How Important Is Improvement?
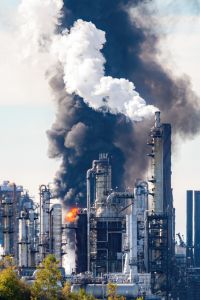
What Are Your Biggest Problems
Before judging how important improvement is, you need to understand your biggest problems. For example:
- Do you still have fatalities at your site?
- Do significant injuries occur more often than you would like?
- Have you had major environmental releases that impacted surrounding communities?
- Have you received regulatory fines or actions?
- Have you lost customers because of poor quality?
- Have you had accidents that caused significant damage to your facility?
- Have you received negative press because of your facility’s performance?
- Is your facility’s performance significantly worse or more expensive than other facilities in the company/industry?
- Is your facility unprofitable?
- Has senior management dictated spending freezes or downsizing of personnel?
- Are workers afraid to report problems or hazards to management?
- Is blame the first response from employees or management when something goes wrong?
- Does unreliable equipment cause production delays, missed customer shipments, or expensive rework?
- Do you have a significant backlog of preventive/predictive maintenance?
- Do you have mystery incidents/accidents where root causes can’t be identified?
- Is human error a major cause of issues at your facility?
- Are improvement programs considered the “flavor of the month” and ignored by line workers?
- Do you lack management support for your improvement efforts?
- Do you lack an accurate picture of the cost of injuries, poor quality, equipment failures, and plant reliability issues?
That’s a pretty depressing list. If you have even one of those issues, you need to get to work making improvements. But before you start, you need accurate measures to see if improvement is happening and show management what they will be getting for their improvement investment.
Measuring Improvement
A lot has been written about measuring performance. One of our volumes in the TapRooT® 10-book set is all about performance measures and trending,,,
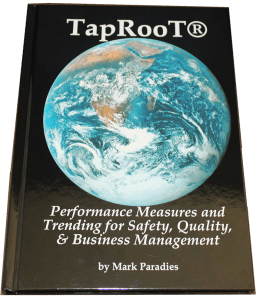
However, I’m still surprised by the number of companies that have problems but don’t have an accurate, agreed-upon set of measures to determine whether improvement is occurring (or even if the problem is getting worse).
Therefore, if you have issues you want to correct (improve), I would recommend developing effective measures to track progress when you implement your improvement ideas.
Ideas for Improving Performance
Now that you have measures to track performance, you can start making improvement happen. But where do you start?
Start Reactively
I suggest starting with advanced root cause analysis. Apply it whenever an incident occurs that contributes to the problem you are trying to solve.
Don’t just wait for major accidents. Use advanced root cause analysis to tackle precursor incidents. Read more about which precursor incidents you should investigate HERE.
See THIS white paper for a description of using advanced root cause analysis to investigate precursor incidents. Then, learn more about advanced root cause analysis by taking one of THESE COURSES.
Next, Become Proactive
Book 6 of the 10-book TapRooT® Set is about proactive improvement. Read about moving from being reactive to being proactive HERE.

The fastest way to learn to use advanced root cause analysis proactively is to take the 2-Day Auditing & Proactive Improvement Using TapRooT® RCA Course. Find out more about the course HERE.
Learn Best Practices
Another way to rapidly improve performance is by implementing best practices from other high-performance sites. Where can you learn these best practices? At the Global TapRooT® Summit.
What is the Summit all about? Watch this video to find out more.
There are eight Best Practice Tracks at the 2025 Global TapRooT® Summit. They are…
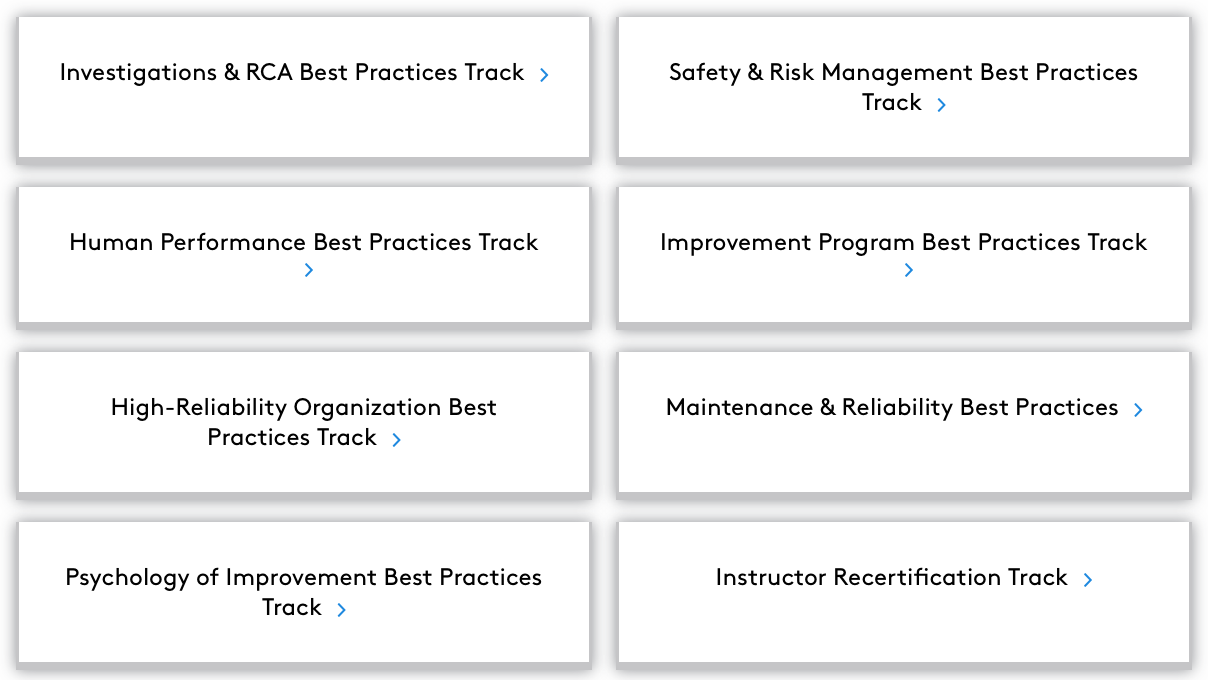
Click on the figure above to find out more about each track. And don’t forget that you can customize your Summit experience by picking sessions from a variety of tracks when you register. That way, you can customize your learning by concentrating on the topics most important for improvement at your facility.
What are some of the sessions I would suggest? Try these…
- Admiral Rickover’s Original High-Reliability Organization
- “Risky Behaviors” Using TapRooT® RCA to Improve Operational Excellence
- Using AI to Improve Safety and Quality
- Training Beyond the Mistake
- Taking Learning Teams to the Next Level
- From Stress to Success: Fostering Psychological Safety in the Workplace
- Sharing Ideas to Achieve High-Reliability & Performance Roundtable
- Investigations and RCA Best Practices Roundtable
- Developing and Using a Lessons Learned Program
And that’s just a sample. See the complete schedule HERE.
When is the Summit? October 1-3. Where is the Summit? Knoxville, TN, at the Knoxville Convention Center. The pre-Summit Courses are from September 29 to 30.
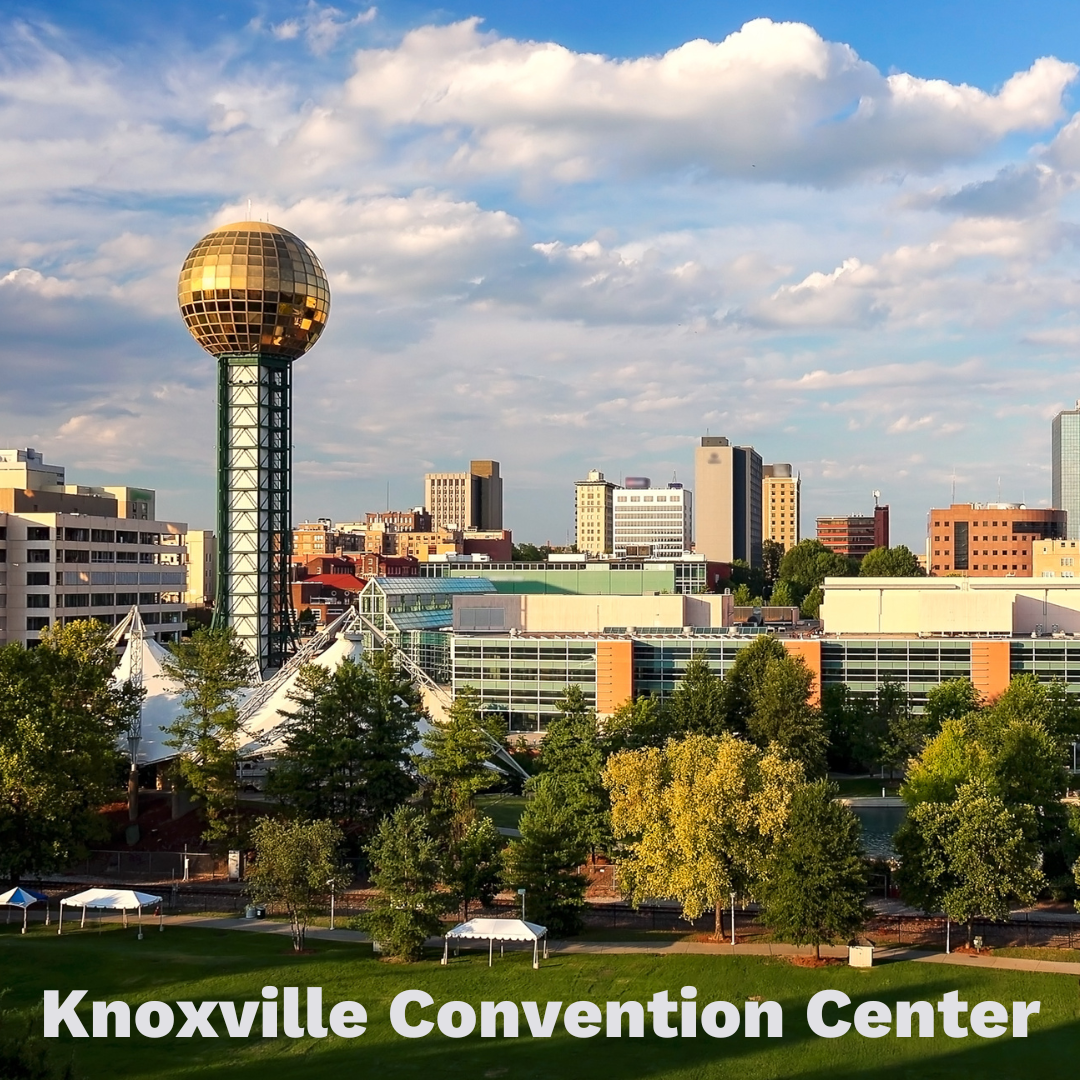
To register for the Summit, CLICK HERE.