Equipment Failure, or Human Performance Failure?
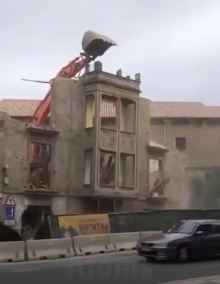
Equipment failure is prevalent throughout our industries.
It happens almost every day — equipment failure, that is. Sometimes it is something simple (such as a corroded switch preventing a pump from starting). Or it can be a major issue (such as an oil rig top drive failure).
The fact that we have some equipment failure is not surprising. However, the corrective actions we often put in place are very frequently focused on the wrong problem.
For example, take a bearing failure. In most cases, the corrective actions I’ve seen revolve around repairing the bearing. The thinking behind this is, We’ll install a new bearing, maybe increase monitoring of the bearing, and perhaps even check our supply system to make sure we have additional spares in place. However, these corrective actions all revolve around the physical equipment failure: We fix the bearing. Unfortunately, this focus on the physical cause frequently leaves us open to future repeat failures of the same piece of equipment.
This often occurs for 1 of 2 reasons:
- We don’t consider the human performance issues that led to the equipment problem;
- We don’t do a good job looking for generic causes.
Let’s look at these equipment failure cases in more detail.
Human Performance Issues
When a bearing fails, it is too easy to just identify the particular failure mode. “The bearing failed due to inadequate lubrication.” Our corrective actions then focus on repairing the bearing and using the correct lubricant upon completion of the repair. However, why was the wrong lubricant used? This should be the focus of our corrective actions. Somehow, a really smart mechanic used the wrong grease, and this then led to the equipment failure. We should be focusing our investigation on what in our systems allowed this person to use the wrong grease. Have we considered:
- Did we purchase the correct grease for the application?
- Did the procedure specify the correct grease?
- Was a supervisor available to assist this relatively new mechanic?
- Did anyone check to make sure we were using the correct grease?
- How was that grease stored and labeled?
Just replacing the bearing and properly greasing it will NOT prevent a future recurrence. Another mechanic could quite easily use the wrong grease again the next time a lubrication PM comes up. By ignoring the human performance issues, we barely scratch the surface of the potential corrective actions that would permanently prevent this issue in the future. Research has shown that over 90 percent of equipment failures are actually human performance failures!
Address Generic Causes
We also need to check if this issue has a generic cause. For example, if we decide that the wrong grease was used because of the confusing way it was kept in the storage cabinet, we need to not only look at that particular storage cabinet, but also how we are storing our lubricants elsewhere in our facility.
- Do we have other storage cabinets?
- Do we have multiple lubricants stored in these other cabinets?
- Are the lubricants properly labeled in these other cabinets?
The answers to these questions will ensure we don’t only fix this one instance of improper storage but we address other possible areas where lubricants are also improperly stored. Generic cause analysis will pick up these other potential similar issues.
Equipment failure is a fact of life at our facilities. However, you should not be content to have similar repeat failures. By addressing both human performance issues and generic causes, you’ll more thoroughly apply corrective actions that will prevent further downtime of your equipment.
TapRooT® Root Cause Analysis/Equifactor® is the only system that uses scientifically derived root causes to eliminate bias and avoid blame (also while addressing equipment failure).
Safety and quality experts know from personal experience that TapRooT® Root Cause Analysis is the best option to get human-performance-based root causes. What they don’t know is that the Equifactor® Equipment Troubleshooting Module should be used whenever there is an equipment failure.
When using the Equifactor® module of the TapRooT® Software, you have the opportunity to store some very specific data in each symptom or possible cause that can help your equipment experts with their troubleshooting efforts. Each of these Equifactor® items has an associated Equifactor® Reference area that allows you to store your own custom data.
We have a team of investigators and instructors who have years of extensive training ready to offer assistance worldwide. We also offer ongoing support to our clients through free newsletters and root cause tip videos, the Root Cause Analysis Blog and our annual Global TapRooT® Summit. We’re here to find solutions for you.
Need phone support? Office hours are 7 am to 6 pm EST M-F. Contact us: 865.539.2139.