Is There Just One Root Cause for a Major Accident?
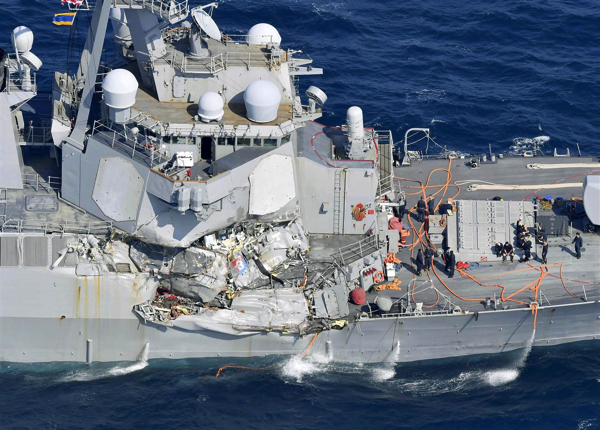
Major Accident – One Root Cause?
Some people might say that the Officer of The Deck on the USS Fitzgerald goofed up. He turned in front of a containership and caused an accident.
Wait a second. Major accidents are NEVER that simple. There are almost always multiple things that go wrong, multiple “Causal Factors” that could be eliminated, and … if they were … would have prevented the accident or significantly reduced its consequences.
The “One Root Cause” assumption gets many investigators in trouble when performing a root cause analysis. They think they can ask “why” five times and find THE ROOT CAUSE.
TapRooT® Root Cause Analysis
TapRooT® Investigators never make this “single root cause” mistake. They start by developing a complete sequence of events that led to the accident. They do this by drawing a SnapCharT® (either using yellow stickies or using the TapRooT® Software).
They then use one of several methods to make sure they identify ALL the Causal Factors.
When they have identified the Causal Factors, they aren’t done. They are just getting started.
EACH of the Causal Factors are taken through the TapRooT® Root Cause Tree®, using the Root Cause Tree® Dictionary, and all the root causes for each Causal Factor are identified.
That’s right. There may be more than one root cause for each Causal Factor. Think of it as there may be more than one best practice to implement to prevent that Causal Factor from happening again.
TapRooT® Investigators go even one step further. They look for Generic Causes.
What is a Generic Cause? The system problem that allowed the root cause to exist.
Here’s a simple example. Let’s say that you find a simple typo in a procedure. That typo cause an error.
Of course, you would fix the typo. But you would also ask …
Why was the typo allowed to exist?
Wasn’t there a proofing process? Why didn’t operators who used the procedure in the past report the problem they spotted (assuming that this is the first time there was an error and the procedure had been used before)?
You might find that there is an ineffective proofing process or that the proofing process isn’t being performed. You might find that operators had previously reported the problem but it had never been fixed.
If you find there is a Generic Cause, you then have to think about all the other procedures that might have similar problems and how to fix the system problem (or problems). Of course, ideas to help you do this are included in the TapRooT® Corrective Action Helper® Guide.
What Did We Learn?
So, in a major accident like the wreck of the USS Fitzgerald, there are probably multiple mistakes that were made (multiple Causal Factors), multiple root causes, some Generic Causes, and lots of corrective actions that could improve performance and stop future collisions.
To learn advanced root cause analysis, attend a public TapRooT® Courses. See the dates and locations here:
http://www.taproot.com/store/Courses/
Or schedule a course at your facility for 10 or more people. CLICK HERE to get a quote for a course at your site.