How Does Routine Maintenance Have a Fatal Outcome?
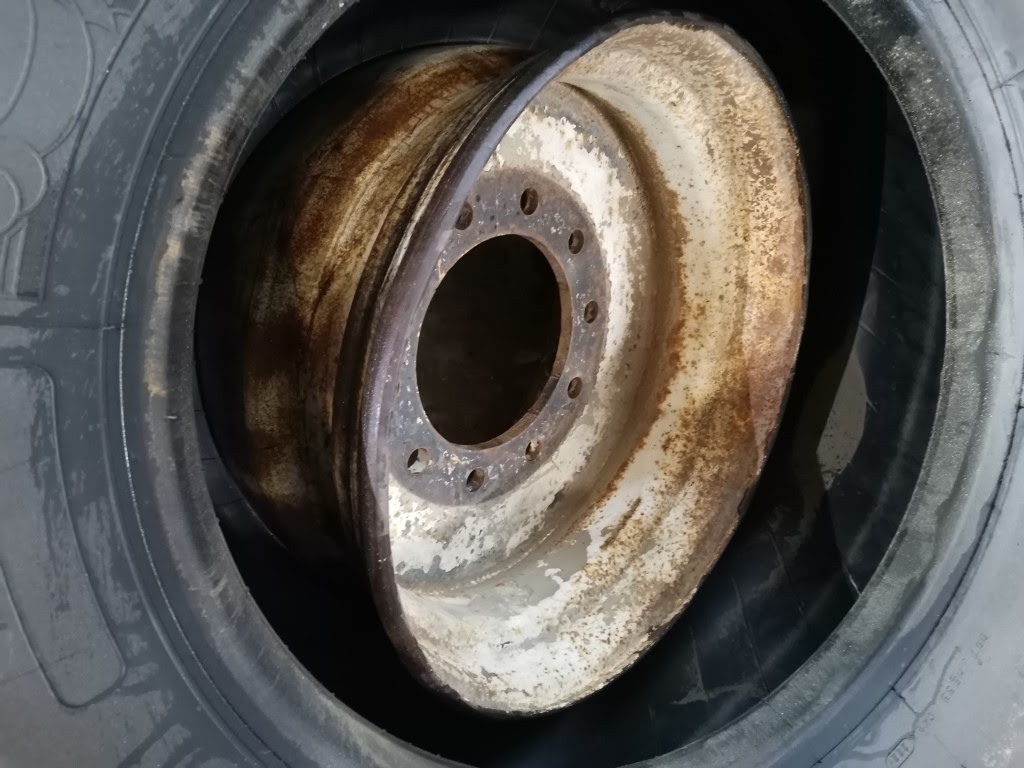
IOGP (The International Association of Oil & Gas Producers) was recently alerted to two separate incidents, both with fatal outcomes and related to routine maintenance and changing of tires on vehicles.
“These routine maintenance incidents represent opportunities to highlight risk areas that were insufficiently recognized in our industry” — IOGP.
- On September 12, 2021, a contracted tire technician was fatally struck by a heavy vehicle tire and a tire rim which ejected after a sudden failure.
- On December 23, 2021, an employee was fatally struck by a heavy vehicle tire rim during maintenance.
Both incidents happened during routine maintenance — both activities were in controlled logistics environments.
The trucks involved were heavy and used in rough terrain. Tire inflation pressures were as per manufacturer’s’ recommendations, in the order of 130 psi.
In the first event, a new tire was already mounted on the one-piece rim after having been previously inflated inside a safety cage, and it was resting outside the cage, awaiting installation on a truck. A maintenance technician noticed some air leaking from it and approached it. While the technician was inspecting/troubleshooting the tire, the wheel parted, releasing the rim which hit the technician on the head.
In the second event, a driver was loosening the lug nuts of a heavy vehicle wheel that had been reported defective by a previous shift driver, with the intention of replacing it with a spare. The rim catastrophically failed and cracked in two, releasing the tire and part of the rim with explosive force
and projecting the driver several meters away.
Following these routine maintenance incidents, prior damage was noted on the tire rims in both cases.
This may either have occurred through wear and tear during rough terrain driving or potentially through driving with a partially deflated tire. Subsequent wider inspection of tires and tire rims revealed that such cases are not limited to the incident vehicles in isolation.
What went wrong?
• In both incidents, workers were in the line of fire from a pressure hazard and had not recognized this as a risk.
• In both incidents, the tires were not deflated prior to troubleshooting task commencing.
• In one incident, substandard practice was noted, in that the wheel was removed from its cage without inspection of the rim seat area.
• In both incidents, tire rim damage had been sustained and not recognized. Subsequent inspection of other vehicles found cases of cracks and damage.
• In first incident, OEM recommendations for tire rim inspection had not been followed.
• In the second incident, learnings from the first incident had been insufficiently embedded.
Corrective actions and recommendations
- Reinforce line of fire awareness with all personnel and the importance of avoiding body positioning in the of line of fire.
- Procure and raise awareness of tools and methods that enable humans to perform any activities related to tires, such as inflation and deflation, away from the line of fire.
- Perform immediate tire and tire rim inspections across the fleet of vehicles and verify inclusion of both tires and tire rims in vehicle inspection programs.
- Reinforce the hazard of tires and tire rim damage through reflective learning or similar activities.
- Raise awareness of the need to deflate tires before removal from the vehicle.
- Raise awareness of the general risk of pressure release from tires and different modalities where such release can occur.
- Attain a deeper understanding of tire rim construction, types and inspection requirements as per OEM recommendations.
- Reinforce the requirement to monitor for weak signals with respect to tire and tire rim construction during driving. Stop the job in case anomalies are noted.
- Reinforce the availability of learnings from previous incidents.
Source: IOGP, IOGP Alert 331, “Technician fatalities,”Feb. 2022.”
Safety and quality experts already know that TapRooT® Root Cause Analysis is the best tool to find human-performance-based root causes
TapRooT® RCA is the only system that uses scientifically derived root causes to eliminate bias and avoid blame. So, what are they missing? That Equifactor® Equipment Troubleshooting should be used WHENEVER there is an equipment failure.
Equifactor® equips the user with a series of predefined equipment troubleshooting tables. For example, there are tables for different types of pumps, AC and DC motors, refrigeration units, etc. These tables will give you a list of symptoms to choose from, and then provide an extensive list of possible causes for that symptom.
EQUIFACTOR® IS AN EFFECTIVE WAY TO GIVE YOUR MAINTENANCE AND RELIABILITY EXPERTS A VALID LIST OF POSSIBLE CAUSES TO BEGIN THEIR TROUBLESHOOTING EFFORTS.
So when would you use these Equifactor® Tables in your TapRooT® Investigation? The series of predefined equipment troubleshooting tables are obviously a great resource for an equipment failure incident. The tables give you a list of symptoms to choose from. However, don’t limit yourself to the obvious investigations. For example:
- You can also use Equifactor® during an injury investigation if one of your Causal Factors happens to be an equipment failure.
- Similarly, during an investigation of a Quality deviation, you may find a failure of a piece of equipment on the manufacturing line. Again, it could be employed to better understand the causes of the equipment failure (probably a Causal Factor), which will then lead to a better root cause analysis.
Use Equifactor® anytime an equipment failure is involved in your investigation. It’s an effective, efficient way to make sure you are fully covering all the possible errors and failures during your TapRooT® analysis.
Get the new book & a masterclass of learning in an Equifactor® Troubleshooting Course
The recently remastered 2-Day Equifactor® Equipment Troubleshooting & TapRooT® Root Cause Analysis Course comprises the complete package, as students receive the course, the new book, and the workbook. Take a look at the full course description.
Now is a great opportunity to get your maintenance personnel, equipment operators, and supervisors trained to increase equipment reliability at your plant.
We are excited to share with you the upcoming public Equifactor® courses. Reach out to us if you have any questions. To discuss on-site course arrangements, call us: 865.539.2139.