KISS and Root Cause Analysis
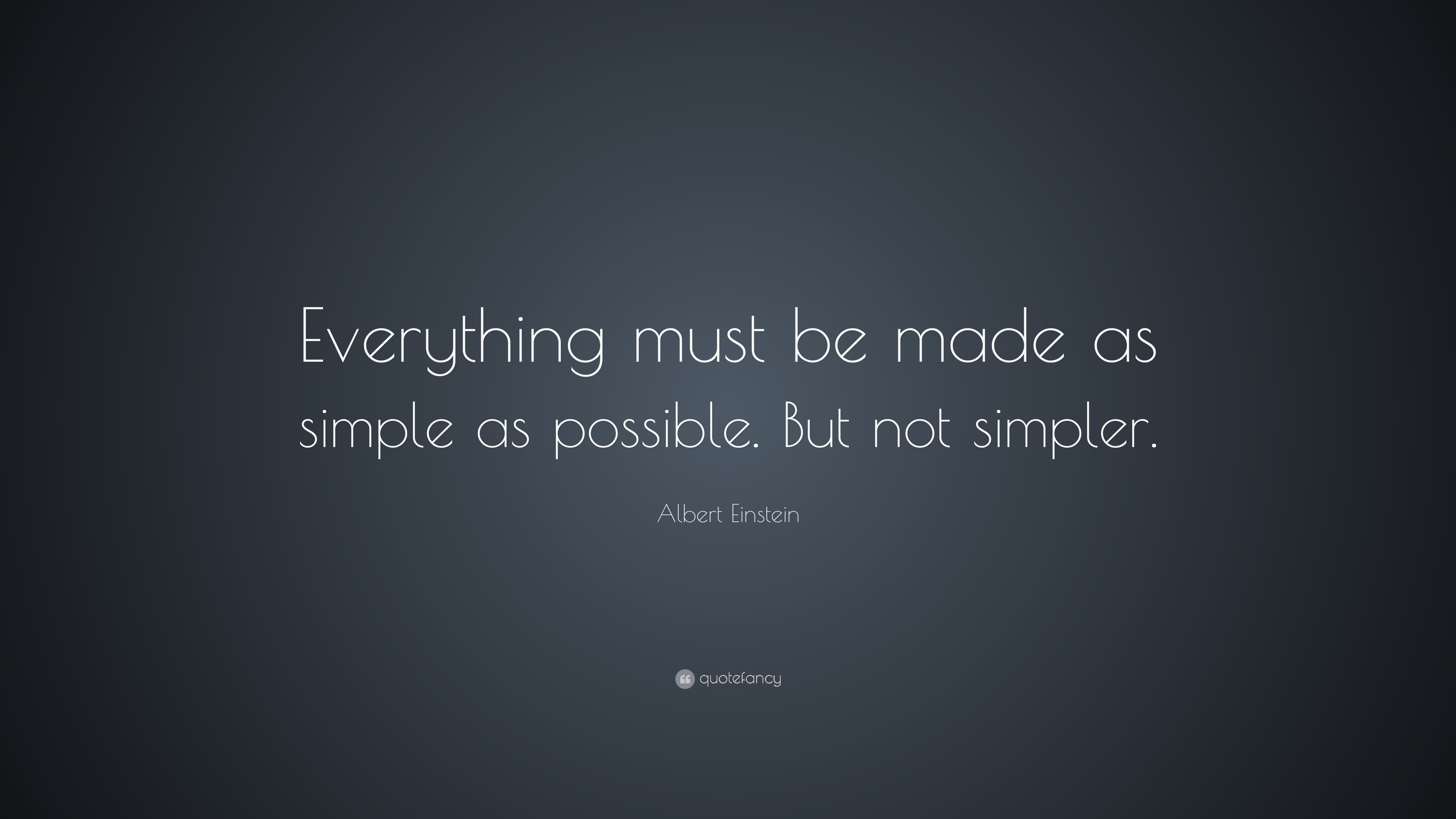
Root Cause Analysis and Keep It Simple Stupid (KISS)
I’ve heard many “experts” claim that you need to apply the KISS principle when it comes to root cause analysis. You may hear this too. You may want to keep your root cause analysis simple. I want you to understand where these experts lead many people astray.
First, what is KISS?
Keep It Simple Stupid!
The acronym implies that simple solutions are better solutions. And when simple solutions work (are effective), KISS is a dream come true. But remember Einstein’s quote:
“Everything must be made as simple as possible. But not simpler.”
Why Simple Root Cause Analysis Isn’t So Simple
So let’s start with some of the reasons that these experts say you need to use simple techniques and debunk or demystify each one. Here’s a list of common expert advice.
- It’s a waste of time to use full root cause analysis on every problem.
- People can’t understand complex root cause analysis techniques.
- Learning simple techniques will get people to start thinking deeper about problems.
- Simple is just about as good as those fancy techniques.
- Managers don’t have time to do fancy root cause analysis, and they already know what is wrong.
- You can apply those complicated techniques to just the most serious accidents.
- The data from the simple investigations will help you identify the more complex issues you need to solve.
I see these arguments all the time. They make me want to scream!
Let me debunk each one, and then you too can dismiss these “experts” the next time they try one or more of these arguments on your management team.
1. It’s a waste of time to use full root cause analysis on every problem.
I actually sort of agree with this statement. What I don’t agree with is the answer they arrive at. Their answer is that you should apply some “simple” root cause analysis technique (let’s just say 5-Whys as an example) to “solve” these problems that don’t deserve a well-thought-out answer.
First, what do I have against their ideas of simple root cause analysis? If you’ve been reading this blog for a while, you know what I’m going the explain, so just skip ahead. For those who don’t know what’s wrong with most “simple” root cause analysis techniques, I would suggest starting reading from the top of the links below until you are convinced that most expert advice about “simple” root cause analysis is root cause analysis malpractice. If you haven’t been convinced by the end of the links … perhaps you are one of the experts I’m talking about. Here’s the list of links:
What happens when root cause analysis becomes too simple? Six problems I’ve observed.
An Example of 5 Whys – Is this Root Cause Analysis? Let Me Know Your Thoughts…
What’s Wrong with 5-Whys??? – Complete Article
What’s Fundamentally Wrong with 5-Whys?
Teruyuki Minoura (Toyota Exec) Talks About Problems with 5-Whys
I believe that one of the biggest root cause analysis problems that companies face is that they are performing “root cause analysis” on problems that don’t need to be analyzed.
YES … I said it.
Not every problem deserves a root cause analysis.
What problems don’t need to be analyzed? Problems that aren’t going to teach you anything significant. I call these “paper cut problems.” You don’t need to investigate paper cuts.
But some people would say that you do need to investigate every loss time injury and medical treatment case. Maybe … maybe not.
You do need to investigate an incident if it could have caused an outcome that you are trying to prevent and there are worthy lessons learned. Some medical treatment cases fall into this category. They got a cut finger but they could have lost their whole arm.
Two similar examples are provided in the book: Using the Essential TapRooT® Techniques to Investigate Low-to-Medium Risk Incidents.
One is a sprained ankle and one is a sprained wrist. Both came from falling down. One was judged worthy of a full but simple root cause analysis using the essential features of the TapRooT® Root Cause Analysis System. One was judged not worthy of a full investigation after a simple SnapCharT® was developed. Interested in how this works? Read the book. It’s only 100 pages long and seeing how to judge if a root cause analysis is worthwhile is worth it. (And you will learn how to apply TapRooT® simply to low-to-medium risk incidents.)
The process outlined in the book is shown below…
Once you know how to do a real “simple” investigation with an effective technique, you won’t need to do a bad root cause analysis with an ineffective technique.
2. People can’t understand complex root cause analysis techniques.
I don’t know every “complex” root cause analysis technique, but I do know that this statement does NOT apply to TapRooT®. Why? Because we’ve tested it.
One “test” was at a refinery. The Operation Manager (a good guy) thought that TapRooT® was a good system but wasn’t sure his operators would understand. We decided to run a test. We decided to teach a basic class to all his union stewards. Then refinery management did a focus group with the shop stewards.
I was one of the instructors, and from the course examples they analyzed, I knew that they really enjoyed finding real root causes rather than placing blame.
They did the focus group (with us in another room). I could hear what was going on. The facilitator asked the first question: “Did you understand the TapRooT® Root Cause Analysis Technique?” One of the shop stewards said …
“If I can run a Cat Cracker, I can certainly understand this!
After all, it’s not rocket science!”
And that’s one of the great parts about TapRooT®. We’ve added expert systems for analysis of equipment and human performance problems, but we’ve kept the system understandable and made it easy to use. Making it seem like it isn’t rocket science (even though a whole bunch of science is embedded in it) is the secret sauce of TapRooT®.
3. Learning simple techniques will get people to start thinking deeper about problems.
Learning to count is required before you learn calculus BUT counting over and over again does not teach you calculus.
If you don’t understand the causes of human performance problems, you won’t find the causes of the problems by asking why. And I don’t care how many times you ask why … it still won’t work.
For years we did a basic poll at the start of our 5-Day TapRooT® Advanced Root Cause Analysis Courses. We asked:
“How many of you have had any formal training
in human factors or the causes of human error?”
Only about 2% of the attendees had ANY training on the causes of human error. But almost everybody attending our training said they had previously been assigned to find the causes of human errors. I wonder how well that went? (I can tell you from the student feedback that they said they really DID NOT address the root causes in their previous investigations.)
So, NO. Learning simple techniques DOES NOT get people to “think deeper” about problems.
4. Simple is just about as good as those fancy techniques.
NO WAY.
First, I’ve never seen a good example of 5-Whys. I’ve seen hundreds of bad examples that 5-Why experts thought were good examples. One “good example” that I remember was published in Quality Progress, the magazine of the American Society for Quality (ASQ). I couldn’t stand it. I had to write a reply. When I sent the letter to the editor, they asked me to write a whole article … so I did. To see the example and my article that was published in Quality Progress, see page 32 of the link below:
Under Scrutiny: A Critical Look at Root Cause Analysis.
Simple is not “almost as good” as real root cause analysis (TapRooT®). If you would like another example, see Chapter 3: Comparing the Results of a 5-Why Investigation to a Basic TapRooT® Investigation in the book, Using the Essential TapRooT® Techniques to Investigate Low-to-Medium Risk Incidents.
That’s it – Case Closed. Those “simple” techniques are NOT just about as good as TapRooT® Root Cause Analysis.
5. Managers don’t have time to do fancy root cause analysis, and they already know what is wrong.
Once again, I’m reminding of a saying:
Why is there never enough time to do it right,
but there is always enough time to do it over?
How many times have I seen managers misdiagnose problems because they didn’t find the root causes and then have bigger accidents because they didn’t fix the near-misses and small accidents?
The percentage of managers trained in human error causes is very similar to the statistics I previously provided (2%). This means that managers need an effective root cause analysis technique … just like investigators need an effective technique. That’s why the standard corrective actions they use don’t solve the problems and we have accidents that happen over and over again.
So if you don’t have time, don’t worry. You will make time to do it over and over again.
That reminds me of a quote from a plant manager I knew…
“If we investigated every incident,
we’d do nothing but investigate incidents!”
6. You can apply those complicated techniques to just the most serious accidents.
I’ve seen companies save their “best” root cause analysis for big accidents. Here are the two problems I see with that…
FIRST, they have big accidents BECAUSE they didn’t solve the precursor incidents. Why? Because they didn’t do good root cause analysis on the precursor incidents. Thus, applying poor root cause analysis to the lesser incidents CAUSES big accidents.
SECOND, their investigators don’t get practice using their “best” root cause analysis techniques because the “most serious” incidents are infrequent. Therefore, their investigators get rusty or they never really develop the skills they need by using the techniques on smaller incidents that could give them practice.
The key here is to learn to use TapRooT® Root Cause Analysis to investigate smaller problems. And that’s why we wrote a book about using TapRooT® for simple incidents: Using the Essential TapRooT® Techniques to Investigate Low-to-Medium Risk Incidents.
Don’t wait for big accidents to find and fix the causes of your biggest risks. Find and fix them when they give you warnings (the precursor incidents).
7. The data from the simple investigations will help you identify the more complex issues you need to solve.
Why do people think that analyzing lots of bad data will yield good results?
I think it is a misconception about mathematics. A good formula doesn’t provide knowledge from bad data.
If you don’t really know how to analyze data, you should attend our pre-Summit course:
TapRooT® Trending to manage Performance
As W. Edwards Deming said:
“Without data, you’re just another person with an opinion.”
And if you know much about Deming, you know that he was very interested in the accuracy of the data and thought that opinions should be backed by FACTS.
If you aren’t finding the real root causes, data about your BAD ANALYSIS only tells you what you were doing wrong. You now have data about what was NOT the causes of your problems. Go analyze that!
So data from BAD simple investigations DOES NOT help you solve your more complex issues. All it does is mislead your management.
Can You Have Simple AND Effective Root Cause Analysis?
THAT’S IT. All the bad advice is debunked.
Now, what do you need to do to get simple + effective root cause analysis?
1. Read the book:
TapRooT® Root Cause Analysis Leadership Lessons
You will learn the theory behind performance improvement, and you will be well on your way to understanding what management needs to do to really improve safety, quality, equipment reliability, and operational/financial performance.
2. Read the book:
TapRooT® Root Cause Analysis Implementation
You will know how to implement a real, effective root cause analysis system for low-to-medium risk incidents as well as major accidents.
3. Take the course:
If you haven’t done it already, attend one of our 5-Day TapRooT® Advanced Root Cause Analysis Courses. See the list of our upcoming public 5-Day TapRooT® Courses held around the world at this link:
http://www.taproot.com/store/5-Day-Courses/
And don’t take any more bad advice from experts who don’t know what they are talking about!
PS: If you have questions or want to discuss what you read in the books, contact us at 865-539-2139 or by e-mail by clicking HERE.