Procedure Usage – When Will They Learn?
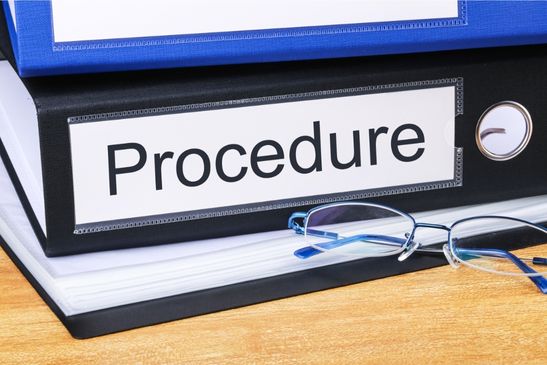
Procedure Not Used
One common theme (near root cause) I continue to hear in major accidents is:
The Procedure Was Not Used
Sometimes:
- They were not using a procedure because no one had written one (so they were winging it).
- There was a procedure, but the operator, supervisor, or mechanic decided they knew better.
- The company culture is that “only trainees use procedures.”
- People don’t understand that using a procedure means reading a step, doing it, and then reading the next step (instead of “doing” a procedure from memory).
I’ve even heard managers say that you CAN’T operate or maintain a plant by procedure – it just can’t be done!
When I talk about procedures, I’m not talking about policies. I’m talking about work-related checklists and detailed written procedures that document how a job is to be performed step by step.
Failure to Use Procedures Causes Major Accidents
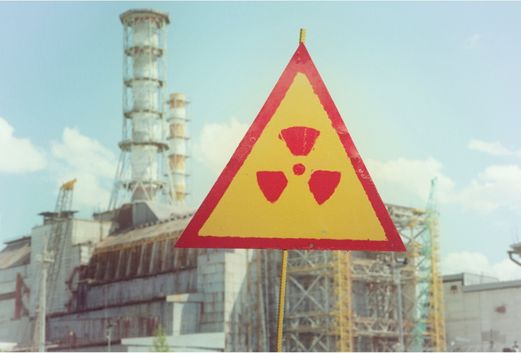
From the BP Texas City Refinery Explosion to Chernobyl, accidents happen when people don’t use procedures.
Look at the list of worldwide major accidents at:
https://en.wikipedia.org/wiki/List_of_industrial_disasters
Imagine how many could have been prevented if the workers had used an accurate, well-written procedure.
What Can Companies Do To Improve Procedure Use?
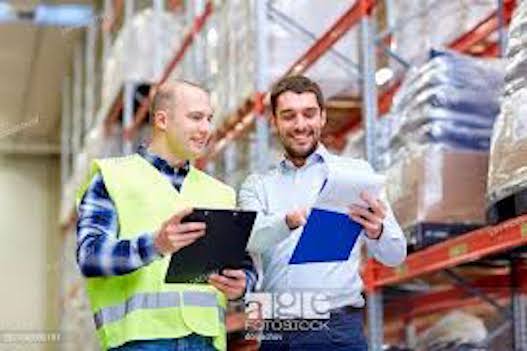
If proper procedure use is such a big deal (and it is), why aren’t companies doing more to encourage operators and mechanics to follow procedures?
What kinds of things should they be doing?
- Investing in well-written procedures that are thorough yet easy to use.
- Making the procedures more available for the plant staff.
- Training people about the importance of procedure usage and what can happen when procedures are not used. This should include the human factors/psychology behind how procedures improve performance.
- Conducting regular supervisor and management audits of procedure usage on all shifts.
- Remote operations monitoring (security cameras) so procedure usage can be checked remotely.
- Developing a rewards program for proper procedure usage.
Is your facility doing anything to ensure that procedures are being used?
If not, your company may be a candidate for a significant accident.
Don’t wait – get going! Start promoting procedure use today!
What Can You Do To Learn More?
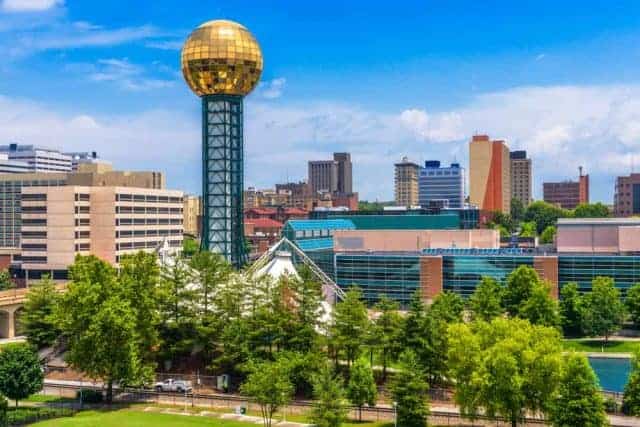
Attend the 2025 Global TapRooT® Summit at the Knoxville Convention Center in Knoxville, Tennessee, on October 1-3. There is a session titled:
Procedure Writing & Use for High-Reliability

This session is included in two of the best practice Tracks:
This is just one of the forty-four sessions to help you improve your company’s performance. See all the best practice tracks at THIS LINK.
Here is another opportunity to learn advanced techniques to improve performance: the 11 pre-Summit Courses, held on September 20-30, 2025. These courses include:
- Analyzing and Adjusting Culture
- 2-Day Advanced Communications/Presentations
- The Best Ways to Use Data to Improve Performance
- 2-Day TapRooT® Root Cause Analysis Training
- 2-Day Equifactor® Equipment Troubleshooting & TapRooT® Root Cause Analysis
- TapRooT® Advanced Case Study Workshop
- Stopping Human Error
- TapRooT® Software Training
- Auditing & Proactive Improvement Using TapRooT®
- Interviewing & Evidence Collection
- 2-Day Developing an Incident Command System
Pick one to attend to get even more knowledge from your trip. Get more information about these courses at THIS LINK. You will also get $300 OFF the combined fee when attending the Summit and a pre-Summit Course. Get an even bigger discount (up to $900 OFF) when you bring a team.
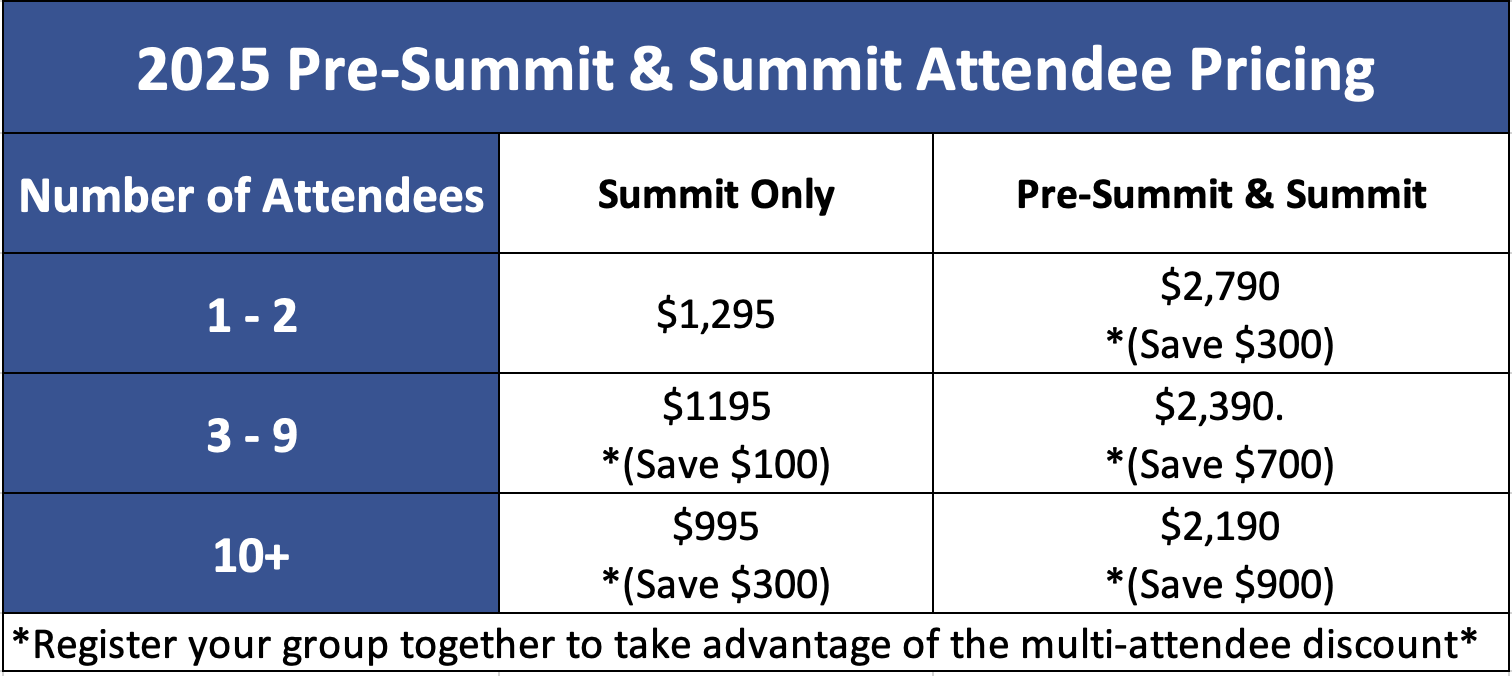
Register for the Summit and a pre-Summit Course by CLICKING HERE.