Food and Beverage Industry – Recall and Root Cause Analysis?
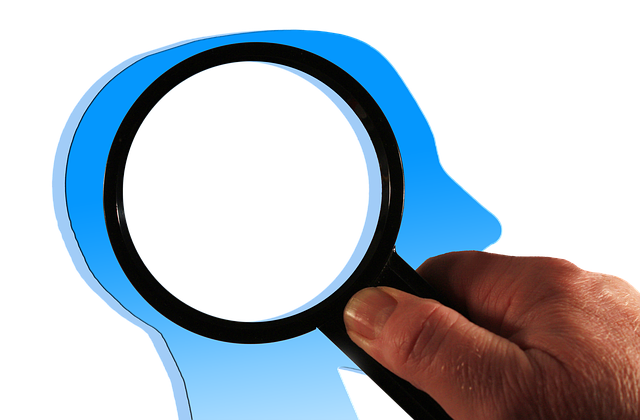
Over the past several weeks, there have been several nationwide recalls, including one for Jif Peanut Butter Recall.
This recall is a great example of when a world-class root cause analysis system can be used to prevent major disruptions to production chain. I think we can all imagine the cost in rejected goods, cleaning of equipment, and even the reputation of the company.
Using a solid root cause analysis system like TapRooT® RCA would allow a company to quickly find not just the physical cause of the contamination, but also the human performance issues that led to the contamination. TapRooT® Root Cause Analysis Training is a proven system engineered to find real root causes and fix problems.
For example (hypothetically), if a steam kettle was not properly sterilized, it isn’t good enough to just note that the steam kettle was improperly sterilized, or even that, “worker improperly sterilized the steam kettle.” We REALLY need to dig into the reasons that the improper actions were taken. For example, maybe we would find:
- Technician used the wrong sterilization method
- It was difficult to reach all areas of the steam kettle
- A new version of the steam kettle was supposed to be used, but it was not known to the staff
- The cleaning procedure did not address secondary contamination
All of these issues could be reasons why our technician made the mistake. This is not about assigning blame but, rather, understanding the possible human performance issues that led to the contamination. Without knowing these issues, it is likely we’ll see a repeat of this mistake in the future.
TapRooT® can help you address these kinds of problems and many more types.
Don’t settle for just blaming the employees; dig deep enough to understand the reasons mistakes are made.
TapRooT® is global to meet your needs. Please see our full selection of courses.
If you would like for us to teach a course at your workplace, please reach out to discuss what we can do for you, or call us at 865.539.2139.
Stay engaged with your skills and training: Follow along on our blog; listen to our Wednesday TapRooT® TV video sessions at noon EST; connect with us on Facebook, Twitter, Instagram, Pinterest, and LinkedIn, and YouTube.
Source for featured image: Image by Gerd Altmann from Pixabay.