What is Stopping Human Error All About?
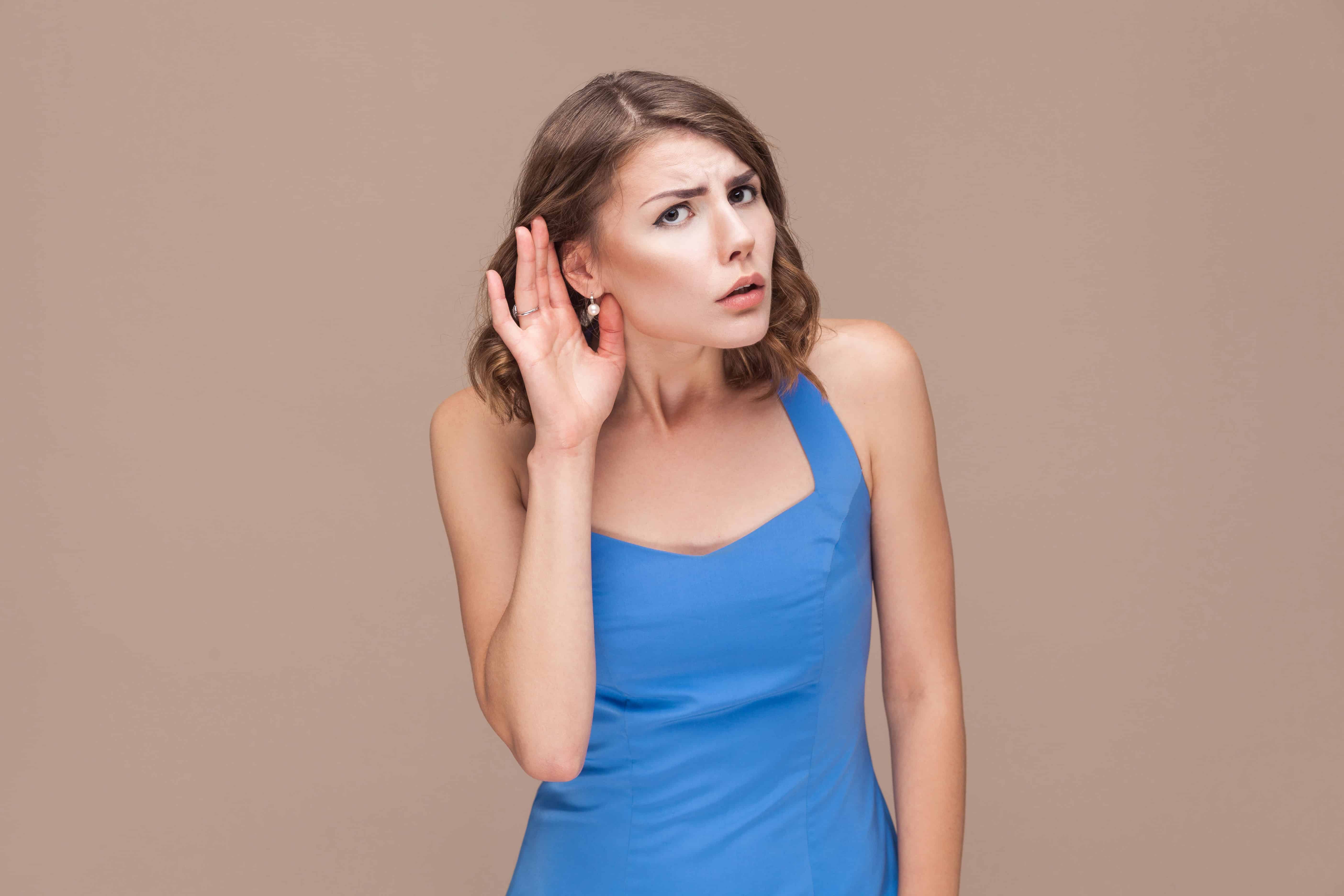
What is Stopping Human Error All About?
When I wrote a book titled Stopping Human Error, several people told me:
You can’t say that!
They said that it was impossible to stop ALL human errors.
Of course, they were right.
But the title of the book isn’t:
Stopping ALL Human Errors.
The point of the book and our course (also titled “Stopping Human Error“) is that you can stop some human errors and thereby prevent major accidents, significant losses, patient safety incidents, and other costly failures.
The History of Human Performance Improvement

In the 80s, after the accident at Three Mile Island, the nuclear industry started a push to improve nuclear plant performance. This push was led by the Institute of Nuclear Power Operations (INPO). They had some good ideas. I participated in the review of INPO’s HPES System and contributed to the Management System evaluation piece.
With good ideas came some bad ones. Some of the techniques developed and spread throughout the nuclear industry were not very effective. They were blame-oriented and not based on human factors principles.
Also, in an attempt to cover all the problems, the human performance (HU) tools became unwieldy. There were too many tools with too many triggers, and they were just too hard to implement.
Finally, even with many tools, they overlooked many important human factors principles and, thereby, failed to correct human factors problems, which caused many errors.
This led to some being dissatisfied with the human performance improvement program (including many operations folks who saw it as blame-oriented).
Below are Mark and Benna in 2019 talking about the history of human performance improvement and the best tools you can use to improve human performance at your company.
This work, which Mark mentioned in the video, took several years and was the final book in the ten-book set that documents the TapRooT® System.
The Stopping Human Error Course will help you learn the techniques and build an effective, custom process to improve human performance at your facility.
When is the next course? CLICK HERE to find out.
What’s in the Stopping Human Error Course?
The Stopping Human Error Course explains how to use the human performance best practices built into the TapRooT® System and the best practices from the nuclear industry and other industries to develop a human performance improvement program to stop human errors. It also explains the problems built into some of the common nuclear industry techniques so that you can make an intelligent decision about which techniques NOT to use.
This isn’t a “one size fits all” program. After taking the course, you will use your knowledge of your facility’s issues to pick just the right techniques to get the most bang for your buck in your improvement efforts. You can decide which strategies you will implement first and the pace of your improvement so you don’t overwhelm your managers and workers with too many new initiatives at once.
At the end of the course, participants will present their improvement plan to benchmark it with other participants and get feedback from the instructors so that the ideas they bring back to work to their managers to implement have been refined and are ready for management approval.
CLICK HERE for the course outline.
With the exercises built-in to try the techniques, this is an active, quick-moving 2-day course.
If you would like to:
- Evaluate your current human performance improvement program or
- Develop a custom program from scratch to help you Stop Human Errors
Then you need to register for this course NOW!
EVEN MORE Human Performance Improvement Information
The 2025 Global TapRooT® Summit has a track titled:
Human Performance Best Practices Track
It has even more information about improving human performance and networking with people interested in HOP, learning teams, and human performance improvement. What sessions are in this track?

For more details about these sessions, CLICK HERE.
The Summit also has five motivating, informative Keynote Speakers.

To see their bios and talk details, CLICK HERE.
The pre-Summit Courses are on September 29-30 and the Summit is on October 1-3. Both are being held at the Knoxville Convention Center in downtown Knoxville, Tennessee.

CLICK HERE to register for the Summit.
I’m Korean and I’m working at oil company as a safety engineer. I’m interested in the book you introduced,”Stopping human error”. It is difficult to attend the training course, but can I buy the book separately?
Yes
Watch for it being released by Mid-March. We’ll post something on the blog and in the newsletter.
Mark
Mark,
I haven’t looked at Tap Root since 2006 because it was light on for human performance so I opted to use other methodologies. Please can you share how you have modified the sheet and the guidebook to improve the ability of RCA Facilitators to get to the root cause?
I see that you went to a 2-Day TapRooT® Course back in 2006. That is a basic course and we don’t explain the human factors link in TapRooT® RCA in that course. It is built-in and easy to use and doesn’t require any special explanation to get the benefits from the technique.
The 5-Day TapRooT® Advanced Root Cause Analysis Team Leader Course does a much better job explaining all the human performance analysis concepts built into the TapRooT® System.
The new Stopping Human Error book and course explains the link in even more detail as well as other techniques to improve human performance.
I am one of the developers of TapRooT® RCA and my background is in Human Factors. Here is some of my experience:
Mark Paradies has 40 years of experience in high-reliability organizations, process safety, incident investigation, human factors, and root cause analysis. His career started as a leader in Admiral Rickover’s Nuclear Navy (where he earned Engineer Qualification). He also worked for DuPont in the areas of human factors, process safety, and performance improvement management before he started System Improvements in 1988. Mark was one of the co-creators of the TapRooT® System. Mark worked with Linda Unger and Dr. Paul Haas on a contract to develop the Nuclear Regulatory Commission’s Human Performance Investigation Process. He has a BS in Electrical Engineering and an MS in Nuclear Engineering (with an emphasis on human factors), both from the University of Illinois.
His human factors and human error analysis experience includes:
• Masters Degree in Nuclear Engineering with an emphasis on Human Factors from the University of Illinois (1985)
• Research on the proper role of automation in the next generation of nuclear power plants (1983-1985)
• Member, Human Factors & Ergonomics Society, (1983-Present)
• Developing a Human Performance Improvement Program at DuPont (1985-1988)
• Contributed to INPO’s Human Performance Evaluation System (HPES) (1986)
• Co-Developer of the TapRooT® Root Cause Analysis System (1988-Present)
• Co-Developer of the NRC’s Human Performance Investigation Process, HPIP (1990-1993)
• The 85th Certified Professional Ergonomist, the first human factors professional certification (1993)
• IEEE Human Factors Committee Member and Co-Author: IEEE Root Cause Analysis Standard (2010-2017)
• Committee Co-Author: Recognizing and Responding to Normalization of Deviation, CCPS
• Committee Co-Author: Guidelines for Investigating Chemical Process Incidents, 2nd & 3rd Editions, CCPS
• Author of the book, Stopping Human Error (2020)
For more on the human factors concepts built into TapRooT® ® RCA, see:
https://www.taproot.com/about/history/
I hope that helps you understand the strength of the knowledge of human factors and human performance analysis that is built into the TapRooT® Root Cause Analysis System.