Best Practices for Corrective Actions
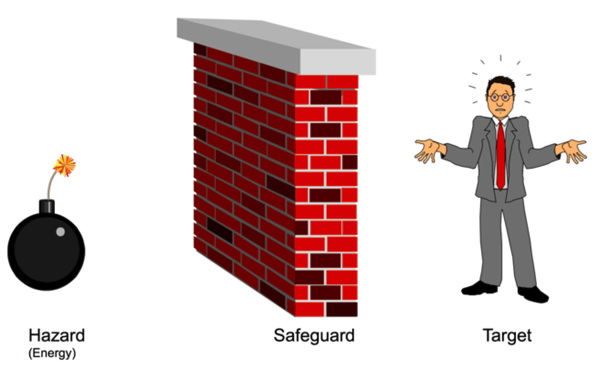
TapRooT® Users: You Are Way Ahead
TapRooT® Users use TapRooT® Root Cause Analysis to find the root causes of incidents, quality issues, hospital sentinel events, equipment failures, production issues, and cost overruns. They are WAY AHEAD of their competition, which is just asking “Why” five times. TapRooT® Users know how to stop repeat incidents by implementing best practices to develop corrective actions for the root causes of problems.
What do TapRooT® Users do? These four simple corrective action strategies (best practices).
1. Remove the Hazard and/or the Target
People who have attended TapRooT® Training know what a Hazard and a Target are (see the picture above). They realize that the most effective fix is eliminating the Hazard and/or the Target if possible.
Once a TapRooT® User gets rid of a Hazard or a Target, they may want to fix the root causes that were identified. However, if there is no Hazard/Target, they can be sure the accident won’t happen again.
2. Install a More Reliable Safeguard

Once again, people who have been to TapRooT® Training know what a Safeguard is.
To have an incident, all the Safeguards for that incident must have failed. Failed Safeguards are Causal Factors.
Strengthening Safeguards so they don’t fail is what root cause analysis is all about. But how much stronger can one make a weak Safeguard?
Instead of fixing a weak Safeguard, TapRooT® Users may decide to implement a stronger Safeguard.
An example would be to replace several weak human action Safeguards with a strong engineered Safeguard that would guard the Target. Or maybe an effective way to improve human performance with a good human factors design.
3. Fix the Root Causes of the Failed Safeguards
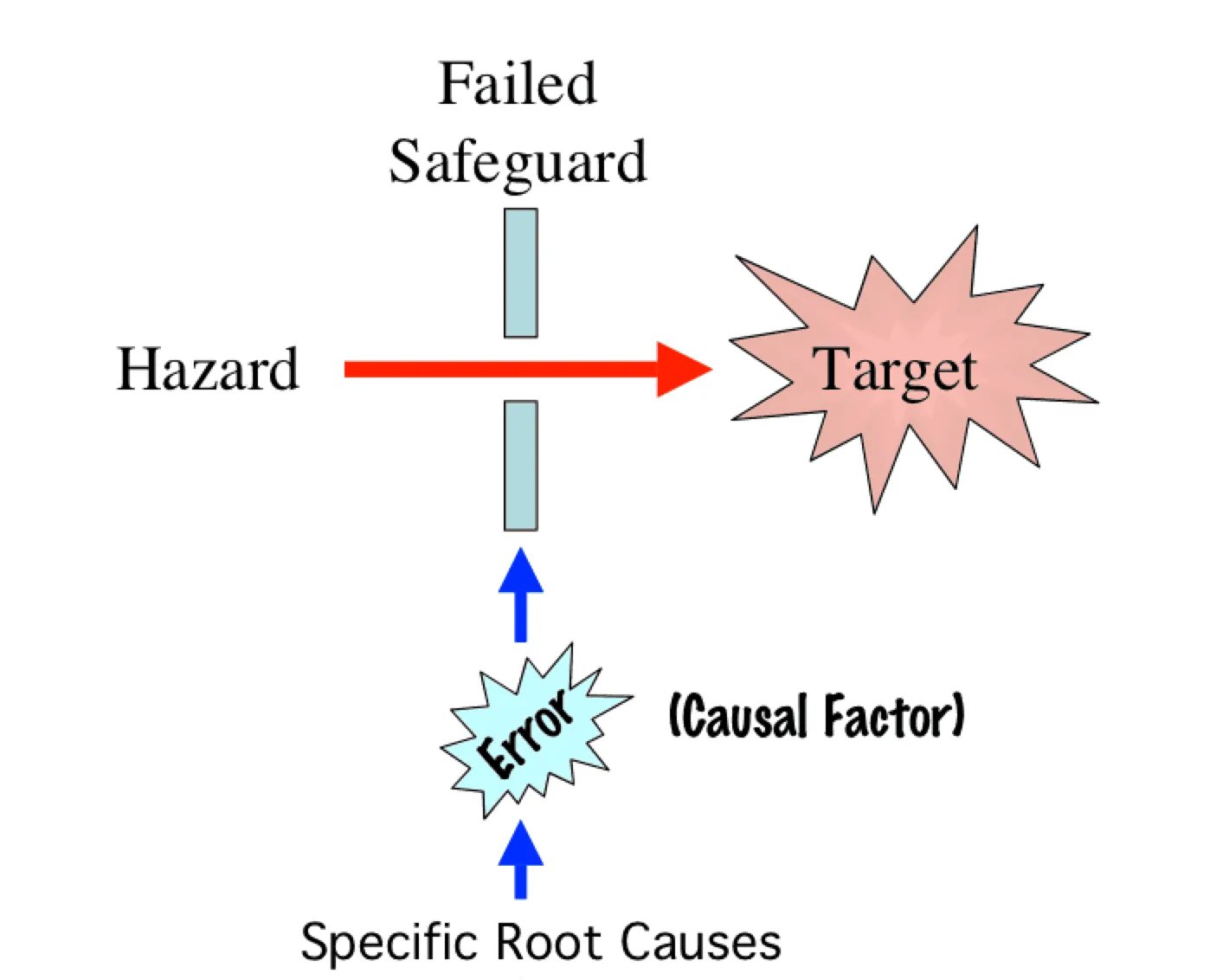
What corrective actions should you implement to fix a failed Safeguard? TapRooT® Users usually go beyond the standard three corrective actions:
- Training
- Discipline
- Procedures
Even though they know that is what people often recommend, TapRooT® Users have better ideas.
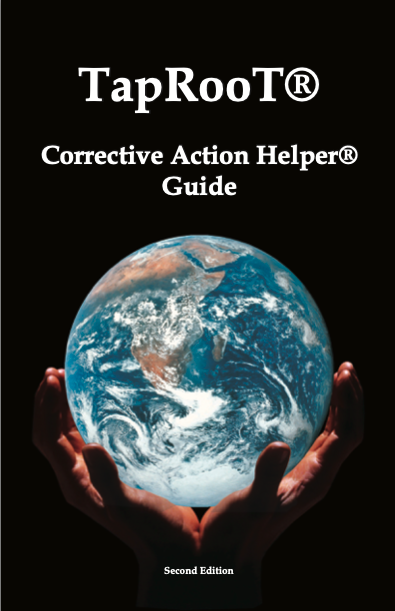
Where do TapRooT® Users get better ideas? The Corrective Action Helper® Guide/Software Module. The Corrective Action Helper® Guide helps investigators develop effective fixes for the root causes of the failed Safeguards. The Corrective Action Helper® Guide is a great way to get new ideas to fix problems that might have seemed difficult to fix.
4. Get Your Fixes Implemented
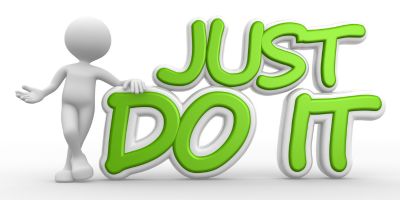
TapRooT® Users know better than to develop fixes, put them in a database (the backlog), and never implement them. TapRooT® Users make sure that corrective actions get implemented!
Companies that use TapRooT® RCA set due dates, track implementation, and do post-implementation effectiveness evaluations. All of this is a standard part of the TapRooT® System and Software.
Learn More About the TapRooT® Root Cause Analysis System/Software
What! You haven’t attended TapRooT® Training? Now is the time to register for one of our upcoming public TapRooT® Courses, held around the world. See the complete upcoming schedule HERE.
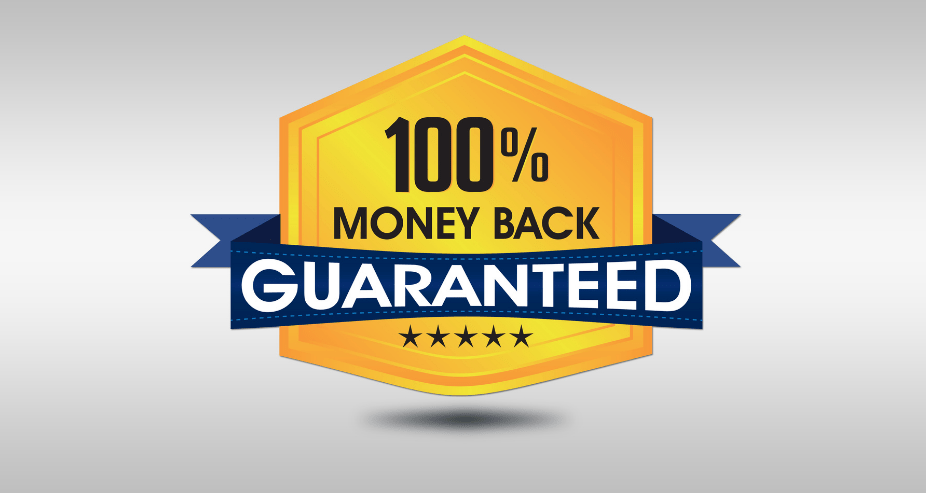
The training comes with this guarantee:
Attend a course. Go back to work and use what you have learned to analyze accidents, incidents, near-misses, equipment failures, operating issues, or quality problems. If you don’t find root causes that you previously would have overlooked and if you and your management don’t agree that the corrective actions that you recommend are much more effective, just return your course materials, and we will refund the entire course fee.
We know that you will go back to work with a valuable tool to help you discover true root causes and develop effective corrective actions.
