Quick-Thinking Team Prevents Contamination Breach
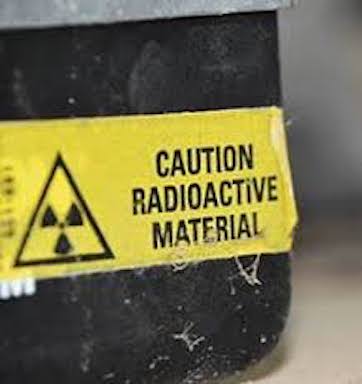
What caused the breach that triggered the alarm to alert the team?
Recently, a researcher was cleaning the interior of a glovebox window when a glovebox differential pressure alarm was activated due to a breach. Remaining calm, the researcher visually surveyed the glovebox work area and realized the left glovebox support ring and glove he was working in had detached outward from the glovebox port creating an opening directly into the glovebox.
The researcher was able to close the gap between the glove and glovebox by pressing his shoulder into the glove ring while simultaneously pulling the left glove into the box with his right glove. Another staff member in the room notified a Radiation Protection Technician (RPT), who immediately responded and re-seated the glove ring. With the assistance of several other RPTs, the researcher was then able to exit the glovebox safely and with minor contamination on his laboratory coat.
Breach prompts lab-wide requirement to install factory-optional locking rings
To better understand why the glovebox ring dislodged from the port, glovebox technicians recreated the event. The technicians discovered that putting significant stress on a glovebox glove could move and dislodge the support ring from the glovebox port. An extent of condition review revealed that PNNL has not consistently utilized locking rings deemed optional by the manufacturer. Use of a locking ring can validate the support ring and glove are installed properly and help keep the support ring and glove in place during operation. PNNL is in the process of updating Laboratory requirements to assure all gloveboxes with push through style glove rings and ports are equipped with locking rings now.
Lessons learned
The differential pressure alarm (design feature) on the air glovebox was helpful in alerting the researcher of the abnormal event with the glovebox. Validate assumptions during design and operations for optional components or suggestions from manufactures or staff. In this case, the manufacturer didn’t require the use of locking rings but if installed, provide validation that the support ring is installed correctly and will prevent the glove support ring from coming out of the glovebox. Although all gloveboxes with push-through style glove rings and ports will soon be equipped with locking rings, staff should be mindful that applying undue pressure on glovebox gloves can result in a breach. Glovebox users can limit stress put on the glove systems by:
- Utilizing reach tools inside the glovebox,
- Asking for assistance from a peer for transferring items,
- Positioning equipment for ideal movement.
This Lesson Learned was published by Pacific Northwest National Laboratory (Richland WA), Richland, WA (PNNL) and disseminated by OPEXShare, The Department of Energy.
Founded in 1988, the TapRooT® Root Cause Analysis System solves hurdles every investigator faces
TapRooT® Root Cause Analysis Training System takes an investigator beyond his or her knowledge to think outside the box. Backed with extensive research in human performance, incident investigation, and root cause analysis, TapRooT® RCA is a global leader in improved investigation effectiveness and productivity, stopping finger-pointing and blame, improving equipment reliability, and fixing operating problems.
System Improvements, the creator of the TapRooT® System, has a team of investigators and instructors with years of extensive training ready to offer assistance worldwide.
TapRooT® Root Cause Analysis Training courses are taught all over the world
If you are interested in learning how to stop repeat incidents, find a 2-Day or 5-Day course; or view the complete selection of TapRooT® courses. We are available to train you and your staff on-site at your workplace; Contact us to discuss your needs. You may also call us at 865.539.2139 to discuss any questions you may have.
Keep in touch to improve your problem-solving skills
We’re continually training, helping you improve your professional root cause analysis skills. Stay current with your TapRooT® Root Cause Analysis skills and training through:
- Following our blog;
- Free newsletters;
- Tuning in to TapRooT® TV Video Sessions or our podcasts;
- Connecting with us on Facebook, Twitter, Instagram, Pinterest, LinkedIn, and YouTube;
- And our annual Global TapRooT® Summit.
Equifactor® Equipment Troubleshooting and TapRooT® Root Cause Analysis Training
Do you need to efficiently and effectively find the root causes of equipment failures to improve your facility’s equipment reliability? Imagine the downtime prevented, and money saved NOT having repeat equipment failures. If this sounds interesting (and worthwhile), then this completely revised TapRooT´® Equifactor® course is for you.
The Equifactor® Techniques are based on the work of noted equipment reliability expert Heinz Bloch. The tools can be used by maintenance personnel, equipment reliability specialists, maintenance managers, or investigators who don’t have an extensive understanding of equipment engineering.
Circumstances can crop up anywhere at any time if proper and safe sequence and procedures are not planned and followed. We encourage you to learn and use the TapRooT® System to find and fix problems.
Contact us to discuss training your employees on-site. You may also call us at 865.539.2139 to speak to an instructor, schedule an executive briefing, or book on-site training for your team. We’re here to find solutions for you.