Stop Re_______ Corrective Actions
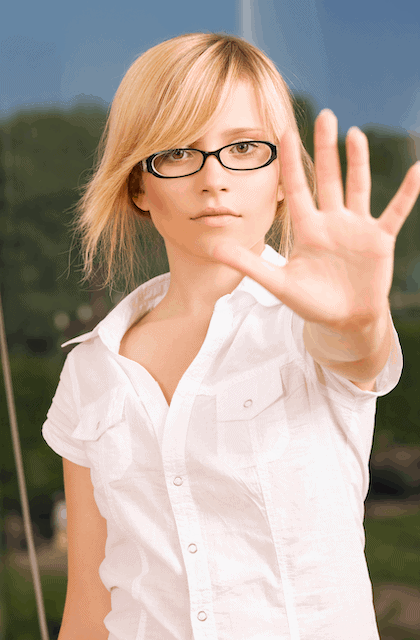
Make Your Corrective Actions Effective
I’ve seen a lot of “re” corrective actions …
Re-train
Re-emphasize
Re-place a part
Re-mind people about rules
Re-qualify (after you disqualify)
Re-write the procedure
Think about this …
If it didn’t work the first time, why will it work this time?
Instead of using a “re”, why not fix the problem? What caused the first training, emphasizing, part, rule, qualification, or procedure to fail?
Consider a more effective Safeguard.
Remove the Hazard or remove the Target.
Then you might not have REpeat incidents.
Learn More About Effective Corrective Actions
Where? At a TapRooT® Root Cause Analysis Course.
Where are these courses? We hold public TapRooT® Courses all around the world and virtually.

Learn to use the Corrective Action Helper® Guide/Software Module to develop more effective corrective actions that fix the incident’s root causes.
Learn to use the Safeguard Hierarchy and SMARTER to improve your corrective actions.
And don’t forget that TapRooT® Training is guaranteed…
Attend the TapRooT® RCA Training, go back to work, and use what you have learned to analyze accidents, incidents, near-misses, equipment failures, operating issues, or quality problems. If you don’t find root causes that you previously would have overlooked and if you and your management don’t agree that the corrective actions that you recommend are much more effective, just return your course materials and we will refund the entire course fee.
One more idea. You can schedule a course at your site. Hold it with live instructors in-person or virtually. For a quote, call us at 865-539-2139 or send an e-mail by CLICKING HERE.

Corrective Action Guide Books, How much and how to order please?
Thank and regards.
They come with a complete set of TapRooT® Books. See various options at:
https://store.taproot.com/taproot-investigation-essentials-book-set
https://store.taproot.com/major-investigations-book-set
https://store.taproot.com/taproot-investigation-essentials-and-major-investigations-book-set
https://store.taproot.com/taproot-books-1-10-book-set
https://store.taproot.com/books