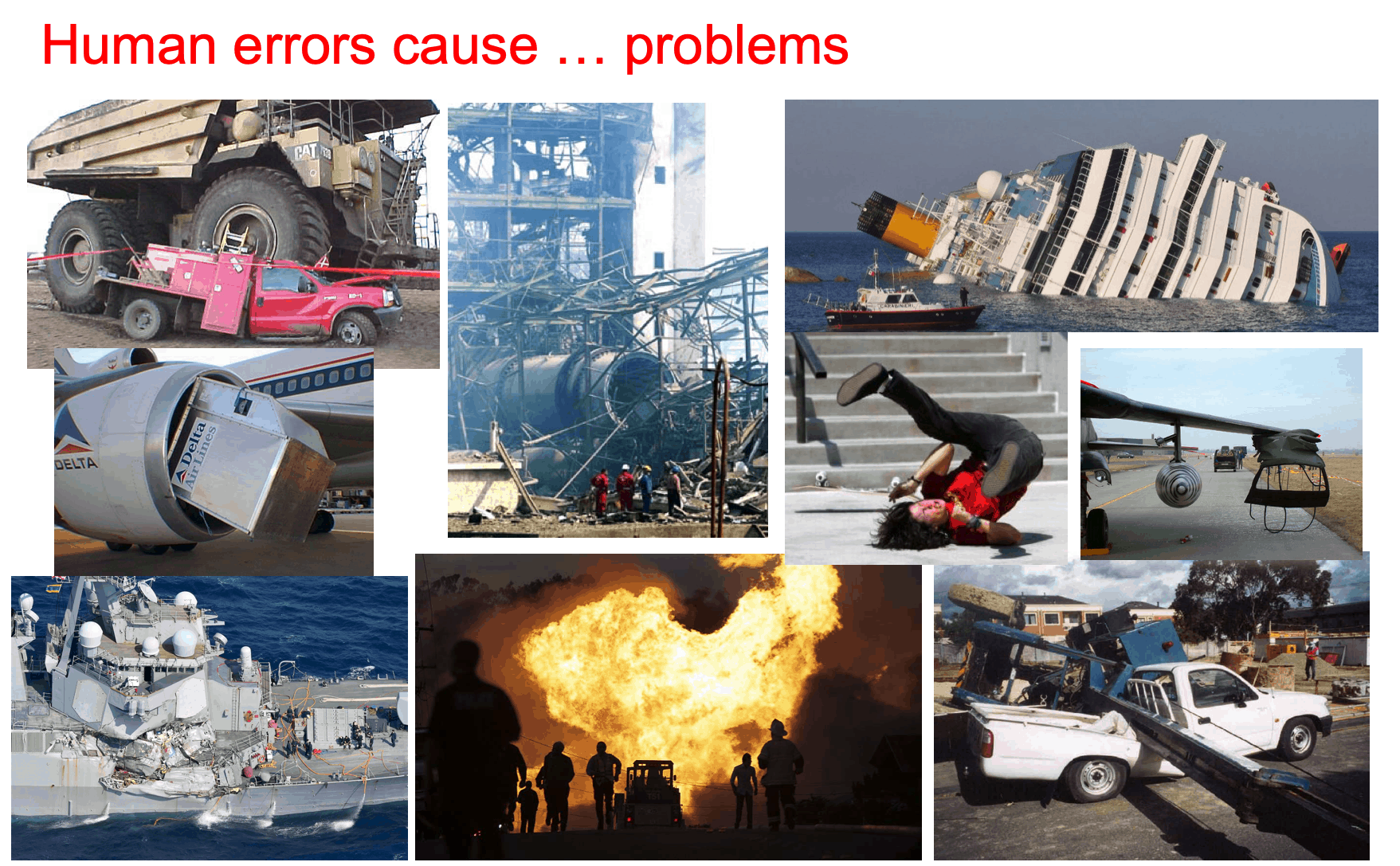
This article is derived from Mark Paradies’ talk at the 2009 Global TapRooT® Summit.
Idea #1: Automation.
Elon Musk believes that automated driving could save half a million lives each year (worldwide).
Want to get rid of human error? Automate the process!
Except that automation may cause other types of errors.
For example, the Boeing 737 Max problems.
Or the crashes involving Tesla cars.
People in charge of automated systems are often heard saying:
“What is it doing?”
and
“Why is it doing that?”
Or, the may get drowsy and fall asleep trying to monitor the automation (this has happened in the cockpit on several highly publicized occasions).
Idea # 2: Inherently Safer Systems or Remove/Reduce the Hazard
Trever Kletz popularized this idea. The US Chemical Safety Board has been promoting the idea after several recent chemical plant fires/explosions.
If you can, removing the hazard is always a good idea.
What is the problem?
If you are at a plant that is already operating, removing the hazard may be costly.
So the key to this issue is … is it worth the cost and do you have the money?
Idea #3: Mistake Proofing
This idea has been around for awhile. And when it works, it seems ingenious.
Kevin McManus gave a course teaching mistake proofing as one of the advanced courses prior to the 2019 Global TapRooT® Summit. (Get more information about having a course at your site by CONTACTING US.
What’s the problem with Mistake Proofing?
Some people just can’t be helped.
That’s why when I was in the Navy we said that nothing could be made “sailor proof.”
Idea #4: Human Reliability Best Practices
You have probably heard of at least some of these. Many are good ideas. What is the problem?
TRIGGERS
Here are some of the triggers I’ve seen taught for just one of the best practices – Questioning Attitude:
Maybe I should add one more…
When your list of triggers gets this long, it is like saying, use this practice all the time, everyday.
That starts to become the old advice, “Be careful.”
Idea #5: Safety II
Researchers claim that human error doesn’t exist in our modern world problems. Rather, they see it as human variability and we just call it error.
I don’t want to try to explain this here … instead I will provide a link to another article I wrote to help you dig into the theory:
https://www.taproot.com/keepitsimple/
Needless to say, there are both good and bad ideas in this new perspective.
Idea #6: Use TapRooT® Reactively and Proactively
TapRooT® can be used to investigate and fix incidents with simple human errors.
It can be used to investigate and fix the causes of major accidents.
And it can be used PROACTIVELY to keep major accidents from happening.
One of the parts of TapRooT® that makes it so effective in stopping human error is the guidance provided by the TapRooT® Root Cause Tree® and the tools to develop effective corrective actions.
To find out how to apply TapRooT® to solve human error issues, attend one of our 5-Day TapRooT® Advance Root Cause Analysis Team Leader Courses. See the upcoming public courses being held around the world here:
https://www.taproot.com/store/5-Day-Courses/
All six ideas above have some value. The 5-Day TapRooT® Course will help you understand how to approach investigating and solving human error related incidents and how to stop major accidents. Register for a course today!
Thank you for this good article ” How to fix human error.”
Best regards
Seidel Muriel Montoya
Cali, Colombia, South America
Just watched the video on this subject and followed the link to the article. Improving human reliability is the current emphasis of many safety oriented organizations. I believe one of the issues with addressing the issue is having the right boundaries to the problem.
I recall a cartoon in one of the Tap Root books that stated that the factory of the future would have only two employees, a man and a dog; the man was there to feed the dog and the dog was there to make sure the man didn’t touch anything. It may be funny but it does portray the way many view human performance.
If we see the problem as human error, isolated from the surroundings, we will never identify workable solutions. We have lots of accident data showing that human error led to the bad thing happening. We don’t have reliable data on how many times human intervention prevented bad things from happening.
Without looking at the pros and cons of human actions, the problem might not be evaluated accurately. Unlike performing a LOPA (Layer of Protection Analysis) on safety instrumented systems, there are no real probabilities of failure for human actions.
Looking forward to seeing future installments. The video mentioned 18 items? Five down, thirteen to go!
I wanted to purchase $114.00 worth of guidance, but not for over $300.00 shipping charges