Root Cause Failure Analysis
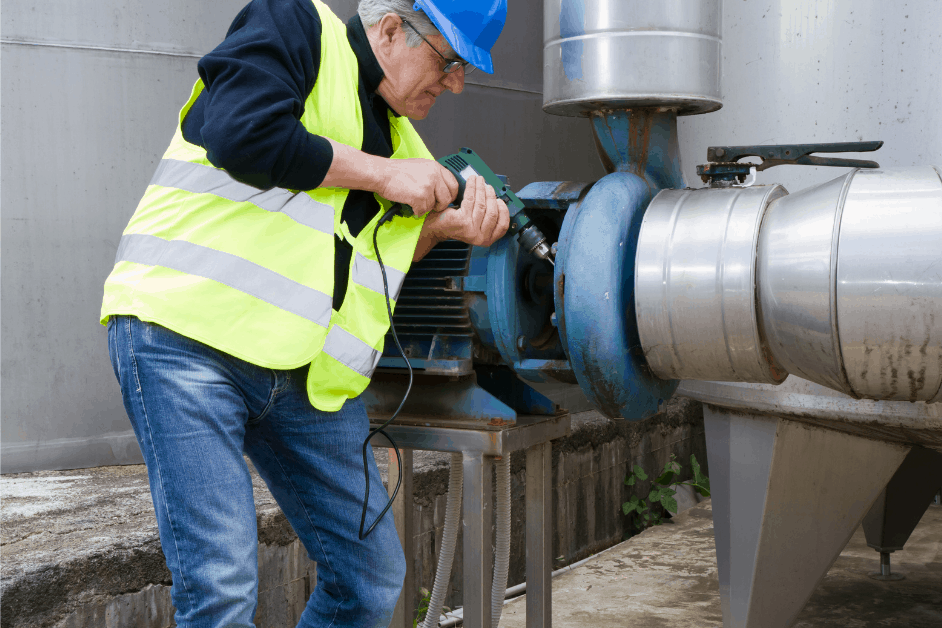
What is Root Cause Failure Analysis?
I’ve worked in the field of root cause analysis for a long time (1985). As far as I can tell, the only difference between root cause failure analysis and root cause analysis is that root cause failure analysis always involves equipment failures. Root cause analysis may or may not involve an equipment failure.
Because root cause failure analysis involves an equipment failure, before you start analyzing the root causes of the failure, you need to first do effective equipment troubleshooting to understand what caused the equipment failure.
For more about root cause analysis, read this article:
Why Do People Fail When Doing an Equipment Root Cause Failure Analysis?
Usually, they fail to do an adequate root cause failure analysis because they:
- They jump to conclusions.
- They don’t do adequate equipment troubleshooting before they start root cause analysis.
Why does starting root cause failure analysis before finishing equipment troubleshooting cause problems? For the same reason that starting to find root causes is a problem before you collect evidence about what happened.
In understanding the root causes of an equipment failure, troubleshooting the equipment failure provides the evidence you need to identify the failure’s Causal Factors and then find the Causal Factors’ root causes.
Thus, if you don’t do effective equipment troubleshooting, you are performing the root cause analysis blind.
What is Effective Troubleshooting?

Back in 1997, I started working on improving root cause failure analysis. I discovered that many people trying to find the root causes of equipment failures were not doing an adequate job of troubleshooting the equipment failure. In looking for better ways to help people do better equipment troubleshooting, I met equipment expert Heinz Bloch.
Heinz and I had some great discussions with the outcome being the Equifactor Equipment Troubleshooting System that included the Equifactor® Troubleshooting Tables and training to teach people how to perform effective troubleshooting.
By 2000, we had merged the Equifactor® Equipment Troubleshooting Techniques into the TapRooT® System to provide effective troubleshooting and root cause analysis for equipment failures.
To get more information about Equifactor®, see these links:
- Equifactor® Equipment Troubleshooting
- How Can You Use Root Cause Analysis to Improve Overall Equipment Effectiveness (OEE)
Or watch this video…
Or subscribe to our newsletter…
Equifactor® Equipment Troubleshooting and TapRooT® Root Cause Analysis Training
To learn to use the Equifactor® Troubleshooting Tables and TrapRooT® Root Cause Analysis for effective root cause failure analysis, you need to attend the 2-Day Equifactor® Equipment Troubleshooting and TapRooT® Root Cause Analysis Training.
Here is the course outline for the virtual course:
Course Outline
DAY ONE (7 HOURS)
Class Introductions and TapRooT® Introduction
SnapCharT® Basics – Understanding What Happened
Software Overview
Collecting Information
Equifactor® Basics
Customization
Begin Final Exercise – SnepCharT®
DAY TWO (7 HOURS)
Seawater Pump Example
Change Analysis
Causal Factors – Identifying the Error
Root Cause Tree® – Eliminating Blame
Root Cause Team Exercise – On your own
Continue Final Exercise – Causal Factors and Root Cause Analysis
DAY THREE(6 HOURS)
Corrective Actions – Developing Fixes
Final Exercise – Putting What You’ve Learned to Work
Final Exercise – Presentations
The course materials include the book, Using Equifactor® Troubleshooting Tools and TapRooT® Root Cause Analysis to Improve Equipment Reliability, a TapRooT® Root Cause Tree®, the Root Cause Tree® Dictionary, and the Corrective Action Helper® Guide, a $129 value. The book includes a complete set of Heinz Bloch’s troubleshooting tables.
Upon completion of the course, attendees will receive a certificate of completion and a 90-day subscription to TapRooT® VI Software, our dynamic cloud-based software that computerizes the Equifactor® and TapRooT® Techniques.
Get more course info HERE.
See the upcoming course dates and locations (including virtual courses), HERE.
