Discover Root Causes
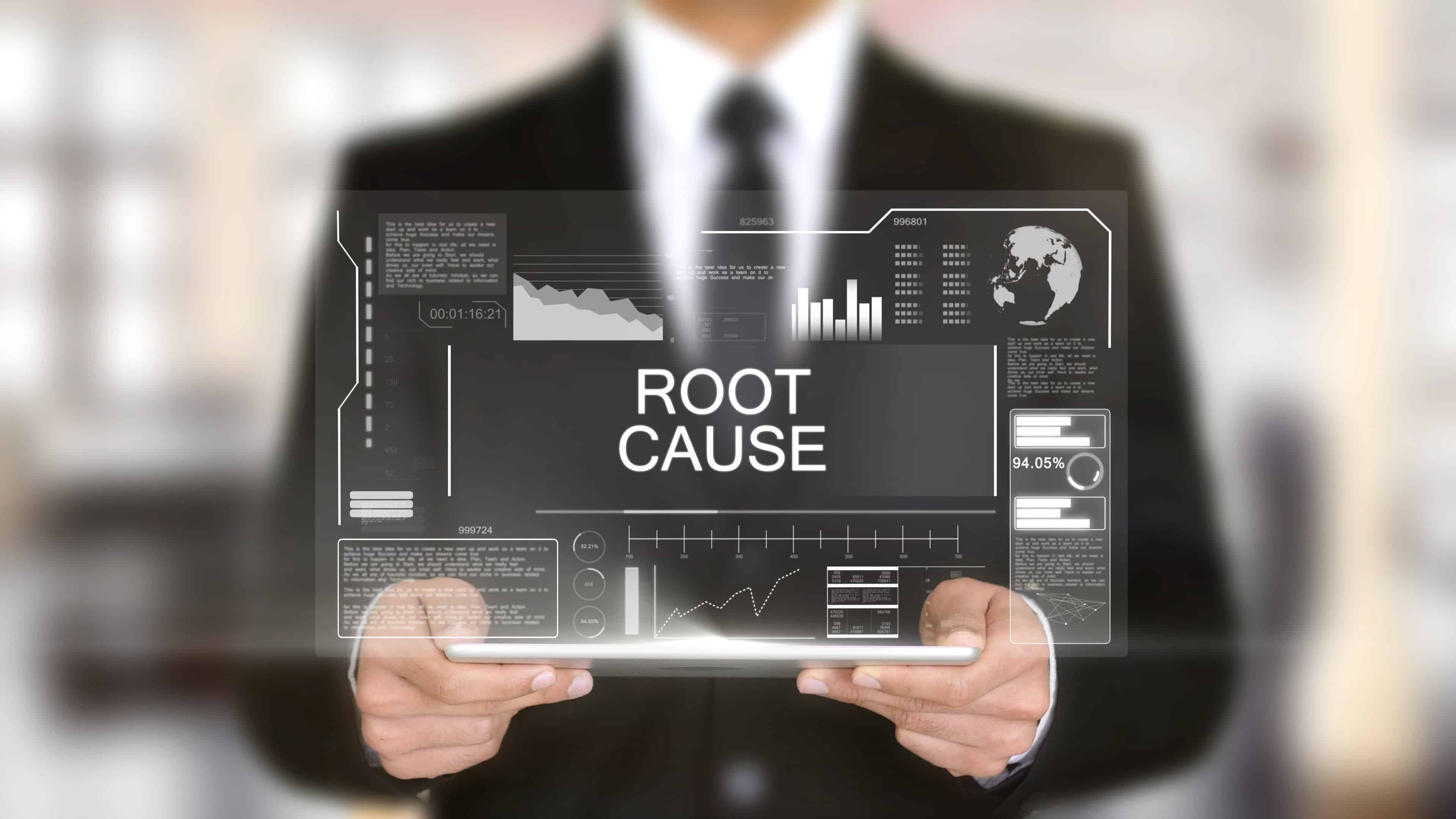
What is Missing from Most Root Cause Tools?
I was talking with a TapRooT® RCA User, and they pointed out something I had not considered. They said the biggest problem with most root cause tools (5-Whys, Why Trees, Fishbone Diagrams, Cause-and-Effect, etc.) was that they only reflect the investigator’s knowledge. If the investigator doesn’t already understand the cause of an incident, they won’t discover root causes that they don’t currently understand.
He said they chose TapRooT® as their corporate standard because they found that it led their investigators to root causes that they previously would not have identified. It helped the investigators go beyond their current knowledge. Thus, investigators could find and fix root causes that they previously would have overlooked. This was especially important for the root causes of human performance issues.
How Does TapRooT® RCA Help Investigators Discover Root Causes?
How does TapRooT® RCA lead investigators beyond their current knowledge to discover root causes that they previously didn’t understand? There are at least two tools in the TapRooT® System that are critical for discovering root causes:
- SnapCharT® Diagram
- Root Cause Tree® Diagram
Let’s quickly review how each of these helps in the sections below.
SnapCharT® Diagram
The SnapCharT® Diagram helps investigators understand what happened and the multiple causal factors that led to an incident. Here is a simple SnapCharT® Diagram from the start of a simple investigation…
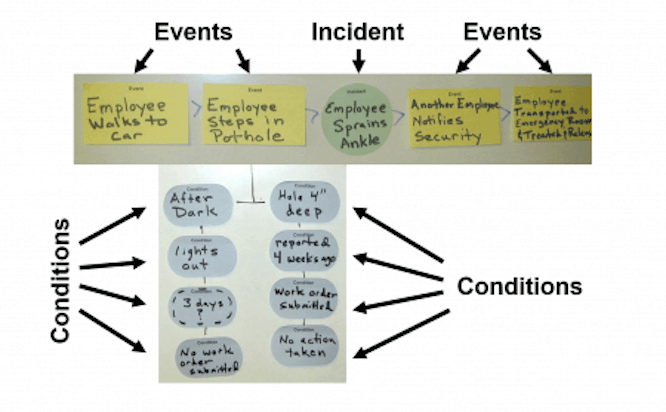
This basic information needed to understand an incident’s root causes can be overlooked when jumping to “the cause” in systems like 5-Whys and Cause-and-Effect.
In an investigation, the investigator adds information to the SnapCharT® Diagram as they expand their knowledge of what happened and how it happened. For example, understanding the simple incident above could grow until the SnapCharT® Diagram looked like the figure below…
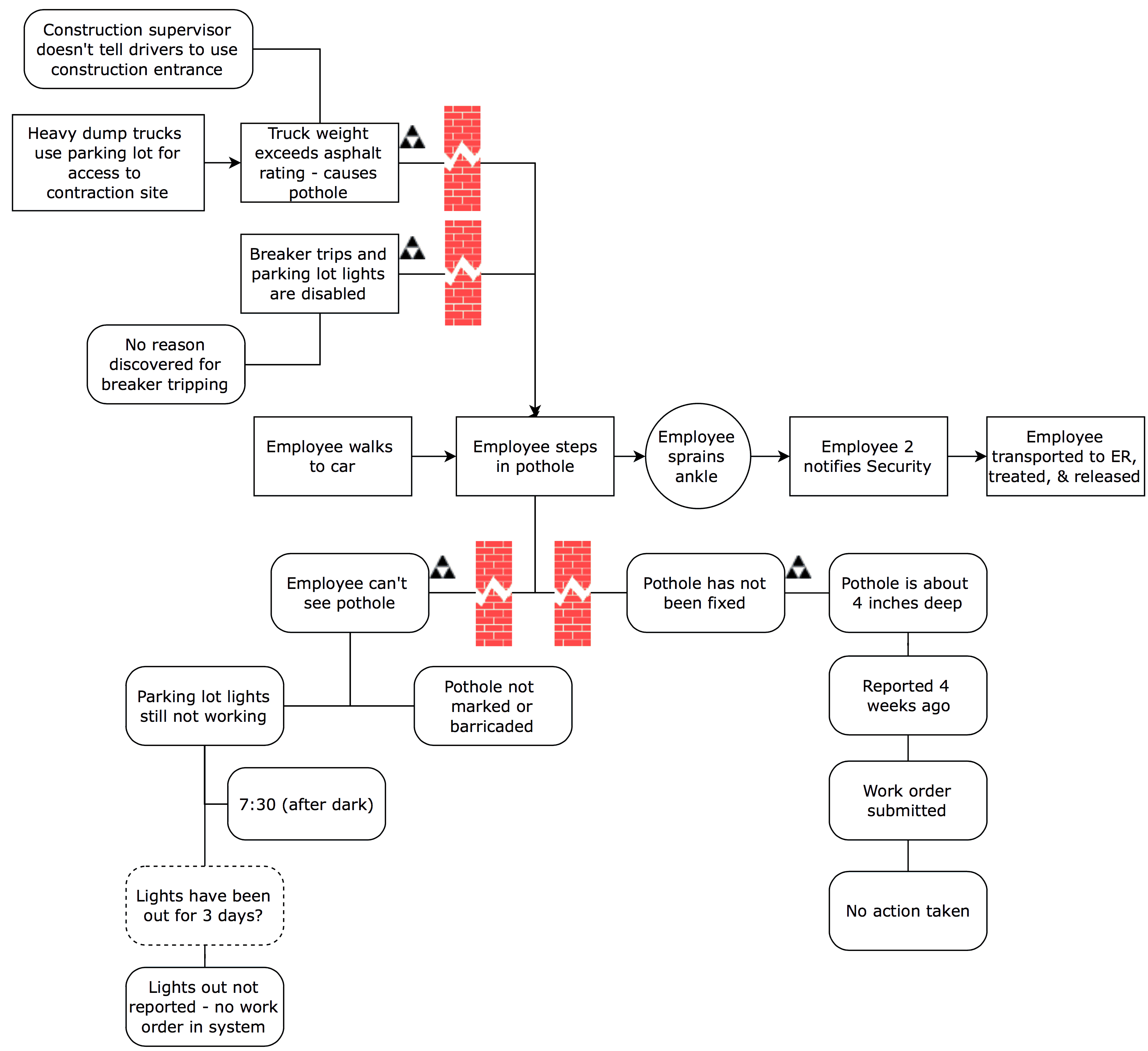
Thus, the investigator’s understanding of the incident is expanded, which helps the investigator understand causes beyond blame for simple incidents. Thus, the investigator may look for causes of causal factors (for example, why weren’t the parking lot lights fixed) that they previously might have failed to identify.
Root Cause Tree® Diagram
The Root Cause Tree® Diagram is probably the “secret sauce” that helps investigators the most when looking for root causes outside the investigator’s experience.
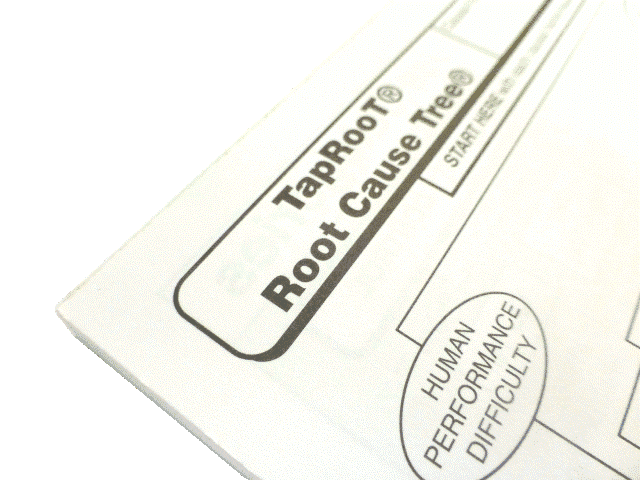
The Root Cause Tree® Diagram uses a tree format and a set of questions (including the Human Performance Troubleshooting Guide – 15 Questions) to lead an investigator to ask questions and collect information that leads investigators to find new causes that they previously would not have considered. For more information about how the Root Cause Tree® works, please read the white paper at THIS LINK.
Putting It All Together to Discover Root Causes
The TapRooT® System integrates these tools (SnapCharT® and Root Cause Tree®) into a process that can be efficiently used for simple incidents or complex investigations. It also includes other important tools for collecting information and developing effective corrective actions.
The process for simple incidents concentrates on the SnapCharT® Diagram and the Root Cause Tree® Diagram…
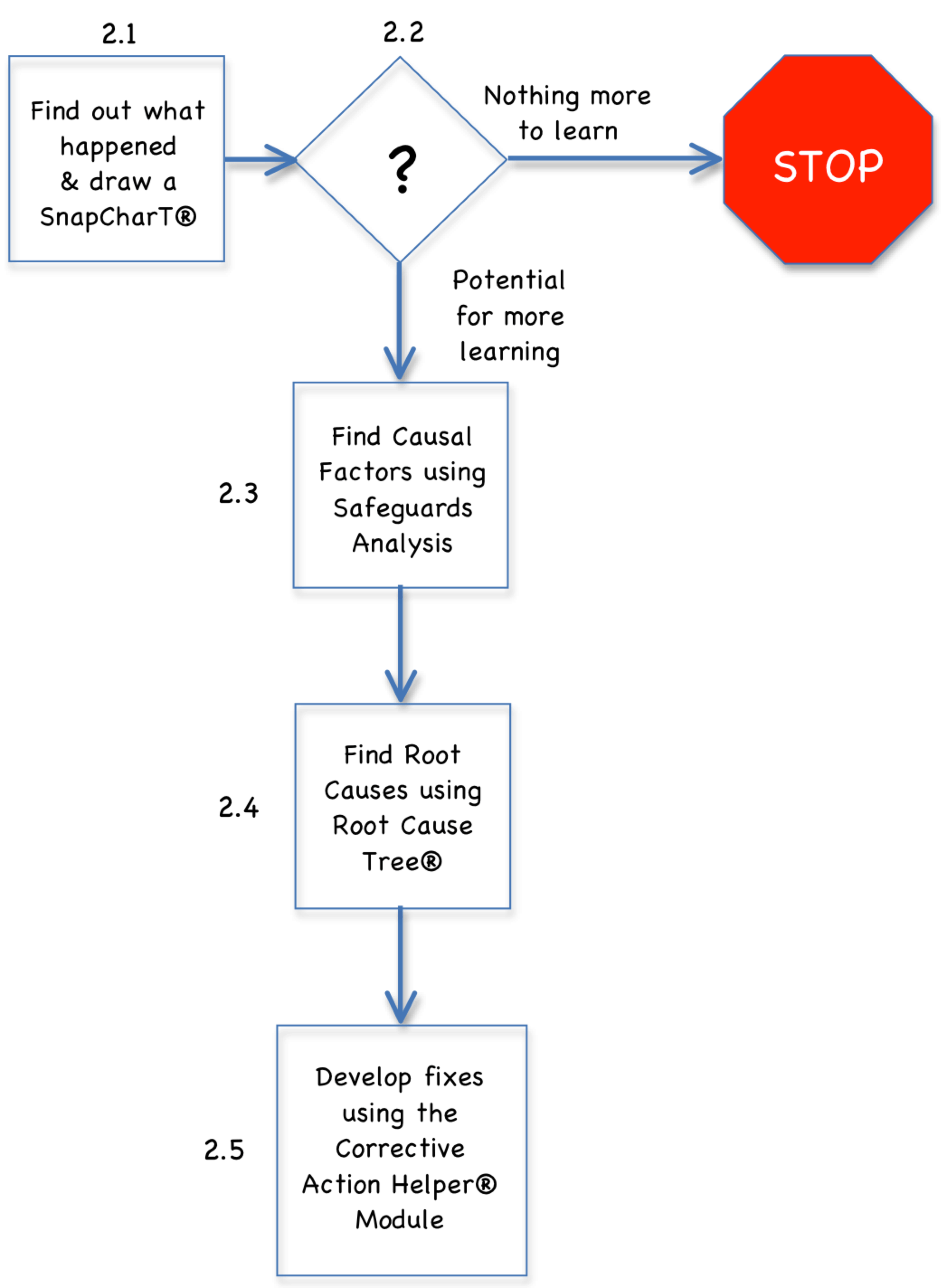
The process for complex investigations includes the SnapCharT® Diagram and the Root Cause Tree® Diagram as its base, but it also includes the optional tools shown below.
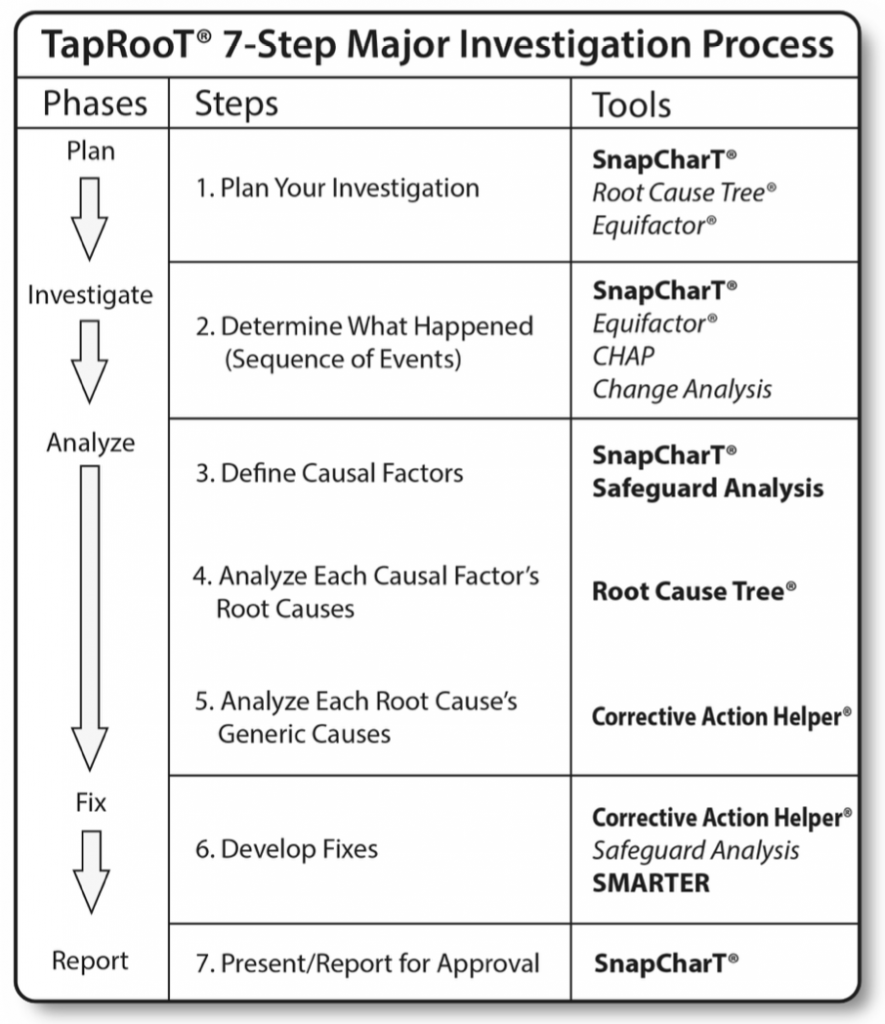
How can your people learn to use these tools to discover root causes that they are currently overlooking?
Training to Discover Root Causes
Have your people attend one of our public TapRooT® Courses (see the upcoming courses, dates, and locations HERE), or get a quote for training at your site by clicking HERE. If you would like to see the complete course outlines, click on the course you want to review HERE.
Don’t worry. Feel confident scheduling this training because it comes with a guarantee:
COURSE GUARANTEE
Attend one of our courses. Go back to work, and use what you have learned to analyze accidents, incidents, near-misses, equipment failures, operating issues, or quality problems. If you don’t find root causes that you previously would have overlooked and if you and your management don’t agree that the corrective actions that you recommend are much more effective, just return your course materials, and we will refund the entire course fee.
We can offer this guarantee because we are certain you will see the value of what you learn to discover root causes.
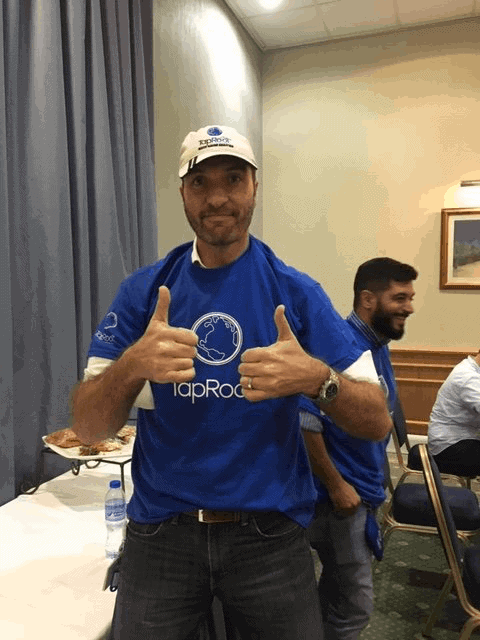