Root Cause Analysis Review Meeting Goes Awry (Friday Joke)
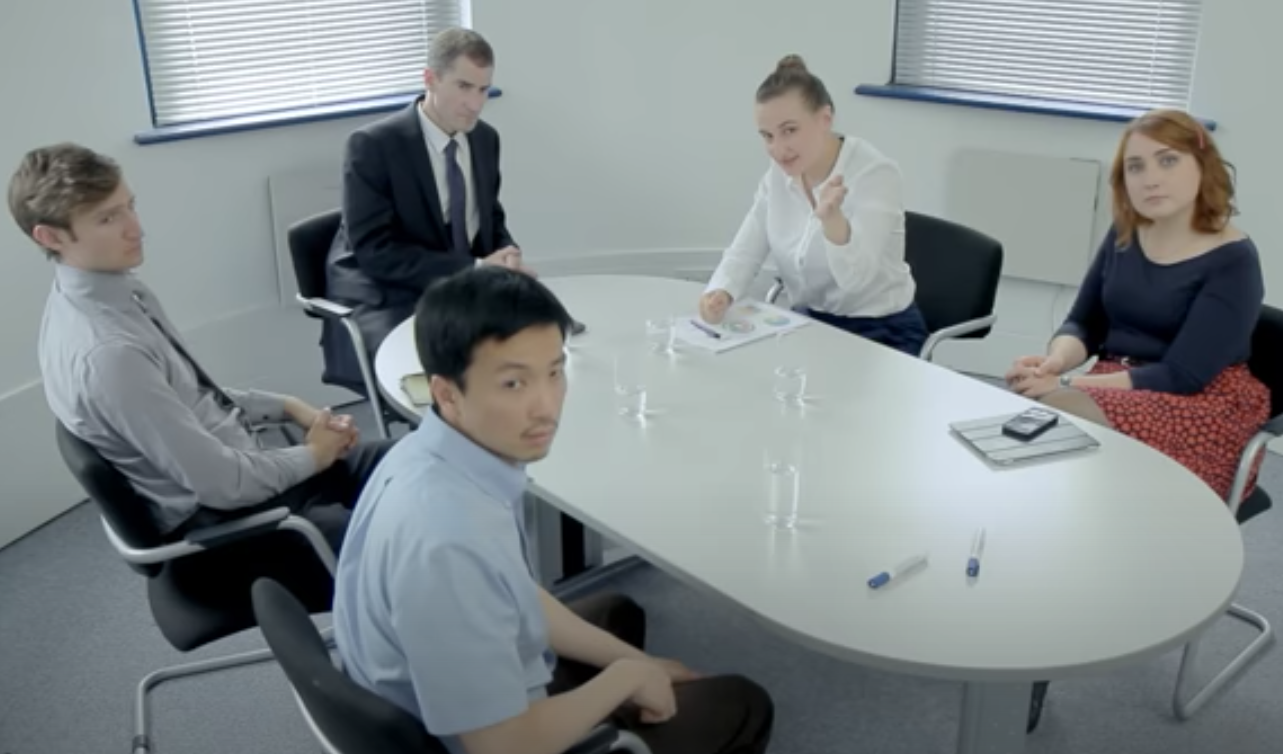
Meeting Goes Awry
Have You Had a Root Cause Analysis Review Meeting Like This?
What went wrong in the meeting above?
- They didn’t agree on definitions.
- Management didn’t understand the technical aspects of the work.
- The customer’s requirements weren’t achievable.
Have you experienced the same problem in a root cause analysis review meeting?
Definition of a Root Cause
First, does everyone agree on the definition of a “root cause” and that there can be multiple root causes for a single incident? Click on our definition of a root cause below…
What should you have learned from our definition? That you need a systematic, guided process to find root causes. That process operationally defines root causes. And that process should be the TapRooT® Root Cause Tree® Diagram.

Learn more about the guided TapRooT® RCA process HERE. And see our upcoming courses HERE.
Management Understanding of Root Cause Analysis
Let’s assume that you have been trained in advanced root cause analysis – TapRooT® RCA. But what if your management has NOT been trained in advanced root cause analysis?
Is your management convinced that you should have quick, simple answers? Maybe they watched a 5-Why video, or they are accustomed to “yes” answers from sycophant subordinates – people who tell their bosses what they want to hear. And you are looking for and finding the real root causes of incidents, and sometimes (but not always) the answer to those difficult problems are significant change.
What happens when you present a difficult improvement initiative when management wants a simple “yes?” Does it resemble the video above? (Which doesn’t seem funny when you are the expert).
What can you do? BEFORE you have a difficult incident, you need to get your senior managers trained. They need to know…
- The performance improvement vision.
- How TapRooT® RCA works and the fundamentals of RCA.
- What management needs to do to make investigations work.
- How to review and approve investigations and corrective actions.
- How to stop major accidents by analyzing precursor incidents and by proactive improvement.
- How to make conservative decisions (and have their subordinates do the same).
That’s the knowledge is that we built into the TapRooT® Executive Leadership Course.
Practical Customer Requirements
Luckily, your management is the primary customer for your root cause analysis. (Yes, regulators, your employees, and the population around your plant are customers, but let’s not discuss that here.)
If you train your management, they can have practical requirements for your root cause analysis.
GET STARTED NOW!
Yes, your investigators need to be trained in advanced guided root cause analysis (TapRooT® RCA). But advanced root cause analysis training for investigators is just a start.
You need to get training for your management to avoid the types of meetings shown above. You can sponsor that training at your site or have your management attend the course prior to the 2023 Global TapRooT® Summit. Get information about the pre-Summit course HERE.
You should also be considering general employee training. They need to know what you are doing when you perform a root cause analysis and interview them about an incident.
Now is a great time to contact your TapRooT® Implementation Advisor to discuss your training plans and get your management and general employee training scheduled before the end of the year.

Call 865-539-2139 or CLICK HERE to text us.
Thank you for being experts.