Goal: Safe, Reliable, Efficient Operations
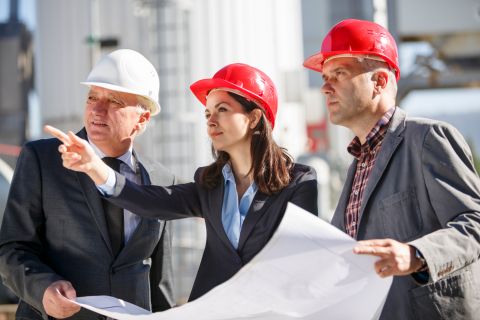
How To Achieve Safe, Reliable, Efficient Operations
If your goal is to achieve safe, reliable, efficient operations at your facility, you need to read this.
Why? Because we will outline an essential path to meet your goal.
Let’s start with this idea:
To achieve safe, reliable, and efficient operations,
you need superior root cause analysis.
Read on for an explanation of why this is true.
What is Root Cause Analysis?

Root cause analysis is the examination problems to discover basic causes that, when corrected, will improve performance by preventing or significantly reducing the likelihood or consequences of a repeat problem.
Root cause analysis can analyze accidents, precursor incidents, quality issues, or equipment failures. It can also be used proactively to find and fix the potential causes of problems before an accident, quality issue, or equipment failure occurs.
Root cause analysis is a recognized industry good practice and is required by law by several federal/state/industry regulations, including those issued by the FDA, FAA, EPA, OSHA, NRC, DOE, DOT, MSHA, BOEMRE, FRA, and the Joint Commission.
When Should You Use Root Cause Analysis?
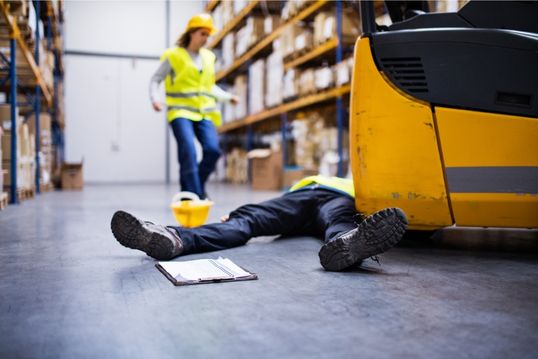
Not every problem is worth a root cause analysis. Every investment should produce a positive return on investment. Root cause analysis requires investigators’ and management’s time. Then, there are corrective actions to implement.
So, before you start an investigation, you should see that the outcome (preventing future incidents/accidents/equipment failures/quality issues) is worth the investment.
Of course, major accidents (like fatalities, explosions and fires, major environmental releases, serious injuries, and expensive losses) will be investigated. We don’t want these major accidents to repeat. But what about more minor incidents and near-misses?
We call these minor incidents worth investigating “precursor incidents.” Even though the incident might not have had serious consequences, the causal factors and root causes could cause a more serious, expensive future incident. Thus, correcting these problems could prevent a more serious accident in the future. That makes the investigation and correction of these problems worthwhile.
To read more about precursor incidents, CLICK HERE.
In the TapRooT® Root Cause Analysis System, we offer the investigator the option to stop the investigation after collecting information if there is nothing more to learn. This prevents wasting time investigating incidents that can’t provide a positive return on the investigation investment. THIS ARTICLE explains more about this decision.
Once you have determined that the incident is worth investigating, you can apply advanced root cause analysis.
What is Wrong with Root Cause Analysis?
Not all root cause analyses are created equal. Some techniques fool investigators into concluding that they have found root causes when all the investigative effort just allows them to confirm their foregone conclusions. These tools are based on cause and effect. They include 5-Whys and Fishbone Diagrams.
What makes these types of root cause analysis substandard? Two things:
- Confirmation bias, and
- No guidance beyond the investigator’s current knowledge.
Would you like to read more about these problems and how they can negatively impact your root cause analysis? CLICK HERE for an article we wrote about the causes of these problems in 2007.
Even though these methods have recognized shortcomings, people often mistake the activity when using these methods as progress.
Watch the video above for some of those shortcomings.

But, as John Wooden, a famous UCLA basketball coach, wrote:
“Don’t mistake activity for achievement. To produce results, tasks
must be well organized and properly executed; otherwise,
it’s no different from children running around the playground—
everybody is doing something, but nothing is being done;
lots of activity, no achievement.”
Can You Build a Better “Mousetrap?”

To avoid common investigation mistakes, you need to develop a system that avoids the common investigation traps. To do this, you must discover the fundamentals of root cause analysis and incident investigation. But you will need much more knowledge than that. You will need knowledge of:
- Human factors,
- Equipment engineering,
- Maintenance best practices,
- Operations research,
- Management theory,
- Ergonomics, and
- Training theory
just for starters.
Then, it will take you a couple of years to design a system that is easy for people in the field and experts to use. Next, you will need hundreds of investigations to test the system and the training to improve it over time. Finally, you will need to design and program software to make the system easier to use and more powerful when analyzing data.
How long will that take? Four to five years if you are good and lucky.
Adopt a World-Class System
Or, instead of trying to reinvent the wheel, you could adopt an industry-leading system that has already done all this development and more. What system is that? TapRooT® Root Cause Analysis.
Would you like to learn more about the development of the TapRooT® Root Cause Analysis System? Just CLICK HERE for some details. Or read this WHITE PAPER to see how the TapRooT® System works.
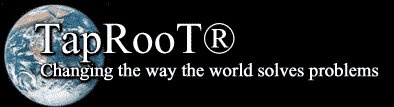
Perhaps an even better way to learn the value of adopting a world-class root cause analysis system is to attend a TapRooT® Root Cause Analysis Course. CLICK HERE to see the upcoming public TapRooT® Courses.
If you aren’t sure about the investment required to learn TapRooT® Root Cause Analysis and then try it to solve your toughest problems, see our course guarantee below.
Guaranteed Training
Attend a TapRooT® Course, go back to work, and use what you have learned to analyze accidents, incidents, near-misses, equipment failures, operating issues, or quality problems. If you don’t find root causes that you previously would have overlooked and if you and your management don’t agree that the corrective actions that you recommend are much more effective, just return your course materials, and we will refund the entire course fee.
How is that for an iron-clad guarantee?
What TapRooT® RCA Users Are Saying
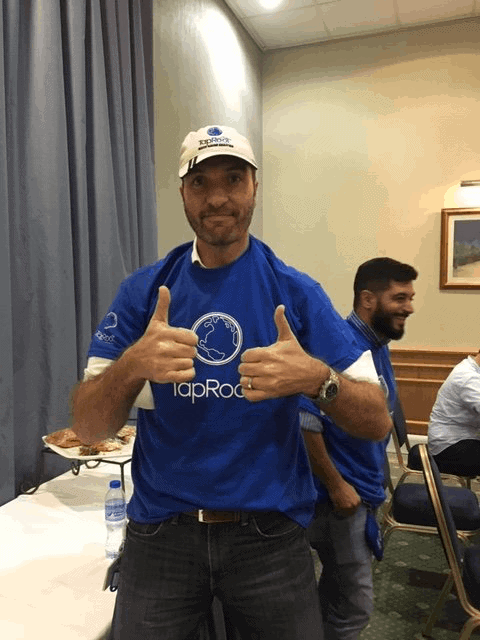
TapRooT® RCA is used by over a hundred thousand people at industry-leading companies around the world. Here are comments from just four of those using TapRooT® RCA to investigate and solve problems:
Plant Manager: “In just the first year, we saved $40 million in plant downtime by applying TapRooT®.”
Reliability Engineer: “Unbelievably professional – a world-class course.”
OSHA Inspector: “I’ve been investigating accidents for over 20 years. Even with all my experience, I was surprised by how much I learned. This is the best training I’ve ever had.”
Safety Manager: “Since using TapRooT®, we are finding fixable root causes that we would not have found using our previous investigation methods.”
To see TapRooT® User Success Stories, CLICK HERE.
Advanced Knowledge at Our Summit

Once you have learned to use the TapRooT® System, you will be ready to take your company’s performance to the next level. That is why we organized the Global TapRooT® Summit – our annual conference for sharing best practices, networking, and learning from experts from around the world. Learn more about all the advantages attending the next Summit provides by CLICKING HERE.
Get Started NOW!

Register for a Public TapRooT® Course by CLICKING HERE and picking the upcoming course that best fits your schedule. Or CONTACT US to arrange a course at your site.
Would you like to schedule an Executive Briefing? CLICK HERE.
To register for the Global TapRooT® Summit, CLICK HERE.
