Lean, Six Sigma, and Lean-Six Sigma – What Do They Need to Advance into the 21st Century?
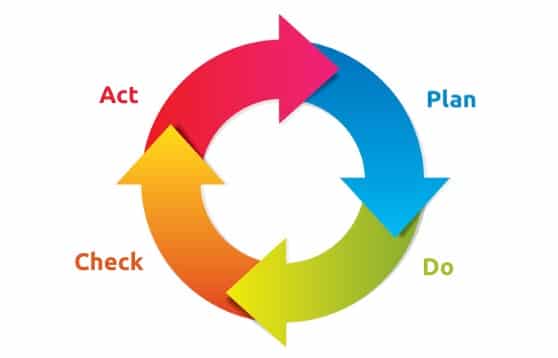
Lean, Six Sigma, and Lean-Six Sigma are based on tools developed in the 1950’s and 1960’s. They were standardized in the 1970’s and popularized in the 1980’s and 1990’s. They have remained relatively unchanged since.
What must be done to bring these improvement systems up to 21st-century standards?
I believe the biggest need for improvement is their root cause tools.
Almost all implementations of Lean, Six Sigma, and Lean-Six Sigma use one of the following root cause tools:
- 5-Whys
- Fishbone Diagrams
- Current Reality Tree
- FMEA
- Fault Trees
All of these techniques are based on the theory of cause and effect. The most common of these cause-and-effect techniques is 5-Whys.
The biggest problems with cause-and-effect and 5-Whys are:
- No guidance for human error investigations
- Jumping to conclusions
- Confirmation bias
- Blame focus (who did it – see 5-Whys and Who Do We Fire?)
- Focus on a single cause
For more about the limitations of cause-and-effect-based tools, see:
- Root Cause Analysis Tip: Why Did The Robot Stop? (Comparing 5-Why Results with TapRooT® Root Cause Analysis Results)
- Dunning-Kruger Effect – Another Reason You Need TapRooT® Root Cause Analysis
- Scientific Method and Root Cause Analysis
- What’s Fundamentally Wrong with 5-Whys?
What can be done to fix these problems and bring your root cause analysis system into the 21st Century? Start using advanced root cause analysis developed for the 21st Century – TapRooT®!
TapRooT® research and development started in the late 1980’s. Early versions were developed and tested in the 1990’s. The latest improvements were started in 2015 and should be completed this year.
For a brief history of TapRooT® see: The History of TapRooT®.
But how will TapRooT® Root Cause Analysis improve your Lean or Six Sigma system?
Here is a video where Mark Paradies explains to Kathy Ireland what makes TapRooT® so special…
Read more about what makes TapRooT® superior root cause analysis at: TapRooT® Advantage.
Probably the best way to become convinced of the value of TapRooT® is to try it on some of your toughest problems. To do that, you need TapRooT® Training. I would recommend the 5-Day TapRooT® Advanced Root Cause Analysis Team Leader Training.
Worried that you may be wasting your time? Don’t worry … the training is GUARANTEED:
If you don’t find root causes that you previously would have overlooked
and if you and your management don’t agree that the corrective actions
that you recommend are much more effective, just return
your course materials and we will refund the entire course fee.
For a complete list of courses and the course closest to you, CLICK HERE.