Food Safety Repeat Problems … Is Your Root Cause Analysis Inadequate?
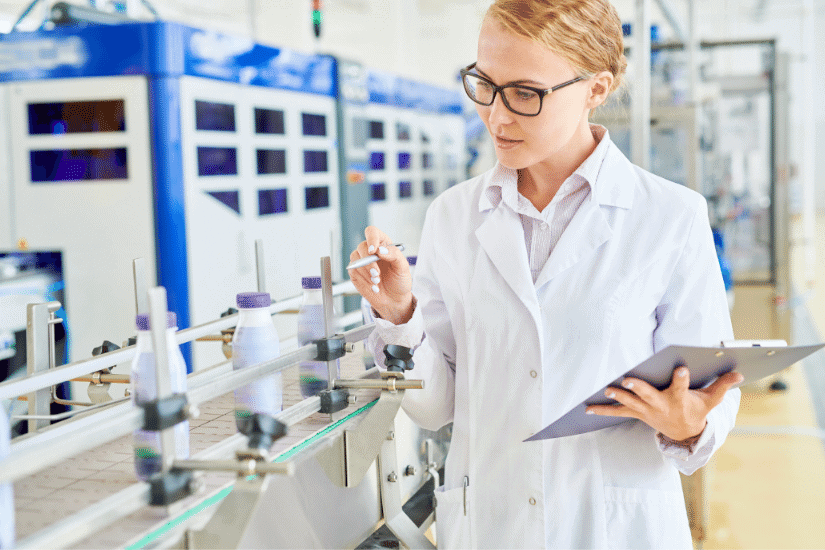
Indications of Inadequate Food Safety Root Cause Analysis
I saw an article in Food Safety Magazine that implied that many food safety issues at many sites are repeat problems. That is, the problems have been identified before, an analysis was completed, and corrective actions were implemented, BUT the incident happened again. In other words, the corrective actions were NOT effective. These companies need to be interested in food safety root cause analysis.
Repeat incidents after investigations are probably due to ineffective root cause analysis. This can be caused by:
- Poor understanding of what happened.
- Jumping to conclusions.
- Inadequate identification of all the Causal Factors.
- Poor root cause analysis – especially of human performance problems.
- Poor Generic Cause analysis.
- Inadequate corrective actions.
- Corrective actions that were too low on the Hierarchy of Safeguards.
- Corrective actions that weren’t implemented.
That’s quite a list! But we find that all of those items are common in most food safety root cause analyses. Maybe they are using this root cause analysis method…
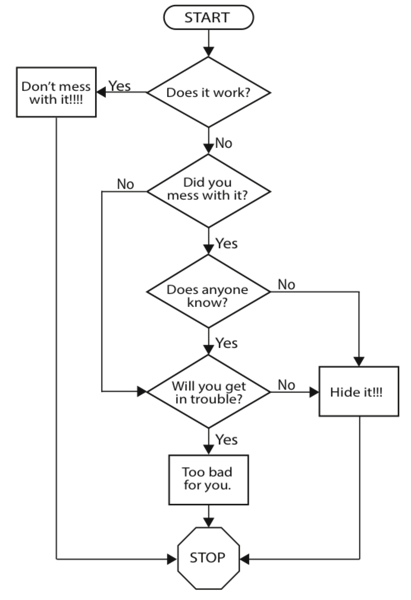
Common Root Cause Analysis Problems
Why are these problems common?
- People, and even industry associations, recommend common faulty root cause analysis tools like 5-Whys and Fishbone Diagrams.
- Companies choose inadequate root cause analysis systems.
- Companies don’t train their people in advanced root cause analysis.
- People don’t know how to develop effective corrective actions.
- Management doesn’t do effective reviews of the company’s root cause analyses.
- Management doesn’t track and ensure the implementation of the corrective actions that are approved.
- Management doesn’t verify the effectiveness of corrective actions.
For more about these problems read these articles:
- Comparing 5-Whys with Advanced Root Cause Analysis
- Are You Dissatisfied with 5-Whys Root Cause Analysis?
- Fishbone Diagram Root Cause Analysis – Pros & Cons
- How Effective is Your Food Safety Root Cause Analysis Process?
- What happens when root cause analysis becomes too simple? Six problems I’ve observed.
Or for the secrets of good root cause analysis, sign up for this free webinar on October 14th:
7 Secrets of Root Cause Analysis
Solve These Common Root Cause Analysis Problems
The seven problems listed above are all solvable.
How?
By implementing a well-thought-out, advanced root cause analysis program.
Now the good news. We can help you develop a root cause analysis roadmap to success. And the development of the roadmap is FREE. And when implemented, it will solve your problems.
Root Cause Analysis Roadmap to Success
How can we help you develop a roadmap for free and how do you know the roadmap will be effective? Because we’ve developed thousands of roadmaps for all types of facilities in all kinds of industries.
What does an effective advanced root cause analysis system look like? We would be happy to show you in an executive briefing that explains the system and why it is so effective.
Once you understand the system, you will be ready to develop your roadmap to success.
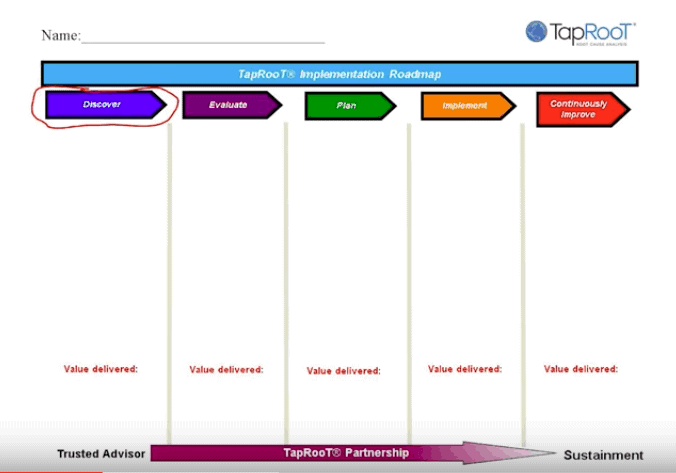
Here is a sample of a completed initial roadmap…
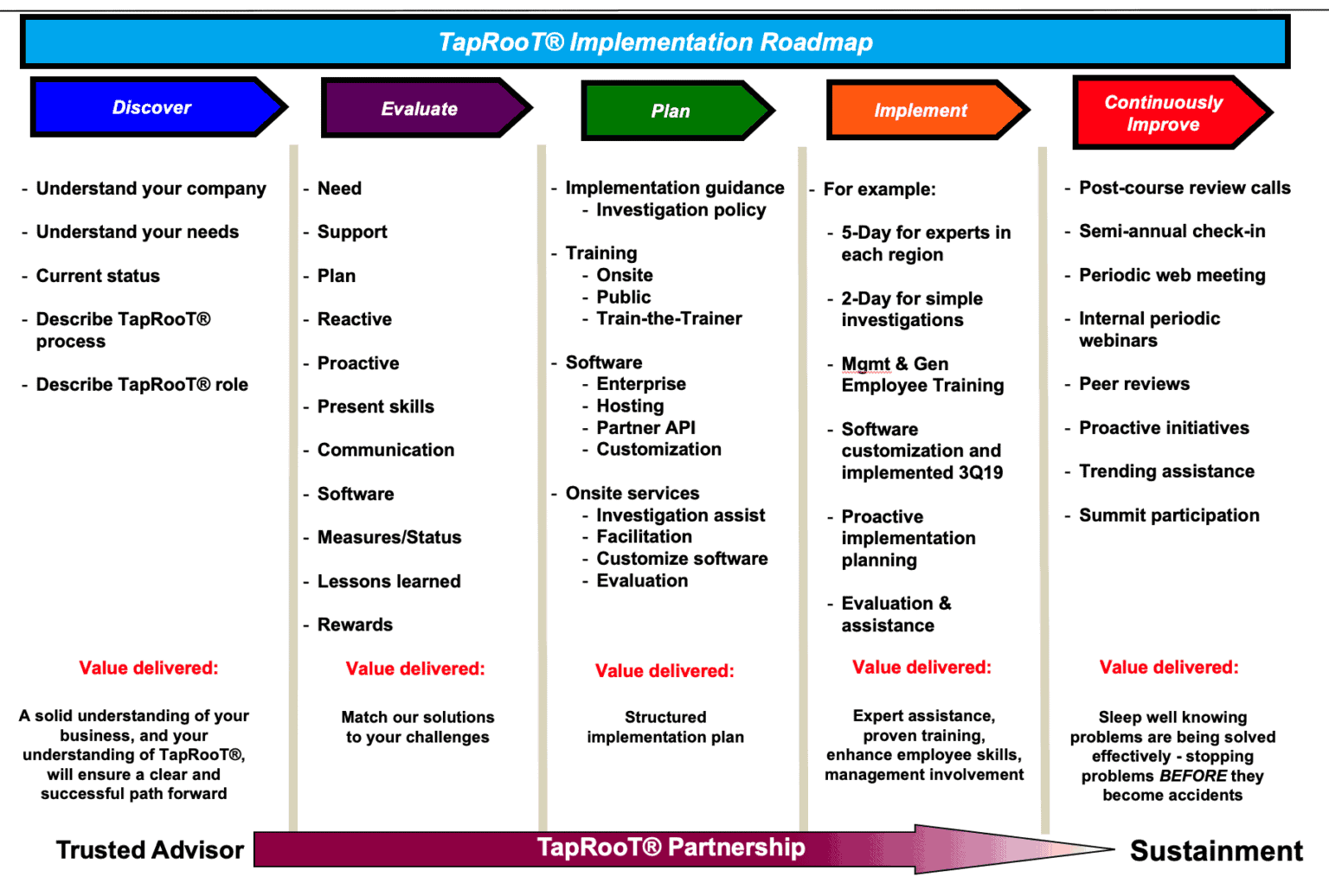
CONTACT US if you would like to end repeat incidents by adopting advanced root cause analysis that meets the fundamental root cause analysis requirements.
Don’t Wait!
Ineffective root cause analysis leads to repeat problems. This can cause serious food safety issues including recalls and even fatalities. To need to get ahead of these problems with effective advanced root cause analysis. Call us NOW (865-539-2139) if you are interested and want to get started ASAP!
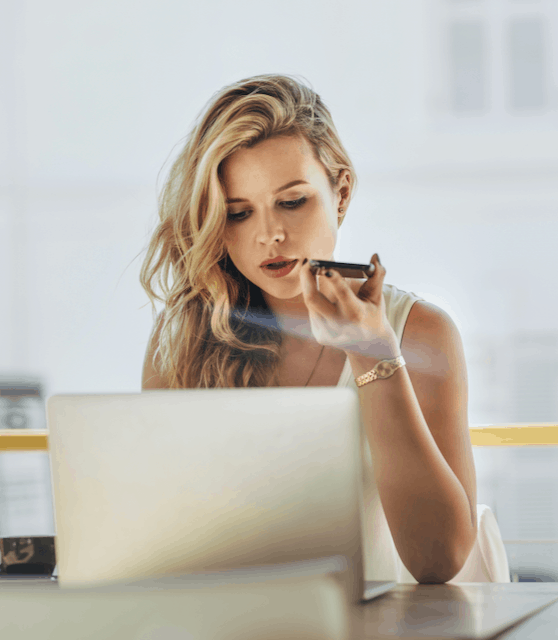