In-flight load shift on ATR 72 from Guernsey to Jersey (15-minute flight)
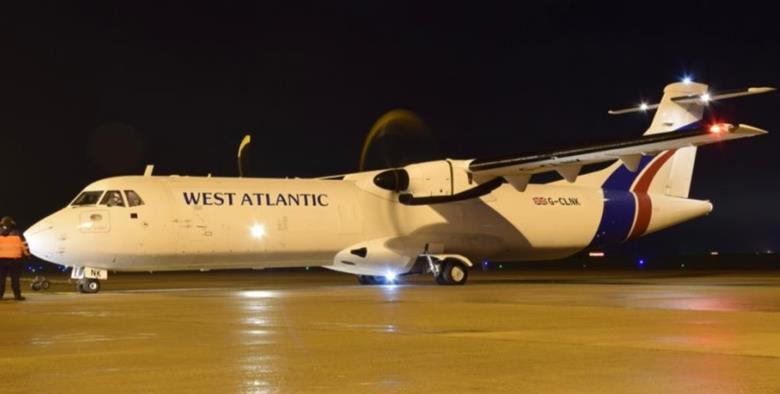
Investigators believe the load — an unsecured cargo container on a West Atlantic ATR 72 freighter — shifted rearward during takeoff, then forward during landing, after floor locks were not engaged.
Despite the substantial shift of the centrally loaded ULD (Unit Load Device) container, the ATR 72 aircraft remained within forward and aft balance limits during its flight from Guernsey airport to Jersey, in the Channel Islands, on April 16, 2021.
The ATR 72 aircraft arrived at Guernsey from East Midlands fully loaded, with each of the five cargo bays – designated C1 to C5, forward to aft – containing a ULD.
Two of these ULDs were unloaded and the three remaining ones were reconfigured to sit in bays C1, C3 and C5. Bays C2 and C4 were left empty.
Each ULD would normally be secured by floor locks forward and aft of the container.
But the ULD in C3 was not properly secured because the aft floor locks, designed to stop the container shifting backwards, were not raised into position beforehand. Only the locks to prevent forward movement were correctly engaged.
The ground-handling organization was unable to determine how the ULD had stopped in the correct position without the rear locks acting as a barrier.
“It was considered that a combination of friction of the ULD as it was moved rearward on the rails, the visual cues of the green marker on the fuselage wall, and the forward locks becoming visible on the bay floor as the container moved over them probably resulted in the ULD being positioned so that the forward locks could be engaged without the rear locks being [raised],” says the UK Air Accidents Investigation Branch (AAIB).
As the aircraft took off, the pilots heard a “slight thud,” which they attributed to movement of water bottles in the cabin. But the inquiry sides with the belief that they actually heard the ULD in C3 sliding backwards into empty bay C4.
Neither crew member noticed any change to the feel or control of the aircraft during the short 15-minute flight to Jersey.
But when the aircraft touched down and decelerated, the pilots heard a sliding noise and a “loud thud,” which was “felt throughout the airframe” as the ULD slid from bay C4 with sufficient force to break the forward locks in bay C3, continue through bay C2 and ram into the locks holding the ULD in bay C1.
While the loading rails and locks were damaged, the ULDs and the aircraft structure were not.
The ground-handling organization carried out its own investigation and found that the loader “may have been distracted,” but also determined that there was no requirement for an independent check of the locks as ULDs were loaded.
It has since revised procedures to introduce such a check, while the aircraft operator has taken training steps to raise awareness of the risks of “empty bay’”operations.
Source: Flight Global, “Load shifted on ATR 72 freighter after floor locks left unchecked,” David Kaminski-Morrow, Feb. 10, 2022.
Safety and quality experts already know that TapRooT® Root Cause Analysis is the best tool to find human-performance-based root causes.
TapRooT® RCA is the only system that uses scientifically derived root causes to eliminate bias and avoid blame. So, what are they missing? That Equifactor® Equipment Troubleshooting should be used WHENEVER there is an equipment failure.
Equifactor® equips the user with a series of predefined equipment troubleshooting tables. For example, there are tables for different types of pumps, AC and DC motors, refrigeration units, etc. These tables will give you a list of symptoms to choose from, and then provide an extensive list of possible causes for that symptom.
EQUIFACTOR® IS AN EFFECTIVE WAY TO GIVE YOUR MAINTENANCE AND RELIABILITY EXPERTS A VALID LIST OF POSSIBLE CAUSES TO BEGIN THEIR TROUBLESHOOTING EFFORTS.
So when would you use these Equifactor® Tables in your TapRooT® Investigation? The series of predefined equipment troubleshooting tables are obviously a great resource for an equipment failure incident. The tables give you a list of symptoms to choose from. However, don’t limit yourself to the obvious investigations. For example:
- You can also use Equifactor® during an injury investigation if one of your Causal Factors happens to be an equipment failure.
- Similarly, during an investigation of a Quality deviation, you may find a failure of a piece of equipment on the manufacturing line. Again, it could be employed to better understand the causes of the equipment failure (probably a Causal Factor), which will then lead to a better root cause analysis.
Use Equifactor® anytime an equipment failure is involved in your investigation. It’s an effective, efficient way to make sure you are fully covering all the possible errors and failures during your TapRooT® analysis.
Get the new book & a masterclass of learning in an Equifactor® Troubleshooting Course
The recently remastered 2-Day Equifactor® Equipment Troubleshooting & TapRooT® Root Cause Analysis Course comprises the complete package, as students receive the course, the new book, and the workbook. Take a look at the full course description.
Now is a great opportunity to get your maintenance personnel, equipment operators, and supervisors trained to increase equipment reliability at your plant.
We are excited to share with you the upcoming public Equifactor® courses. Reach out to us if you have any questions. To discuss on-site course arrangements, call us: 865.539.2139.
Attend the best conference for smart workers and safe clients: The 2022 Global TapRooT® Summit
There’s a good reason why, since 1994, hundreds of companies make it a priority to send experts and /teams to the Global TapRooT® Summit: The attendees bring back game-changing information and tips on how their companies can improve performance while keeping their record clean and their employees and clients working safe and all on the same page. You should, too.
In 1994, we started the TapRooT® Summit as a three-day meeting of the best TapRooT® users. The Summit has grown into an international event with world-renowned session and keynote speakers and multiple tracks designed to share performance improvement best practices across industries and professions.
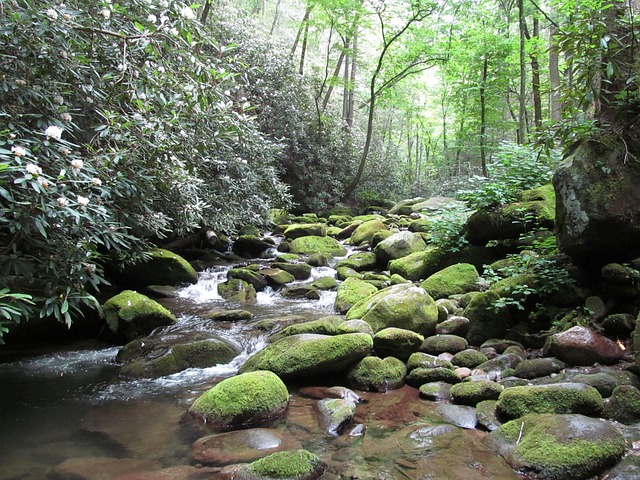
Make plans to join us for the 2025 Global TapRooT® Summit in Knoxville, Tennessee, in October, when you’re going to want to wander nearby to the Great Smoky Mountains National Park for leaf-peeping, down-home dishes and delicacies, and the wonderful peacefulness of water rushing over age-old stones. There’s a reason why the Smoky Mountains is America’s number-one national park and it’s all right here for you to discover. Stay tuned for more Summit information!