Why Do You Need the Best Root Cause Analysis?
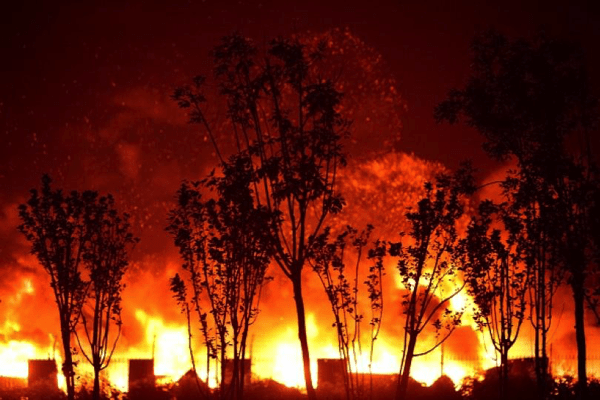
Best Root Cause Analysis: Why You Need It…
Before we discuss the best root cause analysis, you might wonder, what is root cause analysis. Read about “What is root cause analysis?” at this link:
https://www.taproot.com/what-is-root-cause-analysis-updated/
Reasons You Need the Best Root Cause Analysis
Reason #1 – Avoid Pain, Suffering, and Sorrow
Have you ever had a fatality or a serious injury at your facility? If you have, then you know about the pain, suffering, and sorrow that come with a serious injury or a fatality.
If you have never experienced a fatality, read this article:
https://www.taproot.com/content/wp-content/uploads/2015/07/StopSacrifices.pdf
The link above is to the original newsletter article published back in 2003. An updated article about a mining accident was published at this link:
https://www.taproot.com/stop-the-sacrifices-2/
If you attended the Summit in 2018, you witnessed another form of pain.
Mike Willams, a survivor of the Deepwater Horizon accident – seated at the right, told his story while being interviewed by Mark Paradies. Anyone who was there could tell you about Mike’s pain and survivor’s guilt. You never want to experience it.
Stopping fatalities and significant injuries is probably the biggest reason to use the best root cause analysis to learn from precursor incidents to stop major accidents.
Reason #2 – You Want to Save Money by Stopping Major Accidents
Here are five examples of the cost of a major accident/incident:
- The 2019 Camp Fire, caused by a failed PS&G power line, cost $16.5 billion dollars.
- The 2013 explosion at West Fertilizer Company in West, Texas, cost more than $247 million, including $16 million in federal disaster assistance and $230 million in insurance-related losses. The company was only insured for $1 million.
- The 2012 fire at the Chevron Richmond Refinery cost nearly $450 million, including $2 million in fines and restitution, and caused an increase of $447 million in gasoline prices for consumers.
- The 2005 explosion at the BP Texas City Refinery in Texas City, Texas, caused financial losses totaling $1.5 billion.
- A mistake by a Lockheed Martin engineer (confusing feet and meters – a metric conversion) resulted in the loss of the Mars orbiter in 1999. The cost to NASA? $165.6 million.
According to The Guardian, one of the most expensive accidents – the Deepwater Horizon explosion, fire, and oil spill – cost BP over $65 billion (The Guardian, “BP’s Deepwater Horizon Bill tops $65bn,” January 16, 2018). Of course, the cost in dollars doesn’t account for the 11 people who lost their lives. On top of that is the environmental damage that will never be entirely known.
But you might say, the Deepwater Horizon accident (or the others listed above) didn’t happen to my company. Ask yourself this:
What accidents and incidents (mistakes) did happen at
your company and what did they cost?
What were the costs of:
- Fatalities and lost time injuries?
- Needless equipment repairs?
- Lost production due to equipment stoppages?
- Rework of manufactured products?
- Returned products due to quality issues?
- Regulatory fines or stop-work orders?
- Delays in permits/government approvals?
- Production upsets?
- Lost business due to schedule slippage/late shipments?
- Project delays and rework due to construction mistakes?
- Replacing people who quit after an accident and retraining their replacements?
- Bad press after accidents (reputation loss)?
- Insurance?
What is the total cost of these accidents/incidents/errors for your company?
But costs aren’t the only reasons that you need the best root cause analysis.
Reason #3 – Avoid Jail Time
If you think that jail time is a remote possibility after an accident, then you should read these articles about criminal charges after accidents. They range from a forklift accident to the Deepwater Horizon accident and many other accidents in between. And these criminal charges are happening all around the world (not just in the USA).
- Forklift driver jailed after a fatal accident
- Criminal Charges After the Flood – Are They Justified?
- Will Criminal Charges Make Actors Safer?
- Food Safety & Criminal Charges
- Calls for Major Improvements in Patient Safety and Criminal Prosecution of “Wrongdoers”
- Tugboat Pilot Gets One Year in Jail
- Be a Safety Manager – Go To Jail
- Three Engineers Jailed Over Factory Incident
- Three Directors Found Guilty in Criminal Prosecution After an Accident in Ireland
- Ship’s Pilot Sentenced to 10 Months in Jail for Cosco Busan Accident/Oil Spill
- Criminal Prosecution of an Error
- PG&E Pleads Not Guilt in San Bruno Blast Case
- BP Pleads Guilty to Manslaughter and Agrees to $4 Billion Criminal Fine
If that isn’t enough, a Houston DA said that she wanted to hold polluters accountable with criminal charges and make an example of them. Read this article:
Avoiding jail time is a great reason to use the best root cause analysis techniques.
Reason #4 – Save Time and Effort
It is much easier to learn from a precursor incident and prevent a major accident than it is to investigate a major accident and learn from it.
How much easier?
investigating a typical precursor incident takes a couple of people working for a week to a month. Let’s call that 40 person-days of effort. The budget for the investigation? Typically less than a few thousand bucks (for special testing or other contactor assistance).
What does a major investigation cost? The U.S. Chemical Safety Board had multiple investigators spend years investigating the BP Texas City Refinery explosion. The total cost was over $2 million. This probably bounds the cost of any investigation you would do.
But the point is clear. Precursor investigations are easier and cheaper than major accident investigations. And if you do the investigation right, with the best root cause analysis techniques, you can save a bunch of time, effort, and money by putting your accident prevention efforts on precursor incidents.
What is the Best Root Cause Analysis System?
For some, that is a difficult question to answer. They may want to do a comparison of some of the common root cause analysis techniques like the one at this link:
Comparing Common Root Cause Analysis Techniques (Updated)
But for me, the answer is easy:
The TV segment below explains a little about my reasoning for TapRooT® being the best root cause analysis technique…
But that just a start. Here are some other things to consider:
Why is TapRooT® Root Cause Analysis Software the Best Choice?
TapRooT® Root Cause Analysis – Changing the Way the World Solves Problems
Or you can review some of our TapRooT® User Success Stories:
Chemical Industry Success Story
Pharmaceutical Industry Success Story
But that’s not all. We guarantee our training…
Our Guarantee:
Attend a TapRooT® Course, go back to work, and use what you have learned to analyze accidents, incidents, near-misses, equipment failures, operating issues, or quality problems. If you don’t find root causes that you previously would have overlooked and if you and your management don’t agree that the corrective actions that you recommend are much more effective, just return your course materials/software and we will refund the entire course fee.
Want to learn more about how TapRooT® root cause analysis can help you? Call us at 865-539-2139 or CLICK HERE to have us help you apply the best root cause analysis to your problems to achieve success.
And for our list of public TapRooT® Training around the world, see:
https://www.taproot.com/store/Courses/