Designing an Improvement Program
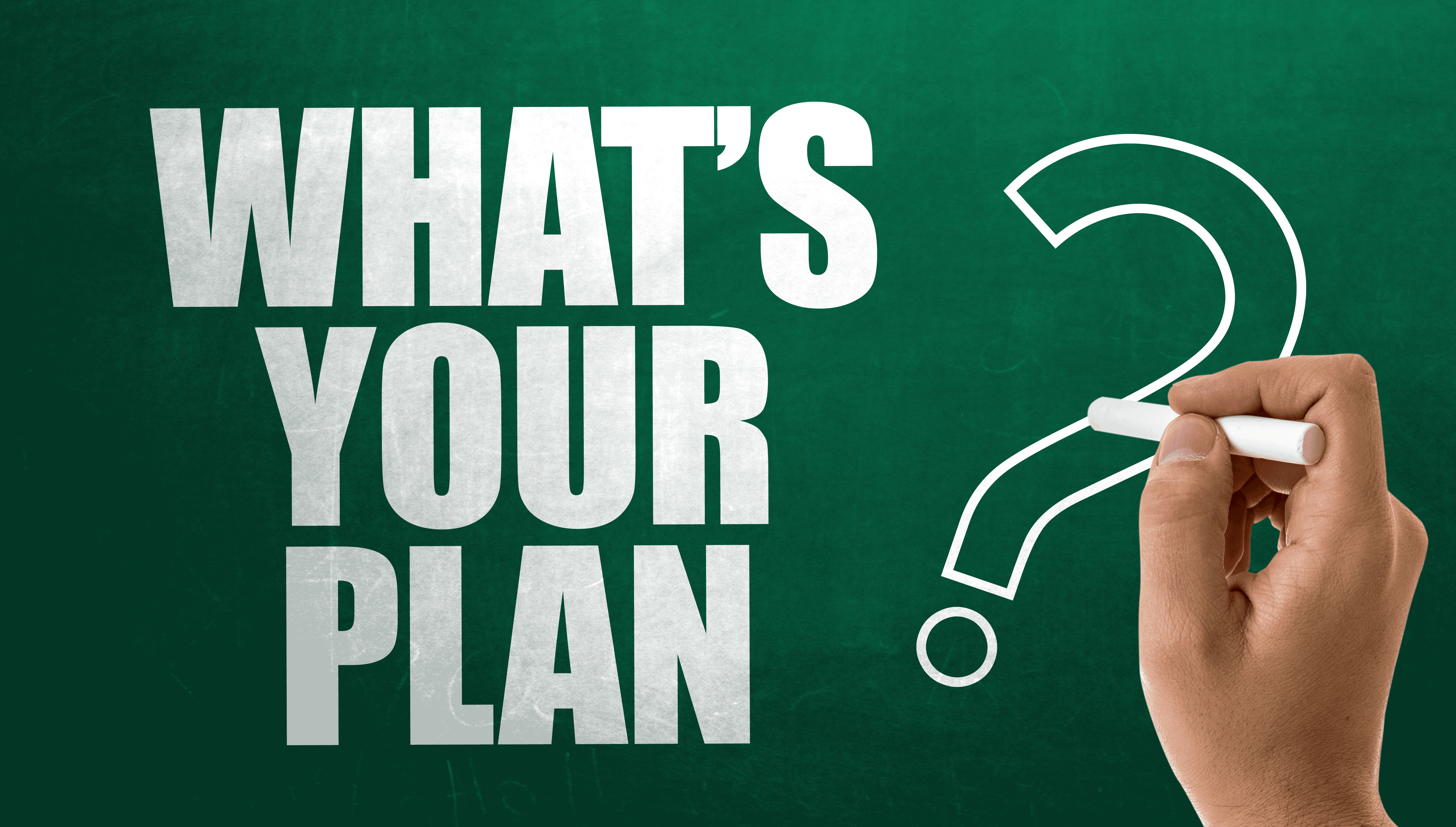
Did you know that 85% of improvement programs fail over time or revert to their initial state? Superior improvement programs are the 15% that have lasting, successful results. What makes them work? What do you need to know to develop an improvement plan? Read on to find out!
Seven Things You Need to Know to Design an Improvement Program
I’ve seen many people design programs to improve:
- Safety
- Equipment/Asset Reliability
- Patient Safety
- Quality
- Production Efficiency
- Process Safety
- Human Performance
- Project Effectiveness
These different types of improvement programs/plans had several things in common that people should understand BEFORE they start designing any improvement program/plan (or buy a one-size-fits-all plan from a consultant).
Unfortunately, I’ve seen people waste considerable time and effort implementing ineffective plans. Plans that seemed like a good idea but were missing key elements. Plans that failed or were lost when people just stopped using them. And a common problem was:
Those designing the plan didn’t know critical knowledge about making
performance improvement successful. They had no knowledge of one or
more of the key elements that would make an improvement plan succeed.
What are these common factors, knowledge, and key elements that people need to know? Here’s a short list:
- What are the essential elements of all improvement plans/programs?
- How can you understand human error and improve human performance?
- How can you troubleshoot equipment failures and improve equipment reliability?
- Knowledge from others that have developed similar plans/programs.
- Knowledge from other industries with other kinds of improvement plans/programs that can apply to your plan.
- How should senior management be involved?
- What measures should be tracked, and how should they be trended?
That’s a good start. Let’s look at each of these seven factors/elements in more detail below…
1. What are the Essential Elements of All Improvement Plans/Programs?
That’s an easy question to answer. See page 10 of Book 2:
Root Cause Analysis Implementation
You will find this checklist…

Pages 11-61 of Book 2 describe each of the 15 items above.

These items in the checklist guide development of any improvement program/plan. You can use this knowledge when you develop your Roadmap to Success.

Would you like to learn more about developing a Roadmap to Success? Call one of our TapRooT® Implementation Advisors at 865-539-2139 or text us HERE.

They will be happy to set up an executive briefing and develop a custom Roadmap to Success for your improvement program.
2. How Can You Understand Human Error and Improve Human Performance?
Almost every improvement program faces a challenge. To improve performance (safety, quality, equipment reliability, …), you must address the challenge of human error and develop ways to improve human performance.
There is no magic potion to make humans error-proof. But there are ways to significantly reduce (and sometimes eliminate) particular kinds of human errors.
You need to understand human performance improvement and include proven human performance improvement techniques in your plan.
Where can you learn about the techniques that work (and those that don’t)? At the 2-Day Stopping Human Error Course. See the upcoming course dates HERE.
This interactive course teaches the methods covered in the book Stopping Human Error.

Would you like to learn more about the book? CLICK HERE to read the book’s Foreword.
Another great place to learn about human performance best practices is at the 2023 Global TapRooT® Summit’s Improving Human Performance Track.
The Improving Human Performance Track shares best practices to reduce human errors by making processes more intuitive and less error-prone (more resilient). The track focuses on advanced human and organizational performance tools (HOP2) and uses advanced root cause analysis to improve the facilitation of learning teams. The track promotes networking and sharing best practices between attendees to develop a custom human performance improvement plan. The track is a perfect complement to the Stopping Human Error Course. Connect with the track leader, Alex Paradies, on LinkedIn to learn more about this track.
The track includes these sessions:
Session 1 – Digital Procedures: What Management Needs to Consider Before, During, & After Adoption | Dr. S. Camille Peres
Session 2 – Using TapRooT® to Improve Learning Teams | Alex Paradies
Session 3 – Advance HOP Techniques (HOP 2) | Alex Paradies & Kevin McManus
Session 4 – Sharing Human Performance Improvement Best Practices | Reb Brickey
Session 5 – The Effect of Fatigue and How You Can Detect It | Dr. Erin Evans-Flynn
Session 6 – How to Stop Non-Conservative Decisions | Alex Paradies
Session 7 – Building a Roadmap to Success | Rick Hulse
Session 8 – Using TapRooT® for Positive Outcomes | Tim Diggs
Session 9 – How Admiral Rickover Built the First High-Reliability Organization | Mark Paradies
3. How Can You Troubleshoot Equipment Failures and Improve Asset Reliability?
After solving your human error issues, you can concentrate on stopping equipment failures. How? By reactively and proactively applying Equifactor® Equipment Troubleshooting Techniques and applying equipment reliability improvement best practices.
To learn about Equifactor® Equipment Troubleshooting Techniques, read the book Using Equifactor® Troubleshooting Tools and TapRooT® Root Cause Analysis to Improve Equipment Reliability or attend the Equifactor® Equipment Troubleshooting & TapRooT® Root Cause Analysis Course (you get the book with the course).
Also, consider attending the Equipment Reliability Track at the 2023 Global TapRooT® Summit.
What is the Equipment Reliability Track all about? Ideas to help you improve equipment reliability and asset performance. Hear how Equifactor® Equipment Troubleshooting Users have reached new levels of equipment performance. Learn how to conduct cross-discipline troubleshooting and apply equipment troubleshooting best practices. And hear equipment reliability expert Heinz Block share his decades of experience achieving world-class equipment reliability.
4. Knowledge From Others That Have Developed Similar Plans/Programs.
Networking and benchmarking with others that have succeeded or are trying to improve performance in programs like the one you are developing can be priceless. But how do you meet these folks? EASY!

Meet these folks in the Creating a Superior Improvement Track at the 2023 TapRooT® Summit on April 24-28, which is being held near Houston, Texas.
If you agree with the saying:
“Progress cannot be generated
when you are satisfied with existing situations.”
– Taiichi Ohno.
Then you need to attend this track!
Whether you are evaluating the health of your current improvement program or just getting started developing your plan, the Creating a Superior Improvement Program Track is your opportunity to learn what you need to have a successful and sustained improvement program. This track will take you from setting goals and developing improvement measures to how to identify and investigate problems to hearing how the first high-reliability organization was built.
What topics are covered in the Creating a Superior Improvement Program Track?
Session 1 – Setting Goals & Developing Performance Measures | Jake Locklear
Session 2 – How Do You Get Senior Management Support? Best Practice Sharing | Amy Souders
Session 3 – Using TapRooT® to Improve Learning Teams | Alex Paradies
Session 4 – Sharing Investigations & RCA Best Practices | Tim Diggs
Session 5 – Best Practices for TapRooT® Implementation | Mark Paradies
Session 6 – TapRooT® Users’ Success Stories | Jason Dalen & Vincent Vincek, Facilitator – Ken Reed, (Panel Discussion)
Session 7 – Building a Roadmap to Success | Rick Hulse
Session 8 – How to Use TapRooT® for Minor and Major Accidents & Proactive Improvement | Marcus Miller
Session 9 – How Admiral Rickover Built the First High-Reliability Organization | Mark Paradies
These sessions provide ample opportunities to network and benchmark with other peers and experts in performance improvement.
If we settle for “good enough,” improvement will stop. Create a superior program that will bring sustained results. Connect with the track leader, Tim Diggs, on LinkedIn to learn more about the Creating a Superior Improvement Program Track.
5. Knowledge From Other Industries with Other Kinds of Improvement Plans/Programs That Can Apply to Your Plan.
The great thing about attending the Global TapRooT® Summit is the wide variety of participants from all sorts of industries from around the world. Thus, you learn more than the same old techniques that have been tried by people in your industry or in your profession. You learn from the success of other industries and professions.
What types of industries attend the Global TapRooT® Summit? This is a sample…
- Oil & Gas
- Construction
- Nuclear Plants
- Transportation
- Pharmaceuticals
- Hospitals/Healthcare
- Refineries and Chemical Plants
- Utilities
- Mining
- Pipelines
- Pulp & Paper
- Manufacturing
What professions are represented at the Summit? Here are a few…
- Safety
- Quality
- Training
- Equipment Reliability/Maintenance
- Senior Management
- Operations
- Engineering
- Nuclear Safety
- Process Safety
- Patient Safety
- Aviation Safety
- Risk Management
- Lean/Six Sigma
- Network Security
What countries have attended previous Summits? Here are the ones I remember off the top of my head (sorry if I left anyone out)…
- Canada
- Australia
- Tanzania
- Colombia
- Saudi Arabia
- Indonesia
- England
- Papua New Guinea
- Denmark
- Senegal
- Russia
- Mexico
- United Arab Emirates
- Germany
- Scotland
- Trinidad
- France
- Kenya
- Chile
- Portugal
- Norway
- Kazakhstan
- South Korea
- Switzerland
- New Zealand
- Singapore
- South Africa
- Belgium
- Brazil
- Nigeria
- The Netherlands
- Sweden
- Ecuador
- Egypt
- Ireland
- Thailand
- Finland
- Mozambique
- Bolivia
- Malaysia
- Peru
- Oman
- and of course, the USA
That’s a lot of cross-learning going on, and it’s a great way to get new ideas to make your improvement program even better!
6. How Should Senior Management be Involved?

Senior management involvement is essential for any serious improvement program across a company or across a site. How do you get your senior management involved? Here are two ideas…
- Have them attend our course about management involvement in root cause analysis and performance improvement. CLICK HERE for more information.
- Attend the best practice sharing session title: How Do You Get Senior Management Support? This session provides a great lesson learned sharing opportunity and is in the Creating a Superior Improvement Program Track at the 2023 Global TapRooT® Summit being held at the Margaritaville Lake Resort, Lake Conroe, near Houston, Texas, on April 24-28.
Those are two great ways to learn more about management involvement and to get your managers involved in supporting your improvement efforts.
7. What Measures Should be Tracked, and How Should They be Trended?
Measuring performance can be difficult. Most of the measures I’ve seen are reactive (not predictive/proactive). Many trends I’ve seen presented aren’t based on a sound mathematical footing.
You need good measures and trends to keep your improvement program on track. What should you do? There are three ways that I know that you can learn advanced methods for measurement and trending. Read about them below.
First is the book, Performance Measures and Trending for Safety, Quality, and Business Management.
The book explains how performance measures and trends can be used and misused. It provides examples of how trending is frequently misused and how you can spot the misuse of trends so that you won’t be fooled. It provides simple techniques that can be applied for quick improvement efforts. It explains and demonstrates more advanced techniques that can be easily understood and applied to spot trends in more complex data. And it explains how to use the same techniques to spot trends in often misunderstood, infrequently occurring data (for example, accident data).
Second is a new 2-day workshop being developed by Kevin McManus called 2-Day Measurement, Trending, and Predictive Analytics: How the Best Use Data to Improve Work.
Kevin McManus has over forty years of work experience as an Industrial Engineer, a Training Manager, a Production Manager, a Plant Manager, and a Director of Quality. That experience gives Kevin a ‘real-life work’ perspective relative to daily work process optimization, work team engagement and empowerment, and sustainable operational excellence.

Kevin has taught over 425 TapRooT® Courses and further enhanced his ability to help leaders proactively minimize risk, reduce errors, and improve reliability. Kevin holds an undergraduate degree in Industrial Engineering and an MBA. He served as a national Malcolm Baldrige Performance Excellence Award Examiner for twenty years, including a three-year term on the national Judge’s Panel. Kevin has authored the monthly performance improvement column for Industrial and Systems Engineer magazine for over 20 years, is an Institute of Industrial and Systems Engineering Fellow, and has been a member of IISE for over forty years.
In the 2-day workshop, you learn how to:
- Identify leading counts and ratios that best reflect the ‘vital signs’ of process performance
- Set up a simple process to capture and crunch daily process information
- Review and use measurement results daily to predict, anticipate, and improve performance
- Recognize and engage team members in effective daily measure use
- Select options to improve the design of your existing measurement work system
Learn more about the workshop HERE.
Third, there is a session at the 2023 Global TapRoot® Summit titled, Setting Goals & Developing Performance Measures, presented by Jake Locklear. You can hear his performance measure best practices and network with others interested in the topic.
That’s great information about measures and trends to improve your improvement program.
That’s a Great Start! (But a lot of work.)
You might think that getting all that knowledge, networking with all those people, reading those books, and attending all those courses is a lot of work. You are right!
It is easy to fail but hard to succeed!
You want to be among the 15% that succeed rather than the 85% that fail.
You might ask:
Why didn’t Mark just tell us everything we needed to know in this article?
Why do I have to get books, attend courses, and attend the Summit?
The answer is simple. I can’t put several books, several courses, and the knowledge of many experts in an article. Instead, I told you where you could find the knowledge. Now it’s up to you to follow through:
- To sign-up for the classes.
- To register for the Summit.
- To read the books.
Then, you will have a headstart making your improvement program world-class.
You might also think that developing this program requires more than one person. And it would be easier if you had an improvement team, and each member could work on several aspects of developing a successful improvement program. If this is true for your program, you need to identify the right people to help you make this happen.
But get started NOW! You can’t afford a second-class improvement effort that wastes time and energy because those designing it didn’t know the best practices they needed.
And once you get started, you will learn that excellence is a continuous process. That once you start, you will need to keep pushing, keep learning, and keep improving to keep your program world-class. There is no resting on your laurels.
You will also learn that the effort it takes is worth it. Once you apply the knowledge and best practices, the improvement will be much easier than the effort required for unsuccessful programs. After all, learning from the success of others is much easier than learning from failure.
