Does Your Company’s Support of HSE Go Up & Down with the Price of Oil?
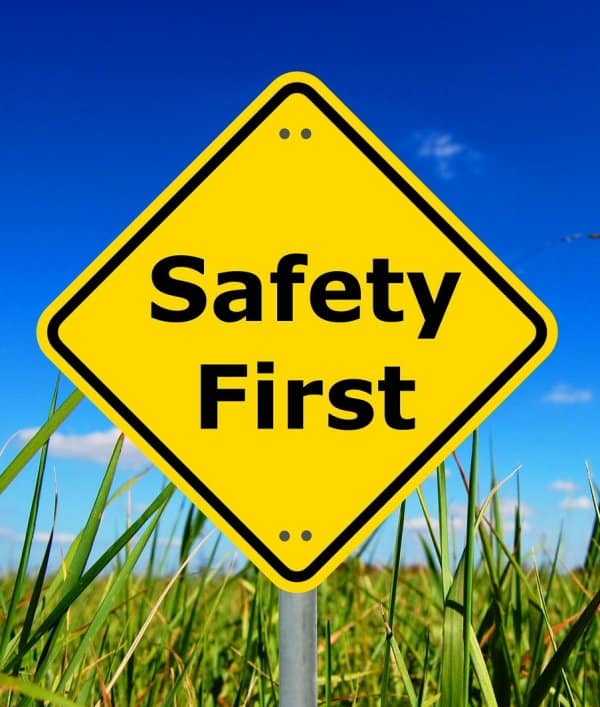
DOES YOUR COMPANY’S SUPPORT OF HSE GO UP & DOWN WITH THE PRICE OF OIL?
I know the question above may be a difficult one, but it is a serious question. People often say … SAFETY FIRST … but do they mean it?
Many years ago I knew of an offshore oil production platform fire that was at least partially caused by cost cutting. One of the engineers we interviewed said that if the price of oil was high, they “gold plated” platforms with many redundant safety features. But if the price of oil was low, they cut features to the bone – often using cheap, off-the-shelf packages that were put together on the fly to keep costs low.
When the VP of the division was presented the facts of the incident, and could see the role that cost-cutting had played, he said:
“If anyone would have told me about the impact of the cuts,
we wouldn’t have made them!”
This may have been a serious comment … but executives SHOULD KNOW the impact of their decisions.
For example, if staff cuts are made, what work isn’t going to be accomplished?
The hope is that everything will be done by fewer people. The reality is that shortcuts will be taken by people low down in the organization. They will prioritize what gets done and what gets left undone. Often, production issues take priority and long-term safety issues get put on the back burner (the backlog). People rationalize these economy moves – especially if nothing bad happens right away.
This happened with budget cuts (that resulted in reduced training and increased operations tempo) in the US Navy. This partially caused two fatal collisions in the Pacific Fleet.
In the Navy example, “We support our troops!” (a saying similar to “Safety First!”) did not mean sailors (including junior officers) received the training and equipment they needed to avoid collisions at sea.
For an industrial example, let’s look at how cuts in the oil industry might impact safety.
When budget cuts are made, production equipment maintenance will happen because, if it doesn’t, the lack of production will get immediate attention. But safety equipment preventative maintenance can be added to the backlog and there are no immediate consequences until … an emergency occurs and the equipment fails. This could lead to fatalities.
Of course, management would say,
“We never intended for safety related
maintenance to be backlogged.”
But did management measure safety system maintenance backlog and keep themselves informed?
Here is another safety question …
Does your attendance at the TapRooT® Summit
depend on the price of oil?
What if management said that people can’t attend the Summit due to budget cuts? Would it hurt anything? Many Summit participants learn valuable best practices that help them save lives. These lives could be lost in a major accident IF the accident isn’t prevented by the application of these best practices.
People say …
“But Mark, there are real cost pressures …
something has to give …“
Let me ask your VP. Would he or she say …
“IF ONLY SOMEONE WOULD HAVE TOLD ME?“
Here are some of the life saving best practices that you WILL NOT be learning if you don’t attend the 2019 Global TapRooT® Summit…
- Best practices from other TapRooT® Users shared in the “TapRooT® Users Share Best Practices Session”
- Ten adverse conditions that commonly exist before accidents happen (from Astronaut Jim Wetherbee)
- How to fix a human error (by Mark Paradies)
- What does it take to be a high reliability organization (by Mark Paradies)
- How to effectively enforce the rules (by Kevin McManus)
- How to be proactive using TapRooT® (two sessions, one by Marcelo Marquez and one by Scott Waddle)
- Selling improvement ideas to management (by Rick Hulse)
- How best of class companies include all job functions in root cause analysis (by Heinz Bloch)
- Decisions that get people killed – and how you can stop them (by Mark Paradies)
And that’s just a sample. To see the complete 2019 Global TapRooT® Summit schedule CLICK HERE.
Certain essential HSE functions must be maintained to keep your company free of major accidents. Continuous improvement of your safety, risk, incident investigation, and improvement functions should be part of those critical functions that ARE NOT CUT. Attending the Global TapRooT® Summit should be part of your plan to continuously improve your safety, risk, incident investigation, and continuous improvement functions (and, thus, should not be cut).
When is the Summit? March 13-15 (with advanced pre-Summit Courses on March 11-12).
Where is the Summit being held? Houston (Montgomery), Texas, at the La Torretta Lake Resort & Spa.
What is the registration fee? Here is the base price and the discounts for attending a course and the Summit or for multiple attendees…
Sign up now and get in on the Early Bird Special...
Register for the Summit by CLICKING HERE.
The consequences of cuts to safety improvement initiatives are real.
Don’t miss out and wish you had learned the knowledge you needed to prevent the next major accident.