Six Ways to Improve Root Cause Analysis Efficiency
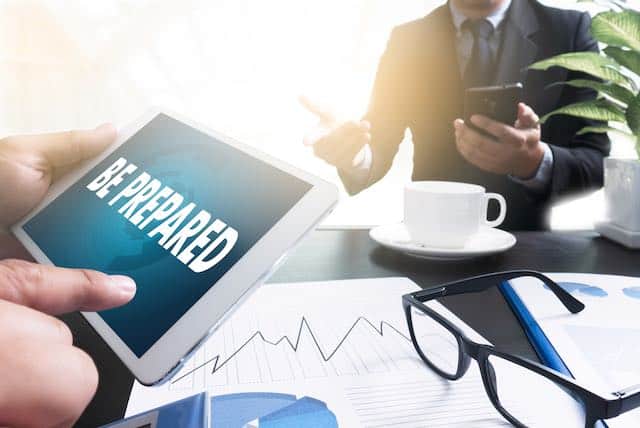
Don’t Have Time for Root Cause Analysis
You have probably heard it: Someone complained that they don’t have time to perform a root cause analysis. But your know that performing a professional root cause analysis is a key part of any improvement effort. So, what should they be complaining about? That they haven’t done everything they could to make their root cause analysis efforts efficient.
That’s why we decided to share these six ways to improve the efficiency of any root cause analysis:
- Have a well-thought-out strategy.
- Use technology.
- Have management that understands root cause analysis.
- Prepare before the investigation.
- Get help from people in the field.
- Properly use a SnapCharT® Diagram.
Let’s look at a little more details about each of these topics.
1. Have a Well-Thought-Out Strategy
You should have a policy that describes when a root cause analysis is needed. That policy should be mindful of the resources required and NOT waste resources on investigating problems where there is NO return on the investigation investment.
Of course, major incidents will require a full investigation by an experienced team. (See Book 4)
Precursor incidents should require a simpler professional investigation by an investigator or a small team using the essential TapRooT® Techniques. (See Book 3.)
And some incidents may require no investigation at all. (See Book 2, pages 64-65 for ideas). )
The best way to save time performing root cause analysis is by not investigating incidents with very little or no potential return on the investigation investment.
2. Use Technology
Technology can simplify your root cause analysis. That’s one of the reasons we developed the patented TapRooT® Root Cause Analysis Software.
What can the TapRooT® Software do for you?
- Help you record and organize your investigation information using the SnapCharT® Module of the software.
- Help you troubleshoot equipment problems using the Equifactor Troubleshooting Module of the software.
- Help you use the Root Cause Tree® Diagram more efficiently by providing dictionary definitions at a click and providing an easy way to record your reasons for selecting particular root causes based on the evidence you collected.
- Suggest effective improvement ideas (corrective actions) for the root cause you identify using the copyrighted Corrective Action Helper® Module of the software..
And that’s just a start.
3. Have Management That Understands Root Cause Analysis
What happens if management doesn’t understand root cause analysis? They don’t know what to look for when you present your results. This can lead to frustration when they ask unwarranted questions or even send the root cause analysis back for “fixing.”
That’s why we created the TapRooT® Executive Leadership’s Role in Root Cause Analysis Course. See the details HERE.
4. Prepare Before the Investigation
What does a waste of time look like? Sending untrained, unprepared investigators out to find root causes using only the knowledge that they have. But how many times have we seen this type of time-wasting investigation?
What should you do to prepare?
- Train your investigators.
- Make sure they gain experience gradually.
- Have refresher training for investigators.
- Have training for anyone involved in investigations (even witnesses) – general employee training.
- Have training for management (see above).
- Pre-plan evidence collection and preservation after an incident (make sure field personnel don’t discard evidence).
- Have initial observation forms for immediate collection of what people saw (see Book 7).
- Be prepared for interviews (see Book 7).
For more on preparing for an investigation, read Book 7.
5. Get Help from People in the Field
If you establish the right investigation/root cause analysis culture, you will get help finding the root causes of problems from people in the field.
What is the right culture? Read about the Opportunity to Improve Vision on page 7 of Book 1.
What is the wrong culture? Read about the Blame Vision and the Crisis Management Vision (also in Book 1).
Companies using TapRooT® RCA either have or are trying to establish the Opportunity to Improve Vision. This helps employees want to participate in root cause analysis.
6. Properly use a SnapCharT® Diagram
We’ve talked about using SnapCharT® Diagrams before HERE. But for a complete guide to using a SnapCharT® Diagram during an investigation, see Book 4, Appendix B, the SnapCharT® Manual.
That’s Six Great Ideas
Would you like to learn more about preparing for and performing an advanced root cause analysis and making your root cause analysis efficient? Then you should consider registering for one of these courses:
5-Day TapRooT® Advanced Root Cause Analysis Team Leader Course
2-Day Equifactor® Equipment Troubleshooting & TapRooT® Root Cause Analysis Course
2-Day Effective Interviewing and Evidence Collection Course
Self-Guided TapRooT® Evidence Collection and Interviewing Techniques Online Course
4-Hour General Employee Training
1-Day TapRooT® Root Cause Analysis Refresher Training
2-Day TapRooT® Advanced Case Study Workshop
That’s seven more ways to be prepared for an efficient root cause analysis. Just click on the course title to learn more about each course.
Plus, HERE are our upcoming public courses.
Hope to see you at a course.