Are You Part of the Problem or Part of the Solution?
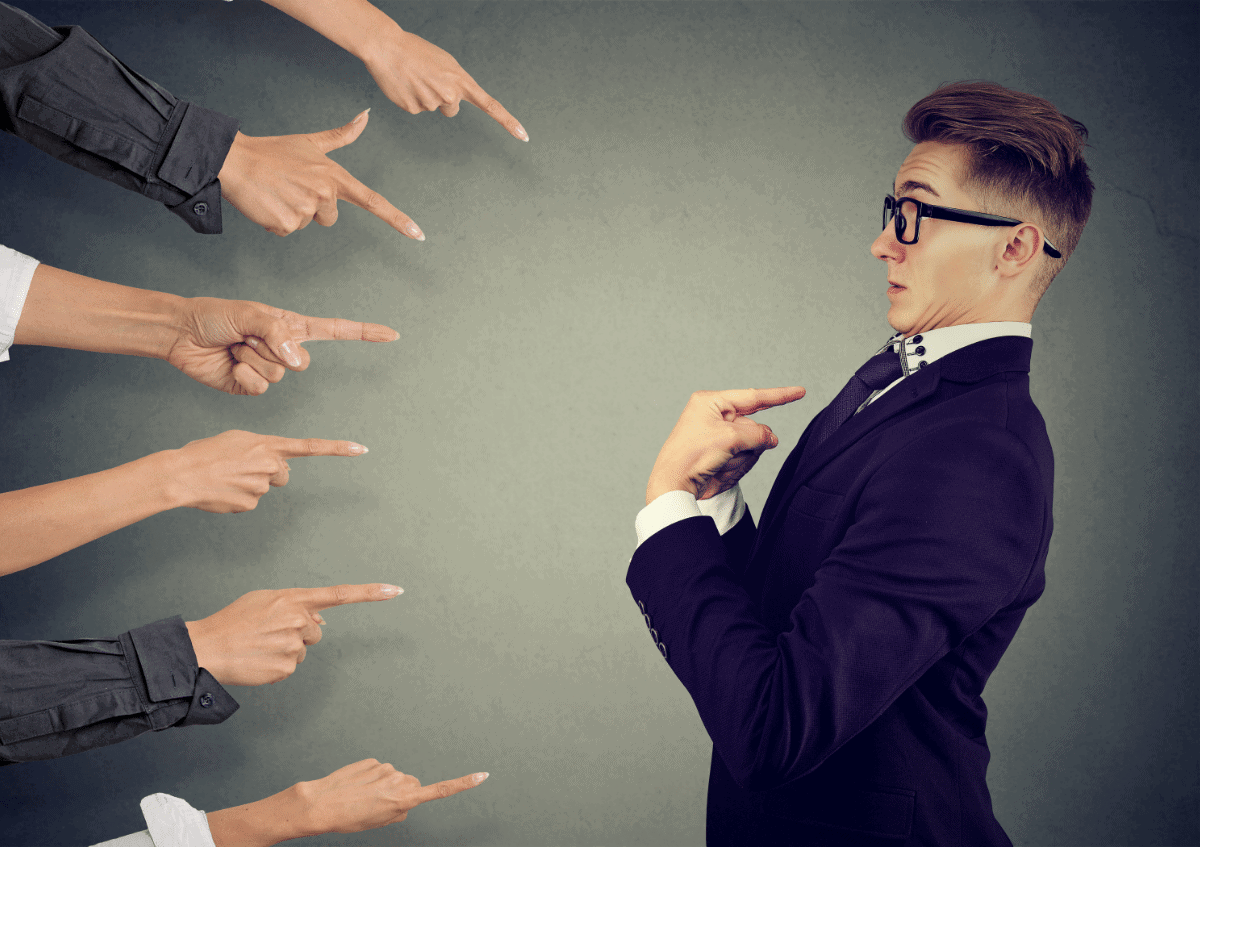
Keep Your Job – Be Part of the Solution
It’s rare that senior managers get fired after a major accident. Usually, if they are thought to be “part of the problem,” they get transferred to another job with little responsibility, and they are never heard from again.
But, if they are seen as part of the solution, they can keep their job and even get in line for their next promotion.
How does this work? Read on to see.
The Major Accident
You know it is a major accident if:
- The corporate board knows about it.
- It is front-page news in the local paper or the nightly news.
- It affects the stock price.
- The NTSB, CSB, NRC, OSHA, or the EPA send a team of investigators.
- The Wall Street Journal covers the accident.
If any of the above happens, managers might start worrying about BLAME.
BLAME
It’s not only the managers that need to worry about blame. Everyone in the chain of command needs to worry. From the operator/mechanic to the plant manager (and perhaps even those above the Plant Manager) may be in line for some blame.

Worrying about blame is especially true if you don’t have any ideas about how to prevent the accident from happening again.
Part of the Solution
However, if you have trained your investigators and led the effort to understand what happened and find and fix the root causes of the accident, you become part of the solution.
You become a valuable part of the management team because you know the answers that can help the company avoid future problems.
That’s why you want you and your investigators to be thoroughly trained in using the TapRooT® Root Cause Analysis System. TapRooT® RCA can help you discover the real, fixable root causes of the problem and clearly communicate the solutions without placing blame.
See the upcoming public TapRooT® RCA Courses at THIS LINK. Or get a quote for a course at your site by CLICKING HERE.
Even Better – Prevent the Accident By Being Proactive
An even better way to stay out of the blame crosshairs is to prevent the accident from occurring. You might think that is Mission Impossible, but you don’t have to be Tom Cruise to achieve success.
If you want to find out how to proactively prevent human errors (the #1 cause of big accidents), then you should attend the 2-Day Stopping Human Error Course. Or you could attend the 2-Day Auditing & Proactive Improvement Using TapRooT® Course.

Both of these courses are being held on April 24-24, just before the Global TapRooT® Summit. Get information about all the pre-Summit Courses by CLICKING HERE.
And get complete Global TapRooT® Summit information by CLICKING HERE.
I believe the premise of stopping human error is a fallacy. Humans will make errors. The task is to allow those errors to happen without negative consequence, e.g. fail safely (T.Conklin)
Thanks for your comment and my answer is … Yes and No.
You can stop some human errors. We have two examples in the Stopping Human Error Course where changes are made and frequent errors go to ZERO errors.
But we also teach resilience and making errors detectable and correctable. (Not progressing to a serious problem. Fail but correct to a safe state.)
In addition, we teach hazard elimination and target elimination which can eliminate consequences. And substitution – to reduce consequences.
All of this, including the best techniques and those that don’t work so well, is summed up in the Stopping Human Error Course.
I think you would find it interesting and eye-opening, especially if you are interested in Todd’s work.
Best Regards,
Mark