What I learned at the 2008 Summit
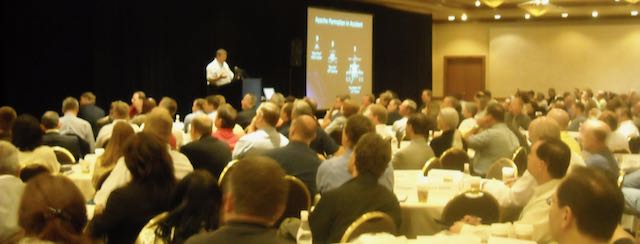
20 Years of System Improvements – So Much to Learn
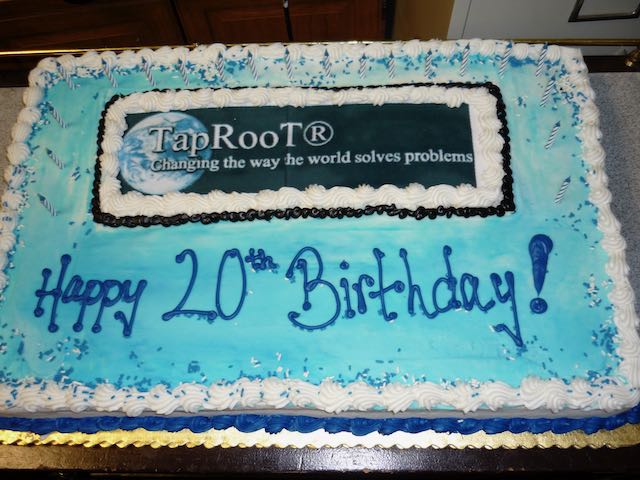
I was so busy at the 2008 Summit that I really didn’t have a chance to take a break from Sunrise to Sunset.
That’s why I didn’t provide minute-to-minute reporting on what I learned at the Summit—I just didn’t have a chance to write.
Ah-Ha Moments
I did take some notes, and I thought that readers might be interested in what I learned. Therefore, I will share my “A-Ha’s” here for everyone to read.
1. I learned from Darby Allen that 5-10% of all profits are consumed by the costs of accidents and incidents. The costs include hidden costs. For example:
- Fines
- Legal
- Investigation
- Productivity Loss
- Retraining
- Lost Production/Missed Orders
- Sullied Reputation
- Hidden Equipment Damage
2. I learned from Dave Prewitt that senior management needs a single source (a single database) that contains all failure data and costs, including audit findings. Senior management can then use the data to build an organization that is resistant to disaster because they proactively ensure that systems are safe.
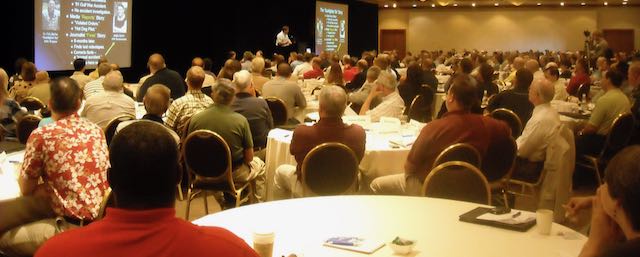
3. I learned from Lt. Col. Hayles that big organizations naturally tend to cover up senior management failings and look for scapegoats when big things go wrong. That this is a natural part of “protecting the mission of the organization”.
4. I received many good ideas about TapRooT® and the TapRooT® Software from the TapRooT® Advisory Board Meeting.
5. I really enjoyed the great people at the Summit and had a wonderful time at the Reception/Birthday Party, where I got a chance to catch up with two old friends – David Busch and Kevin O’Connor.
6. Carolyn Griffith shared that the UK Rail Accident Investigation Board spends seven months training one of its new investigators and that a “no blame” policy is a major part of its investigations.
7. I heard many user best practices at several best practice sharing sessions, including the TapRooT® User Best Practices Session run by Linda Unger and Michele Lindsay. I’ll try to write up these separately later.
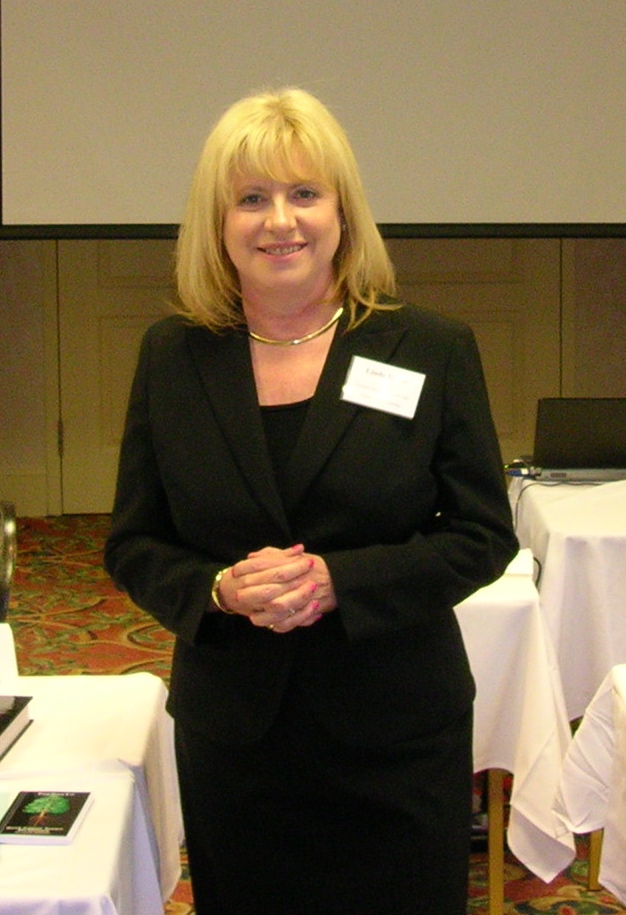
8. I learned from Chris Vallee (Six Sigma Black Belt and TapRooT® Instructor) that SnapCharT®s and Swim Lanes can be combined into a powerful Lean/Six Sigma tool.
9. Even though I had studied the Three Mile Island accident extensively, I could learn much more by listening to an operator who was at the panel (Ed Frederick).
10. I learned from Marcia Wieder that dreams and visions are similar and that fear is the biggest roadblock to achieving your dreams (vision).
11. That I need to practice if I am going to play golf!
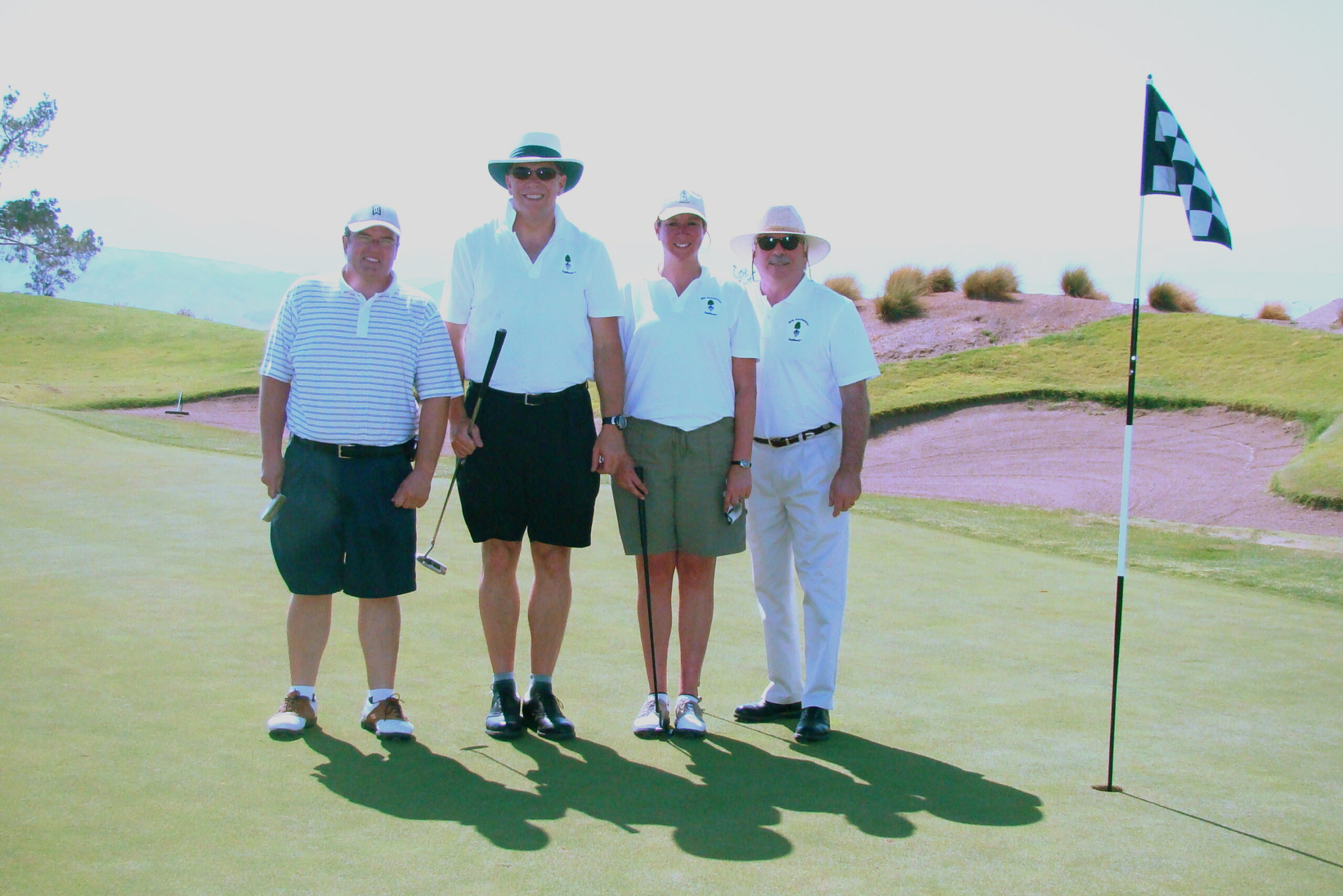
General Summit Lessons Learned
I also learned some things in general about the Summit that others should know about…
1. That there were many outstanding sessions that people told me about (and that I wanted to attend) but that I couldn’t go to. Therefore, bring several people from your facility to cover all the applicable sessions from which to learn.
2. That you should come early and stay late. This helps you learn more.
Start by attending one of the many pre-Summit courses.

Next, come down early in the morning and have a leisurely breakfast while networking with other participants.
Don’t plan to leave early. Plan to stay over Friday night and leave Saturday morning.
3. That people love to share best practices. We had 10 Best Practice sharing sessions at the 2008 Summit that were focused on allowing participants to share their knowledge with others. These were some of the highest-rated sessions of the Summit because the caliber of the attendees at the Summit is so exceptional.
4. That people love to be inspired. Speakers who inspire are always highly rated. Heinz Bloch, Marcia Wieder, Nikki Stone, and Beverly Chiodo inspired their audience and helped people leave the Summit energized to make a difference when they returned to work.
5. That even with a crowd that is as enlightened as people at the TapRooT® Summit, it is hard not to blame people for mistakes. This became apparent after Lt Col. Hayles’s talk. Some of the people I spoke to couldn’t get by his mistake when he pulled the trigger in a friendly fire incident – even though they could see how he was set up for the accident by factors beyond his control. And even though they could see that to prevent future friendly fire accidents, you must go beyond “being more careful next time.”
6. That a hot room for one is a cold room for another. Temperature is an individual preference. (Bring a coat if you tend to feel cold – even to Las Vegas.)
Reinforced Lessons Learned
Here are some things I already knew but were reinforced by the Summit:
1. We have great clients that are industry leaders. I’m always impressed by the discussions we have and how willing participants are to share their best practices.
2. I have a great staff that knows what they are doing, plans well, and handles unexpected changes with panache (style, grace, and a flair for excellence).
3. Even the best in any industry can learn from others, and even the best companies can improve.
4. Even companies with the most to learn have best practices that others can learn from.
5. Some of the most eye-opening lessons come from outside your industry (if you can translate from their terminology to yours).
6. Having a good time and learning are not mutually exclusive activities.
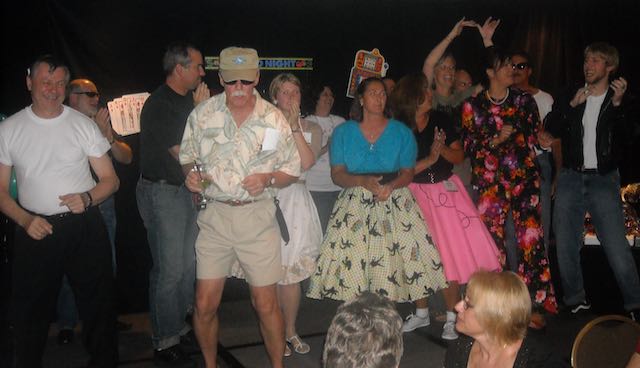
7. TapRooT® RCA really is an exceptional root cause analysis tool that is changing the way the world solves problems.
8. Every facility and company that uses TapRooT® should have someone at the Summit. We guarantee that what you learn will produce a return on investment at least 10 X the cost of your attendance, or you get your money back. So, start planning to attend in 2009!
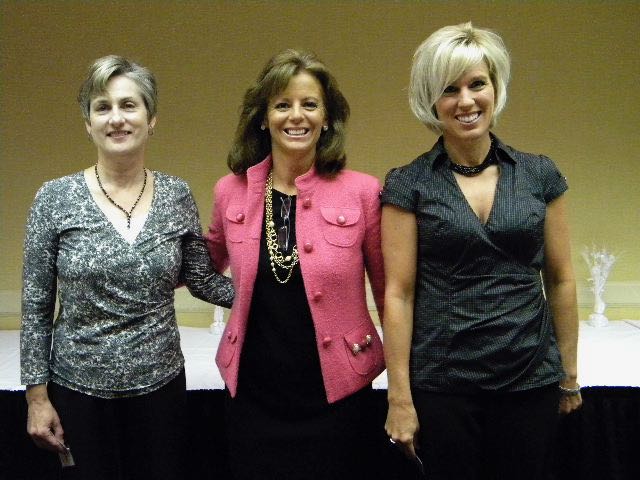