Is Fatigue an Issue for Your Workers? (How far away is death?)
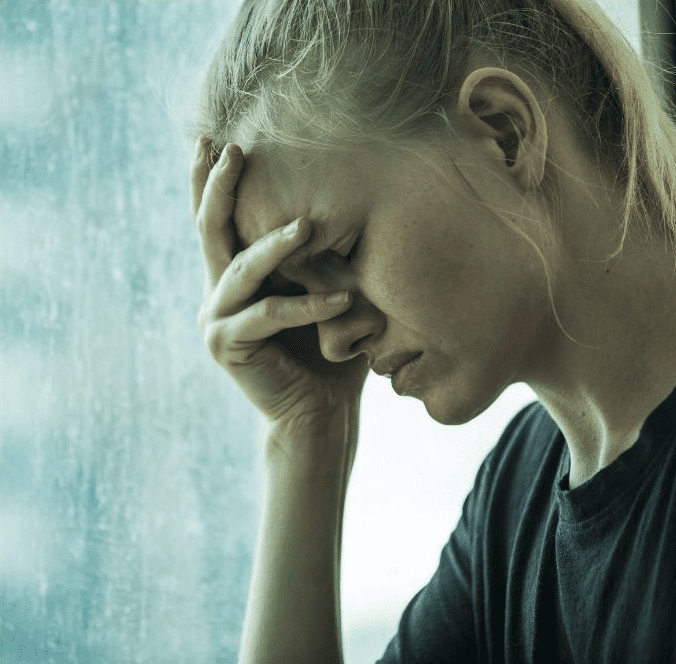
Failure to Recognize Fatigue-Related Accidents
Here is an example of a fatigued driver from actual car crash research…
I was reviewing an industry study on the causes of accidents and noticed that fatigue was nowhere on their list. Since other studies where people actually observed performance (like the study in the video above) show that fatigue is a major issue in real-world accidents, I wondered why fatigue or fatigue-related causes did not appear on the industry-sponsored list.
The easy answer is … If you don’t ASK about fatigue and look into fatigue as a potential cause, you will never find it.
Actual Investigation Didn’t Ask About Fatigue
That reminded me of an investigation into a barge crash. The investigator couldn’t find a reason why the First Mate had gone “brain dead” and made a totally inappropriate approach to a bend in the river. The first mate was experienced and knew how to line up for this turn. It was very important to be lined up correctly because the river was running near flood stage, and there was little room for error. But once he was lined up wrong, he had little choice. He tried to “power through” the turn and crashed the barges into a bridge after the turn.
One of the questions I asked the investigator was, “Did you consider fatigue?” (The accident happened at about 5 AM and the tug and barges were on the second day of the trip.)
The reply was interesting … the investigator said:
“He was working a standard schedule.”
That seemed to be enough for him to dismiss fatigue as a cause.
I asked,
“What is a standard schedule.”
The answer,
“6 on and 6 off.”
So the First Mate would normally work from midnight to 6 AM, have six hours “off” to rest or work, then be back piloting from noon to 6 PM, get off, eat dinner, and go to bed and get back up to work from midnight to 6 AM again.
I asked if he knew the First Mate’s sleep schedule before starting the journey. The answer?
“No, I didn’t ask about that.”
Even after this questioning, the investigator just couldn’t see that fatigue could be a potential cause that should be looked into. After all, the schedule was a standard industry practice.
How Does TapRooT® RCA Help Investigators Recognize Fatigue?
How Does TapRooT® RCA Help Investigators Recognize Fatigue? That’s an easy question to answer. The first question in the Human Performace Troubleshooting Guide on the Root Cause Tree® Diagram is…

The Root Cause Tree® Dictionary then has questions to help the investigator answer this question, including questions about:
- the supervisor’s ability to detect the fatigue level of the worker,
- the shift scheduling,
- sleep disorders,
- violations of state or federal laws requiring rest/sleep periods,
- working more than 16 hours in a row, and
- the design of the job that requires excessive monitoring that leads to a vigilance decrement for normal workers.
If the investigator answers yes to:
“Was a person excessively fatigued, impaired,
upset, distracted, or overwhelmed?”
Then they have potential causes to investigate by answering the questions in the Human Engineering and Work Direction Basic Cause Categories. This helps the investigator identify causes like:
- vigilance decrement,
- excessive work hours,
- shift/work scheduling, and
- company policies.
That’s certainly some good guidance for investigating potential causes of fatigue.
What Do You Do to Investigate Fatigue?
Does your investigation system include standard questions about fatigue? Or does it leave your investigators like the barge accident investigator who never thought about fatigue as a cause?
Next, would the person who had an accident admit that they were fatigued (or worse yet, asleep)? Many accidents are caused by fatigue, but the fatigued individual doesn’t even realize that was the cause. For instance, in the barge accident above, the investigator can’t understand why the First Mate was “brain dead.”
Sometimes people invent excuses to hide the fact they were fatigued or asleep. Watch this video for an example…
That’s a good reason to install cameras to look for fatigue as a potential cause. These cameras and other monitoring devices can be used proactively to spot fatigue on the job and implement fixes before accidents happen.
Learn More About Advanced Root Cause Analysis
TapRooT® Root Cause Analysis is advanced root cause analysis. It covers all the fundamentals of root cause analysis and guides investigators to the fixable causes of accidents and precursor incidents.
Why do we suggest guided root cause analysis? Watch Mark and Benna discuss that topic here…
How can you learn more about TapRooT® RCA? We have several courses to choose from:
- 2-Day TapRooT® Root Cause Analysis Training
- 3-Day Virtual TapRooT® Root Cause Analysis Training
- 1-Day Equifactor® Troubleshooting Training
- 5-Day TapRooT® Advanced Root Cause Analysis Team Leader Training
To have one of these courses at your site, call us at 865-539-2139 OR CLICK HERE to e-mail a request for a course quote.
Or, if you would like to sample a course BEFORE you have one at your site, attend one of our public TapRooT® Courses held worldwide. Here is a LINK to our upcoming course schedule.
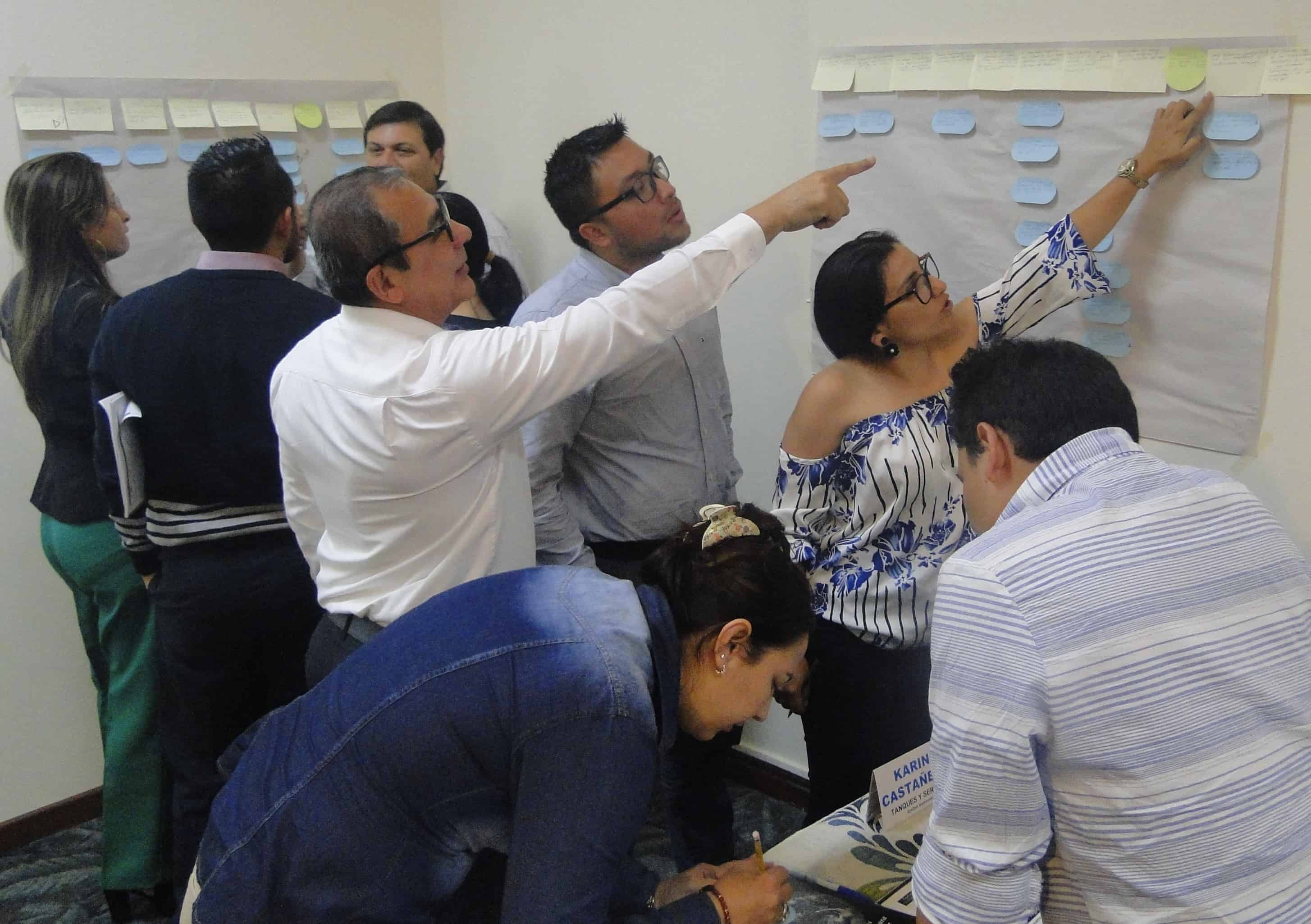
But don’t wait! The TapRooT® Root Cause Analysis System guides you to many more potential causes than just fatigue. Attend one of our guaranteed courses and learn how TapRooT® RCA can help you find and fix root causes that you previously would have overlooked.