Improving Root Cause Analysis Quality
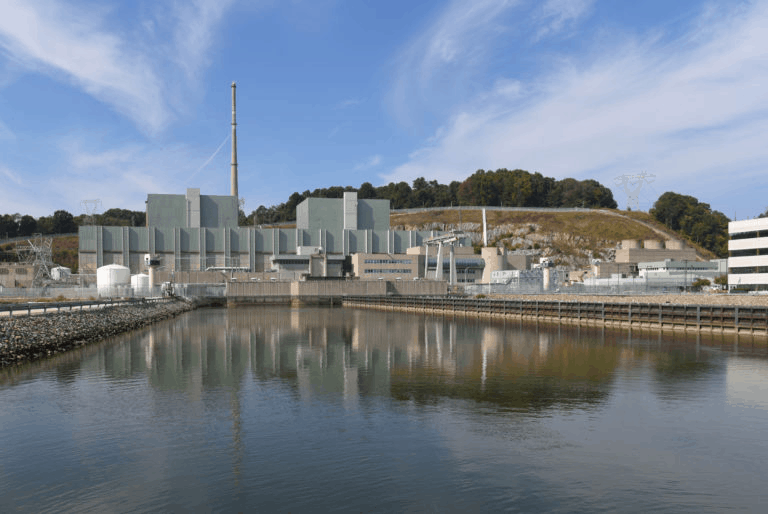
TapRooT® User Success Story
Written by Gary Waldrep
Manager, Corrective Action Program
Exelon Nuclear
This success story was written in the past and is being updated to our most recent blog article format and is being reposted here.
Challenge
The quality of root cause analysis at our five nuclear power plants was criticized by reviewers such as the Nuclear Safety Review Boards, Nuclear Oversight (Quality Assurance), and corporate executives. Our critics noted repeat failures and stated that the investigations often missed the mark and had weak corrective actions. We needed to find a system that would produce consistent quality root cause analysis.
Action
An improvement plan was developed and implemented. Elements of the improvement plan included process improvements to increase line manager involvement, use of a SnapCharT® Diagram, use of an investigation charter, use of the TapRooT® Root Cause Tree® to guide our root cause analysis, and implementation of the TapRooT Software.
We obtained a TapRooT® License Agreement for the five Commonwealth Edison nuclear plant sites, plus the corporate office. Since we were in the midst of a merger, and some of our merger-partner sites were also TapRooT® Clients, the final License Agreement includes all 10 nuclear plant sites plus the corporate office. We also sent a core group of investigators to a 5-Day TapRooT® Root Cause Analysis Team Leader Course.
We replaced our in-house 5-Day root cause analysis class with the 2-Day TapRooT® Root Cause Analysis Class and installed TapRooT® Software on the Local Area Network at each site. We also conducted orientation sessions for plant senior managers.
By the end of April 2001, we had conducted at least one 2-Day TapRooT® Class at each plant site.
Results
The initial reaction to the TapRooT® System by investigators, line managers, and reviewers have been positive. Investigators like the structured approach. Line managers like consistent results. Reviewers like consistent quality. Investigators and line managers also like savings training time. The investigators like the TapRooT® Software that includes the SnapCharT® Module.
Our reviewers use a 10-question checklist to grade our root cause analysis reports. Prior to the introduction of the TapRooT® System in September 2000, the average report score was about 50%. Since the introduction of the TapRooT® System, the average report score has risen to about 75%. We anticipate continued improvement as we train additional investigators.
The improvement in the report ratings and the investigators’ and managers’ opinions about our new system (TapRooT®) might not seem like a major improvement, but we have been working for years to improve our root cause analysis and have tried several other systems. Getting this consistent and significant improvement this far along in our quest for better root cause analysis clearly demonstrates to us the value of the TapRooT® System.
One more piece of evidence that shows how much we value the progress that we have made. Our energy delivery districts (transmission and distribution) needed improved root cause analysis to analyze human performance problems that result in outages for our customers. They have been looking for a way to effectively and consistently evaluate their incidents. The corporate nuclear staff presented the TapRooT® System to the corporate energy delivery staff, and they decided that the system would help them effectively improve performance. They are obtaining a license to implement TapRooT® System and Software for the 10 mid-West energy delivery districts to provide our customers with increased power reliability while Exelon realizes cost savings.
(Note: Exelon continues to use the TapRooT® Root Cause Analysis System and Software to this day.)