Distracted Pilot of Slingsby T65A Vega Loses Control Due to Loose Canopy
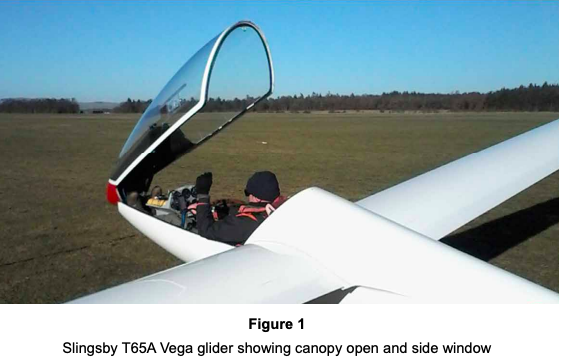
A pilot lost control of the glider and struck the ground after the canopy on the Slingsby T65A Vega became insecure soon after takeoff.
The canopy had not been secured properly during the pre-flight preparation due to the pilot, and a person assisting him with the canopy on the Slingsby T65A Vega, being distracted.
History of the Slingsby T65A Vega flight
The canopy on the Slingsby T65A Vega has an opening hinge on the nose of the glider and opens vertically at the rear (Figure 1).

The canopy lock is located on the top of the fuselage behind the pilot’s head. The pilot commented that it was not possible for him to lock the canopy, or to see the locking indicator, when seated in the glider due to his stature and his requirement to use a seat back He would normally be assisted by his syndicate partner in lowering the canopy, engaging the lock, and checking that the indicator button was flush. The syndicate partner would then say, “canopy closed and locked.” When the syndicate partner was not available, the pilot would ask for assistance from someone else and brief them this procedure.
The accident flight
On the day of the accident, the syndicate partner was not available, so the pilot
obtained assistance from a gliding club member who he briefed on the canopy locking
procedure.
The pilot stated that as he was distracted talking to the club member, not fully focused on his flight, he did not complete his cockpit pre-flight checks correctly. As the club member was also distracted by the conversation with the pilot, he did not complete the canopy-locking procedure. However, the pilot convinced himself that when the canopy was closed, it was also locked.
Read the full AAIB report, “Vickers Slingsby T65A Vega, G-EECK,” here.
Through TapRooT® RCA Training, we can help your management understand how advanced root cause analysis works and how it can help your site/company achieve excellence.
It starts with a FREE executive briefing. Visit our Executive Portal to request a free, 1-hour Executive Briefing. TapRooT® Root Cause Analysis was developed to meet the proven requirements for systematic root cause analysis. We can help you implement the proven TapRooT® process. Dan Verlinde prepared this graphic to help you implement TapRooT® Root Cause Analysis in your improvement process. We will work with you to develop your custom plan.
Register for a TapRooT® Root Cause Analysis Training Course.
TapRooT® Root Cause Analysis Training courses are taught all over the world. If you are interested in learning how to stop repeat incidents, find a 2-day or 5-day course. We are available to train you and your staff on-site at your workplace; contact us to discuss your needs. You may also call us at 865.539.2139.