Twelve Years Since the Deepwater Horizon Blowout, Explosion, and Fire
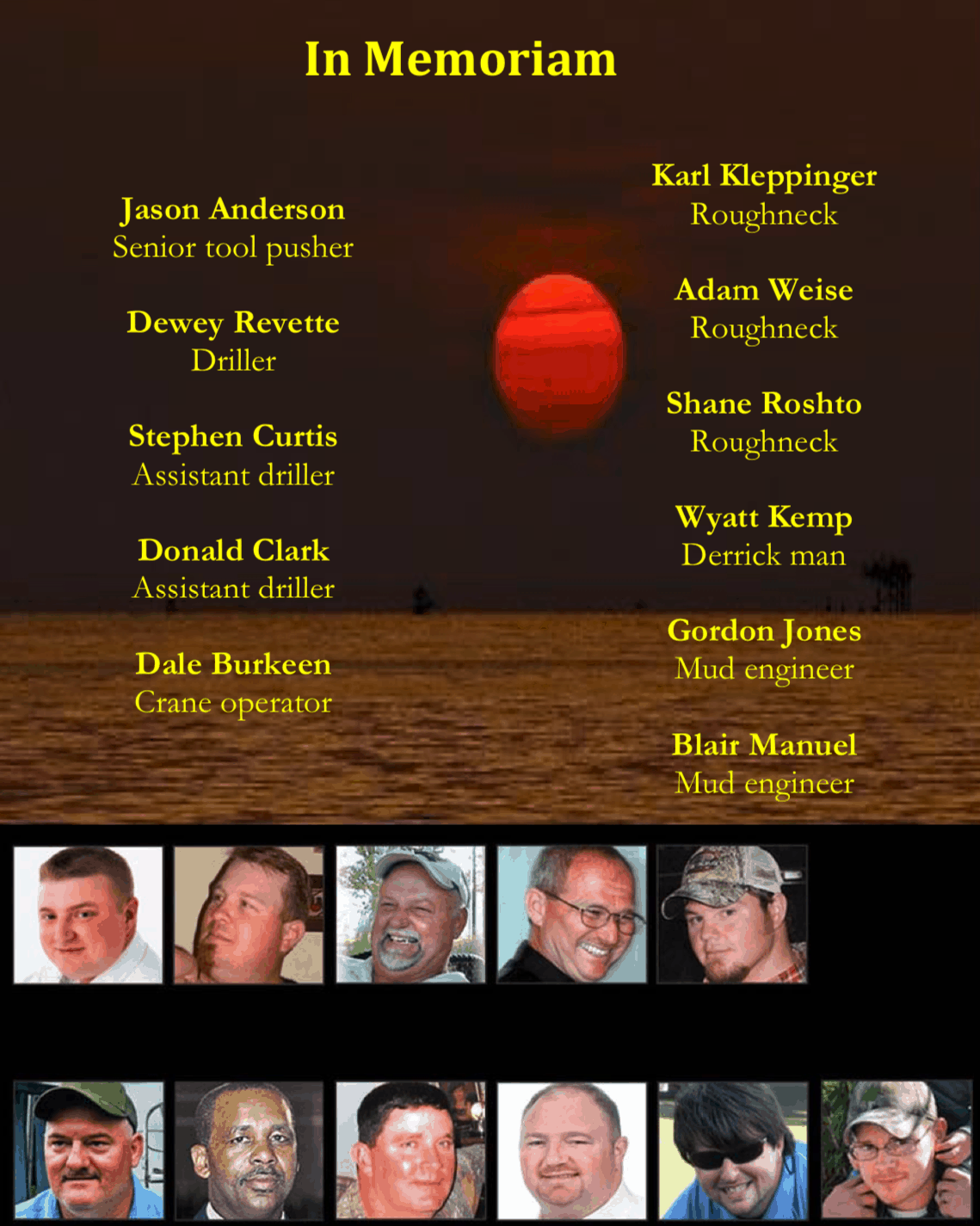
Remembering the Deepwater Horizon Accident – 12 Years After
First, let’s start by remembering those that lost their lives in this accident (shown in the picture above from the Deepwater Horizon Study Group Final Report):
- Jason Anderson
- Aaron Dale Burkeen
- Donald “Duck” Clark
- Stephen Ray Curtis
- Gordon Jones
- Roy Wyatt Kemp
- Karl Kleppinger Jr.
- Keith Blair Manuel
- Dewey Revette
- Shane Roshto
- Adam Weise
And those who loved them.
And those that were injured and seriously affected mentally by the accident.
Also, those that lost their jobs, work, or livelihood as a result of the accident.
And the environment, that suffered three months of uncontrolled flow from the well.
What Lessons Should Have Been Learned?
There were many investigations and lessons learned that were published. This includes:
- BP’s investigation
- TransOcean’s investigation
- The Presidential Commission’s investigation
- The Coast Guard/Bureau of Ocean Enery Management Regulation investigation
- The CSB investigation
- Deepwater Horizon Study Group Final Report
This accident could have been prevented. The:
- 11 deaths
- extensive environmental damage
- vessel destroyed
- impact on those that survived
didn’t need to happen.
Lessons could have been learned from previous incidents. Effective root cause analysis could have stopped this accident before it happened.
What were the most important lessons learned from this accident? That’s a tough question to answer. But here are four suggestions…
First Lesson Learned from Deepwater Horizon – Process Safety
I think the first lesson that should have been learned is that process safety needs to be applied to oil exploration and production just like it needs to be applied to the industries covered by the EPA’s Risk Management Plans and OSHA’s Process Safety Management Rule.
But there’s more…
There are missing pieces of process safety management that need to be improved. How? By following the advice of Admiral Rickover. See:
These missing parts of the current application of process safety is a major reason why we continue to have process safety accidents in the oil business.
Second Lesson Learned – Senior Management
My opinion of the second most important lesson (and maybe this should have been the first) that should have been learned is that Senior Management, starting with the CEO and Board of Directors, is responsible for safety. You can’t achieve safety excellence without their support.
I was especially convinced of this watching the deposition to Tony Hayward. He totally violated Rickover’s advice about:
I was talking to Astronaut Jim Whetherbee (speaker at the 2020 TapRooT® Summit) and we both agreed that you just can’t achieve safety excellence if the CEO is working at crossed purposes. You can try to improve safety from the bottom up but budget cuts, production pressure, and bad rewards programs will sabotage your efforts.
If you are the VP in charge of safety, you need to ensure that the COO, CEO, and Board of Directors understand their prominent role in achieving safety excellence. How what they do directly impacts the safety culture and the actions of those in the field. If you don’t do this, odds are the pressure to meet quarterly earnings goals will override their interest and support of the efforts needed to make safety a value that everyone in the corporation knows that senior management supports.
Third Lesson Learned – Human Factors
This lesson learned was almost overlooked by most of the investigations. Why did the driller and others miss the problems that were developing? Why didn’t they spot the problems BEFORE the blowout? I’m convinced it had to do with poor human factors design of the displays used for the drilling process.
Designing displays for the complex process of drilling is not easy. Certainly maintaining well control is a primary function of the displays in the drilling shack. Post-accident, engineers could easily spot the well control problems developing in the data they reviewed. But to the driller and others in the drill shack, the developing problem wasn’t noticed and diagnosed until it was too late. This indicates a human factors problem.
This should make the application of human factors to the design of displays in every drill shack something of primary importance. But unlike the accidents at Three Mile Island, this lesson wasn’t highlighted by the many investigations.
Fourth Lesson Learned – Root Cause Analysis
All the lessons above could have been learned by previous incidents at BP, the company in charge of drilling the Macondo well. BP’s failure to learn these lessons meant that they were doomed to have a major accident. This is always the case when you have poor root cause analysis.
The BP Texas City Refinery explosion and fire should have taught BP this lesson. But they didn’t learn it.
If you don’t meet the fundamental requirements of root cause analysis, you will have repeat incidents. Sooner or later the wrong set of circumstances will come together to cause a major accident. The more risk you face, the bigger the accident will be.
Don’t neglect to perform a thorough and credible root cause analysis of your precursor incidents. This investment in learning is the best way to prevent major accidents.
Achieve Excellence
It will be a true tragedy if we fail to learn from this accident.
It’s been 12 years. Were the lessons learned? Has the industry forgotten what happened? With so much turnover in the industry, will new people make the same mistakes? Have the worse performers been brought up to the highest standards?
Please review your efforts to ensure the prevention of major accidents at your company. Don’t let the failure to investigate and fix precursor incidents doom your company to suffer a major accident.
Well done!
I presented a presentation at an ASSE Conference shortly after the Deepwater Horizon Incident happened. I believe your article hit all the main factors (Human, Management, Process Safety, and failure to apply appropriate Corrective Actions to previous incidents (Proper Root Cause Analysis & Corrective Action Process.