Regulator’s View on Improving Process Safety with Root Cause Analysis
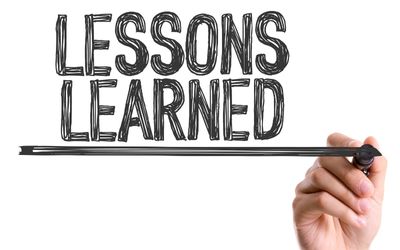
Jay Branson of Delaware OSHA wrote a great article in the December 2010 issue of Process Safety:
“Regulatory Initiative for Improving Process Safety Performance.”
Two key items about incident investigation from the article are:
1. “A key element of process safety is the incident investigation following both severe accidents and near-misses.”
Mr. Branson also writes:
“…investigations become an important part of continuous improvement…”.
This may seem obvious. After all, incident investigation is part of the OSHA PSM regulation. But many (see the next section) don’t do good incident investigations/root cause analysis and miss golden opportunities to avoid major accidents.
2. Mr. Branson’s second comment that I would like to highlight is:
“…there is a wide range of quality of incident investigations.”
Mr. Branson writes that in their regulatory experience (Delaware),
“Some small facilities do not have the expertise
to conduct adequate root cause investigations.”
On the other hand, he writes:
“…large companies may blame the operator
rather than admit to management system failures…”.
Of course, we believe in the importance of incident investigation and root cause analysis as a part of any continuous improvement program (not just PSM). The reason we developed the TapRooT® System was that we saw many programs at big, medium, and small companies that needed improvement.
One might have thought that by now, big, medium, and small companies would have learned about the TapRooT® System and improved their investigations and root cause analysis.
That got me thinking…
Maybe we need to enlist your help?
If you have friends, colleagues, or acquaintances who haven’t discovered TapRooT® RCA, it’s time you had a talk with them.
Tell them about the public TapRooT® Courses.
Forward them a link to the success stories on our website.
Tell them how to sign up for our free newsletter.
You’ll help them save lives and make your industry a better, safer place.
That’s a good thing for everyone.