Troubleshooting Electrical Equipment
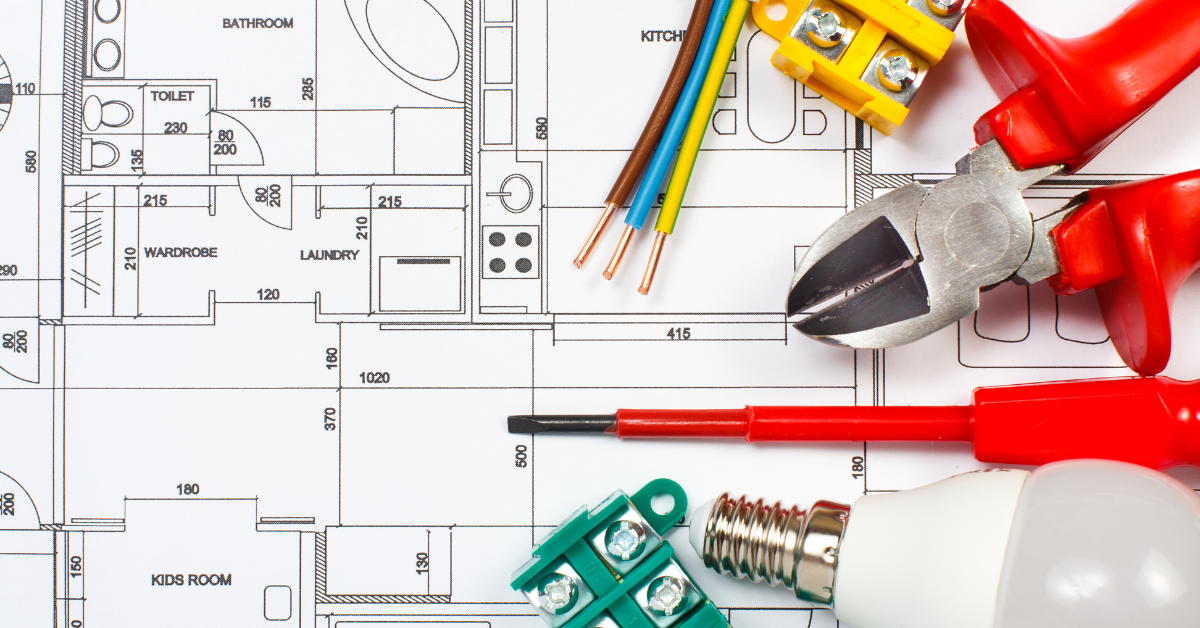
There’s only so much that CAN go wrong with electrical equipment.
I read a book last week from 1972: How to Repair Electrical Appliances by Gershon Wheeler. Older books are the best because there’s no timidity or “it has been suggested,” or “we don’t know exactly but . . .”.
“Here’s how it works and why” is all there is . . .
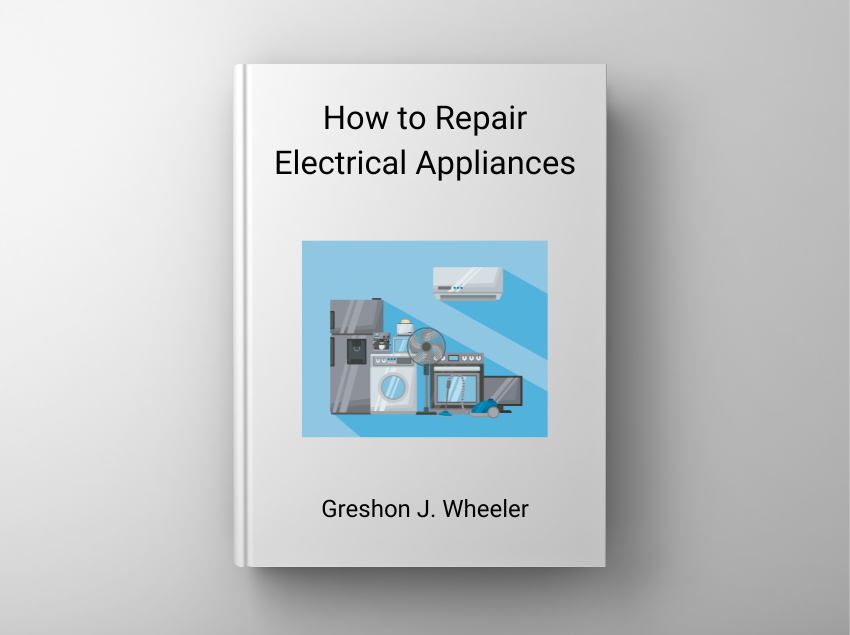
Rewiring and greasing blenders and finding why you have to run multiple dryer cycles to dry your clothes are some great skills I added to my tool belt, but there’s one key concept he kept presenting:
“There are only so many ways an electrical system can fail.“
I’ve led divisions of electrical and electronics technicians, and I found this embarrassingly recentering. Every effect has a definite cause, and lists of possible causes for a given symptom are short. With access to experience and knowledge, we can turn an infuriating brainstorming guessing game into a simple process of elimination. I and my guys spent way too many hours troubleshooting just because we didn’t stop long enough to bound the problem.
Form a troubleshooting plan based on the symptoms, collect evidence to eliminate possible causes that don’t apply, and you are left with a set of ≥ 1 causes you need to correct. Fix these problems everywhere they exist, and you’re on your way to perfect reliability.
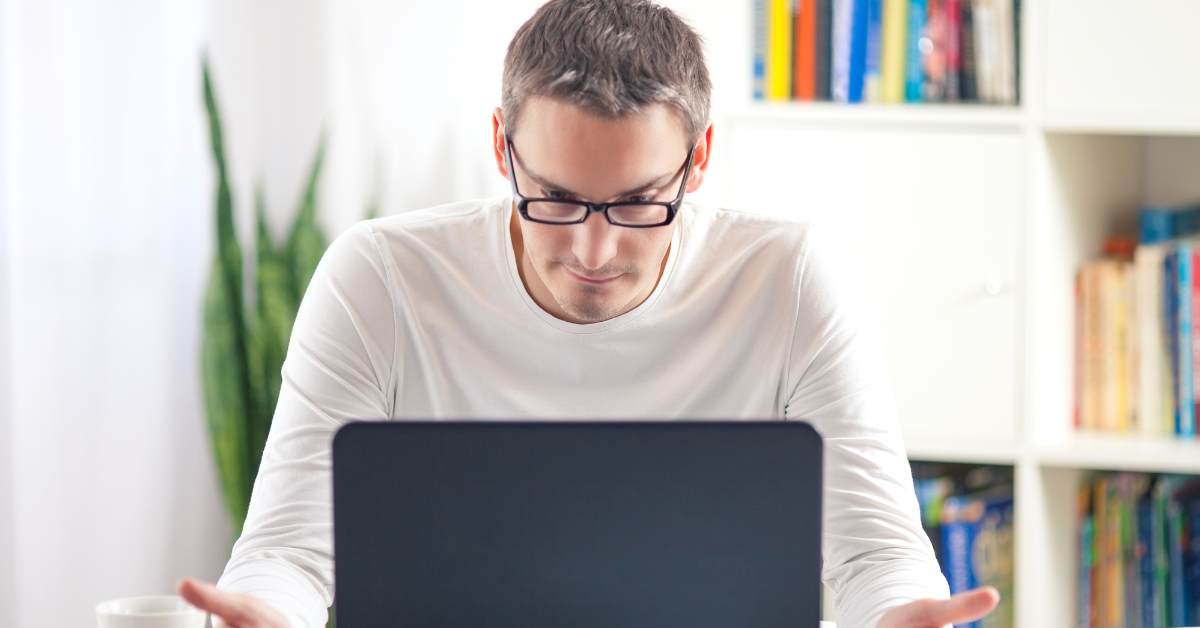
Equifactor® Troubleshooting Tables list all the ways equipment can fail.
This is the signature strength of the Equifactor® troubleshooting tables. Engineers, equipment operators, technicians, and designers have spent collective man-millennia understanding equipment and why it fails. The answer to why your equipment broke is absolutely out there. How accessible is it though?
Equifactor® gathers all of this information on symptoms and possible causes into a set of easy-to-use tables. World-class maintenance and troubleshooting expert experience (think Heinz Bloch) is the source. At its core, Equifactor® is built on the idea that there are a finite and usually small number of symptoms and possible causes. Equipment troubleshooting and Root Cause Analysis do NOT require a degree or experience. You just need a way to access that collected expert knowledge and experience so that you can ask the right questions. That’s what Equifactor® and TapRooT® are all about!
For much more in-depth equipment troubleshooting, sign up for an upcoming Equifactor® course. Until the game day, keep reading Equifactor® and equipment articles on taproot.com/blog.