Alaska Airlines Success Story
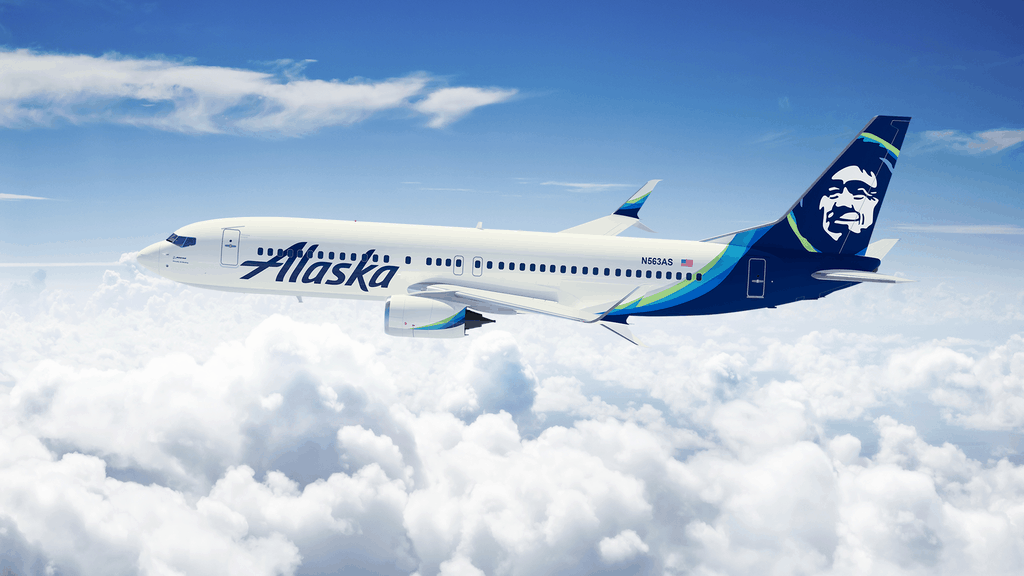
Success Story: Improving Root Cause Analysis at Alaska Airlines
Submitted By: David Prewitt, Vice President, Safety
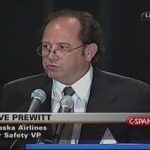
Alaska Airlines Success Story: This success story was written in the past (2005) and is being updated to our most recent blog article format and reposted here. Sorry that the video quality is poor, but video technology has improved greatly in 19 years. The example shows how TapRooT® Root Cause Analysis can help improve incident investigations and root cause analysis at an airline that is implementing system safety. These lessons apply today just as much as they did when this was first written, and the video was recorded. One last comment … in the video, everyone certainly looks younger!
Challenge
In 2001, we started implementing system safety. We realized we needed improved root cause analysis for incidents and audit findings.
Action
We implemented the TapRooT® Root Cause Analysis System and Software as part of the internal evaluation program to identify the root causes of problems before accidents or incidents happen. This includes aviation safety, ground safety, and even operational issues that cause significant flight delays.
Results
We started identifying root causes that we previously would not have identified. This helped us improve safety, quality, environmental responsibility, and productivity.
Watch the video below to see how TapRooT® Root Cause Analysis helped us at Alaska Airlines improve performance.
Here is a video from 2004 of a talk by David Prewitt, VP of Safety at Alaska Airlines, at the Safety Conference of the Air Line Pilots Association (ALPA). The talk is about Alaska Airlines’ implementation of system safety and mentions how TapRooT® RCA is built into their performance improvement initiatives.
Comments from Mark Paradies
If you listen closely to the second video, you might have heard Dave say that TapRooT® RCA isn’t perfect. That’s just like Dave; he always works to improve his performance. In 20 years since that video, we have worked hard to make TapRooT® Root Cause Analysis much more perfect than it was in 2004. I would say the biggest improvement that David would point out is our software. Back in the early 2000s, Alaska Airlines was using our TapRooT® Software Version III. That was a PC-based software. Today, we have improved to TapRooT® Software version VI – a cloud-based software that is platform-independent and much easier to use, administer, and connect to other software.
Also, back then, we used the old TapRooT® green book and materials.
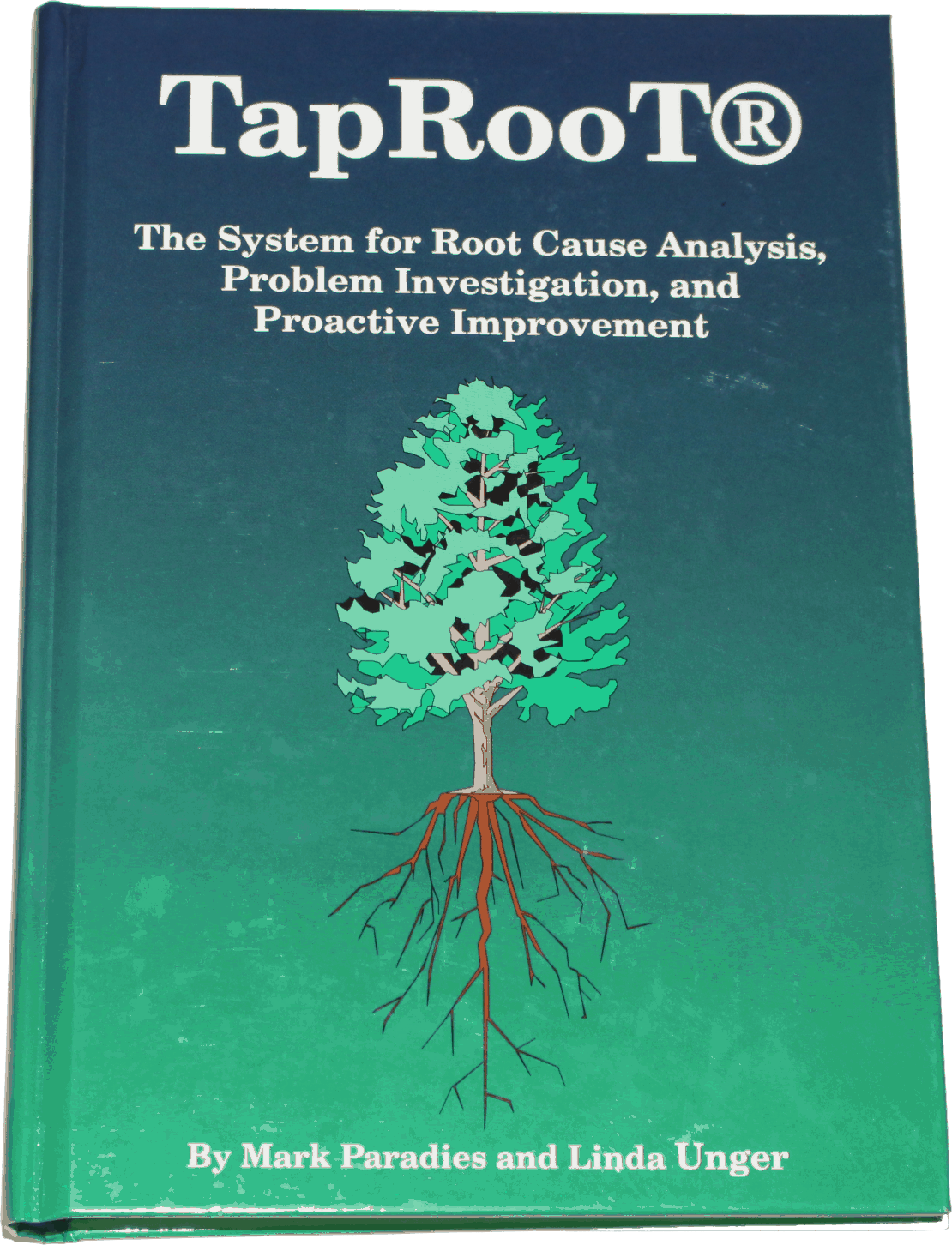
Today, we have progressed to a new set of books documenting the TapRooT® System for root cause analysis and proactive performance improvement. The books are shown below.
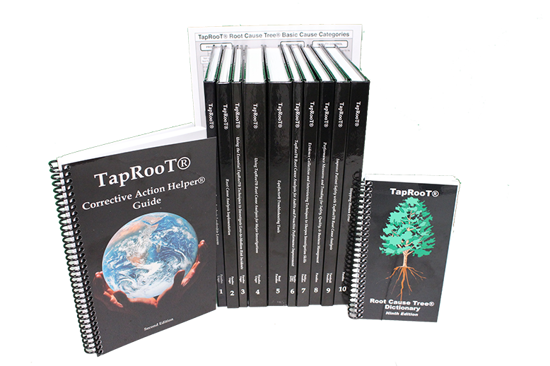
Once again, we have improved our documentation and training to make TapRooT® Root Cause Analysis THE root cause system for industry leaders.
The biggest improvement to the documentation and training since 2004 is probably the revision that allows TapRooT® RCA to be applied flexibly for audits, simple incidents, or major accidents. For more information about how TapRooT® can be applied flexibly for low-to-medium risk incidents, see THIS LINK.
Learn More About Advanced Root Cause Analysis
To learn more about TapRooT® Software, see THIS LINK.
To learn more about TapRooT® Root Cause Analysis Training, see THIS LINK.
To see the dates and locations of upcoming public TapRooT® Root Cause Analysis Training, see THIS LINK.
And don’t forget, TapRooT® Root Cause Analysis is GUARANTEED…
COURSE GUARANTEE
Attend TapRooT® Root Cause Analysis Training, go back to work, and use what you have learned to analyze accidents, incidents, near-misses, equipment failures, operating issues, or quality problems. If you don’t find root causes that you previously would have overlooked and if you and your management don’t agree that the corrective actions that you recommend are much more effective, just return your course materials and we will refund the entire course fee.