Mine Manager Dies During Equipment Maintenance
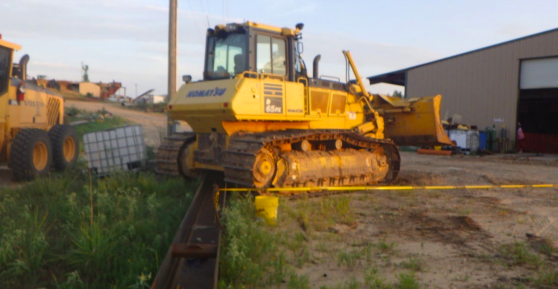
The emphasis on “being safe” while equipment is moving often appears as most important. However, this fatality—in what should have been routine machinery maintenance—underscores how important it is to secure the workspace and have safety features in place even when machinery is not in motion.
The Department of Labor’s Mine Safety and Health Administration report on this accident offers some best practices for this type equipment incident:
• Operators should train miners on safe maintenance procedures:
– turn off the engine
– block machinery against motion
• Operators should make sure miners are in a safe location in relation to machine parts that can move.
This is the 17th fatality reported in 2022, and the seventh classified as “machinery.”
If your company would like to learn more about how TapRooT® Root Cause Analysis can help your mining operation reduce incidents and assist you in saving lives, sign up for one of our public courses.
Would you like a free demonstration on how TapRooT® Root Cause Analysis can improve your safety and reliability program?
Reach out to us with a request for a free demonstration. We look forward to showing you how TapRooT® Root Cause Analysis saves lives, fixes problems, and eliminates equipment failures.
Register for a TapRooT® Root Cause Analysis Training Course
TapRooT® Root Cause Analysis Training courses are taught all over the world. If you are interested in learning how to stop repeat incidents, find a 2-day or 5-day course. We are available to train you and your staff on-site at your workplace; contact us to discuss your needs. You may also call us at 865.539.2139.
Equifactor® Equipment Troubleshooting & TapRooT® Root Cause Analysis are powerful methods to ensure your machinery issues are correctly fixed the first time.
Apply Heinz Bloch’s troubleshooting techniques and the TapRooT® Root Cause Analysis System to understand and prevent equipment failures. This includes developing equipment troubleshooting plans, getting a clear picture of how the failure occurred, and identifying and fixing the root causes of the equipment issues. Companies find there are significant savings when repeat equipment failures are eliminated. Discover how Equifactor® can help you.
Content and image credit: “Fatality Alert,” from the US Department of Labor, Mine Safety & Health Administration.