How Much Does an Accident Cost?
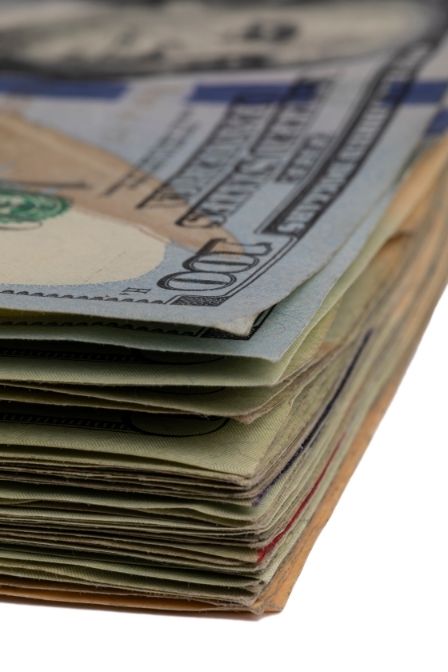
See the OSHA’s “$afety Pays” Calculation
OSHA has an online calculator to help you find the total cost of an accident. See it at:
https://www.osha.gov/safetypays/estimator
For more information on the basis for this calculator, see:
https://www.osha.gov/safetypays/background
What Was the Most Costly Accident in Recent History?
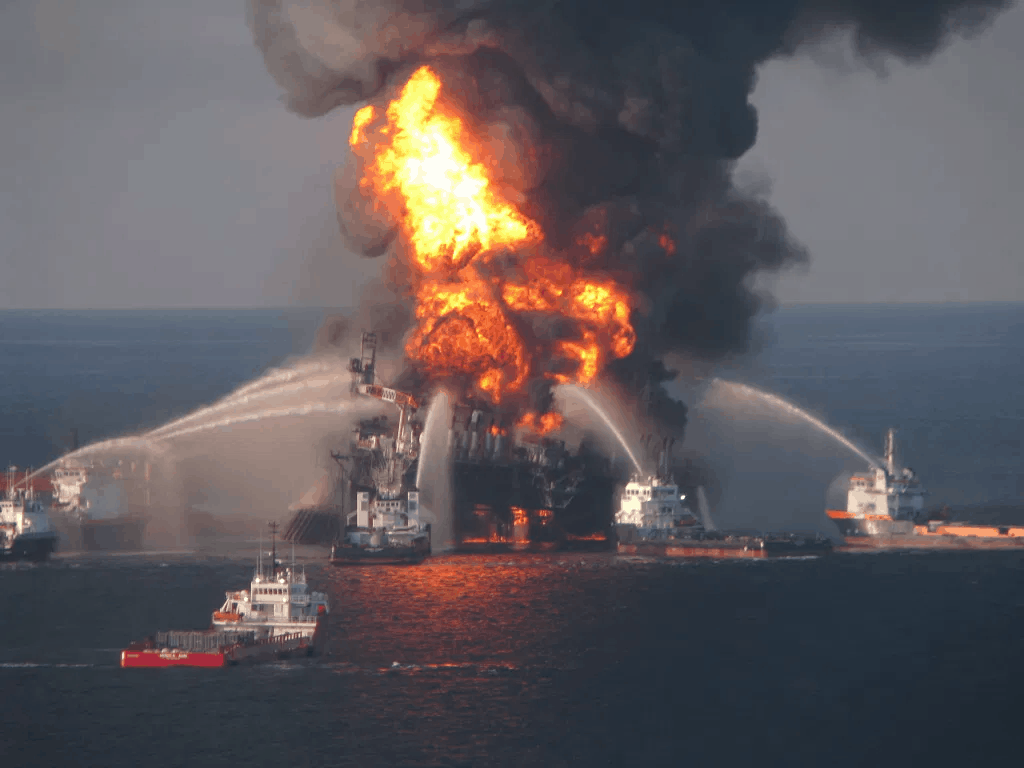
I would guess that the Deepwater Horizon blowout, explosion, and oil spill was the most costly accident in recent times. First, there were 11 killed. Then, there was over $65 billion in direct costs. An estimate of the total costs might exceed $100 billion. And the accident was preventable.
Effective root cause analysis and corrective actions to prior incidents and accidents could have provided the lessons learned to stop the Deepwater Horizon accident.
Good Root Cause Analysis Can $ave
Repeated incidents and accidents can be costly. If you have an incident, an effective investigation with advanced root cause analysis that leads to effective corrective actions can prevent costly repeat incidents and accidents.
Why do so many companies have repeat incidents?
- Poor evidence collection and lack of understanding of what happened.
- Poor root cause analysis using substandard techniques (for example, 5-Whys).
- Poor corrective actions (doing the same old ineffective corrective actions over and over again, for example – retaining).
What can you do to prevent repeat incidents? Learn the TapRooT® Root Cause Analysis System.
TapRooT® Root Cause Analysis has:
- The SnapCharT® Diagram to help you collect and organize your information about an incident.
- The Root Cause Tree® Diagram and Dictionary that leads the investigator to the fixable causes of human performance and equipment failure issues.
- The Corrective Action Helper® Guide that helps the investigator develop outside-the-box corrective actions to fix human performance and equipment reliability-related root causes.
Plus, all these techniques are built into the patented TapRooT® Software.
For an example of an environmental accident that demonstrates how the TapRooT® RCA System works, see THIS LINK.
Then hold a TapRooT® Course at your site (get a quote by CLICKING HERE) or attend one of our upcoming public TapRooT® Courses. See the dates and locations by CLICKING HERE.
Being Proactive Can Have Even Better ROI
What works even better than reactive root cause analysis? Proactive root cause analysis.
How does proactive root cause analysis work?
First, you can read more about it in Book 6 of the 10-book set, TapRooT® Root Cause Analysis for Audits and Proactive Improvement.
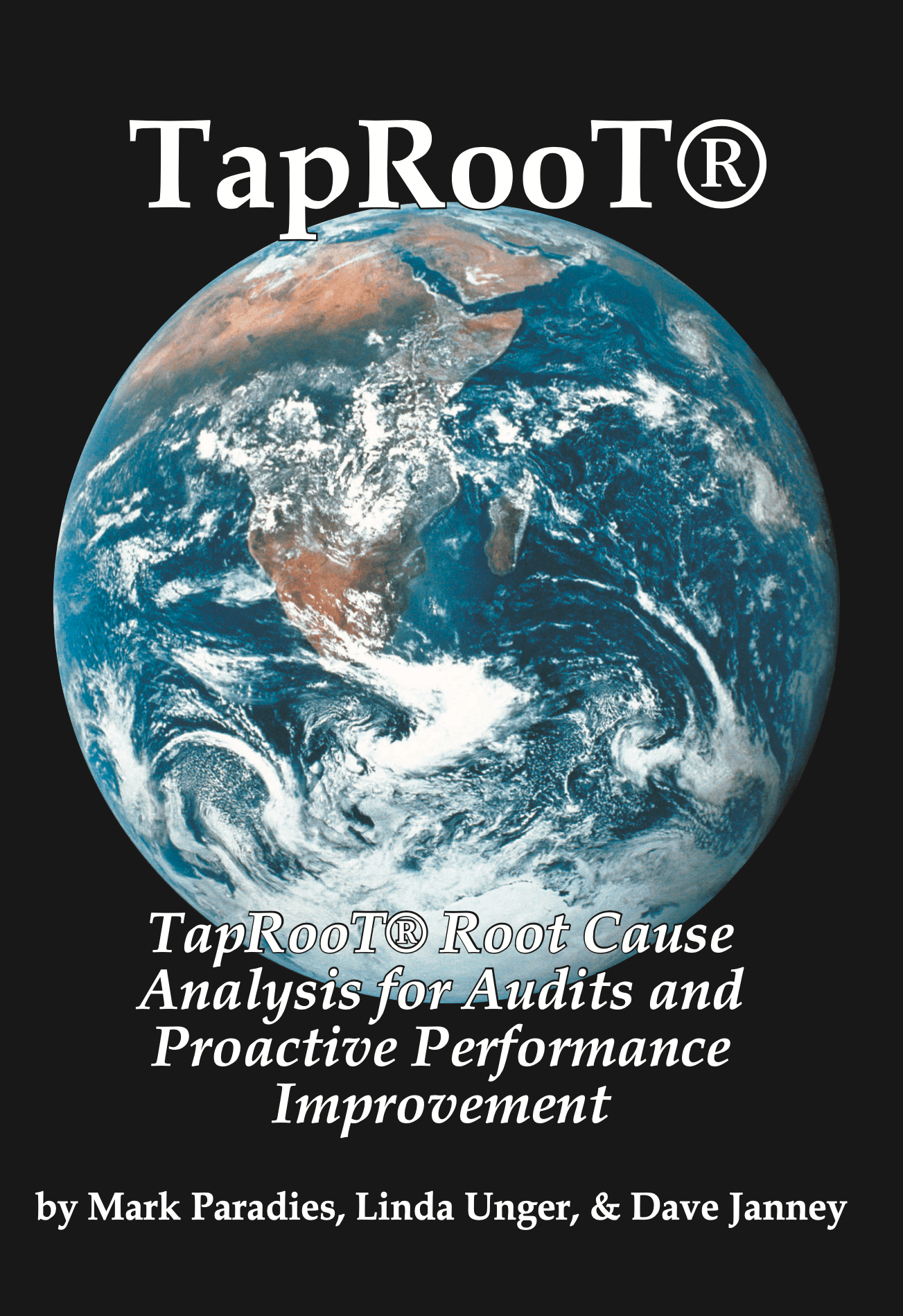
CLICK HERE to order a copy.
Next, you read a short article about being proactive HERE.
Finally, find out more about our 2-Day Auditing & Proactive Improvement Using TapRooT® RCA Course at THIS LINK. Book 6 is included in the course materials.
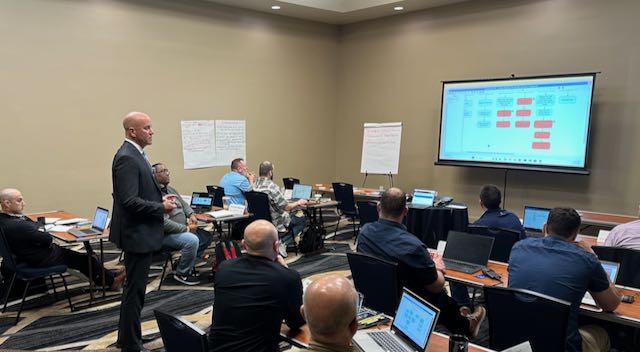