SKF Bearing Engineers Attend Equifactor® Training
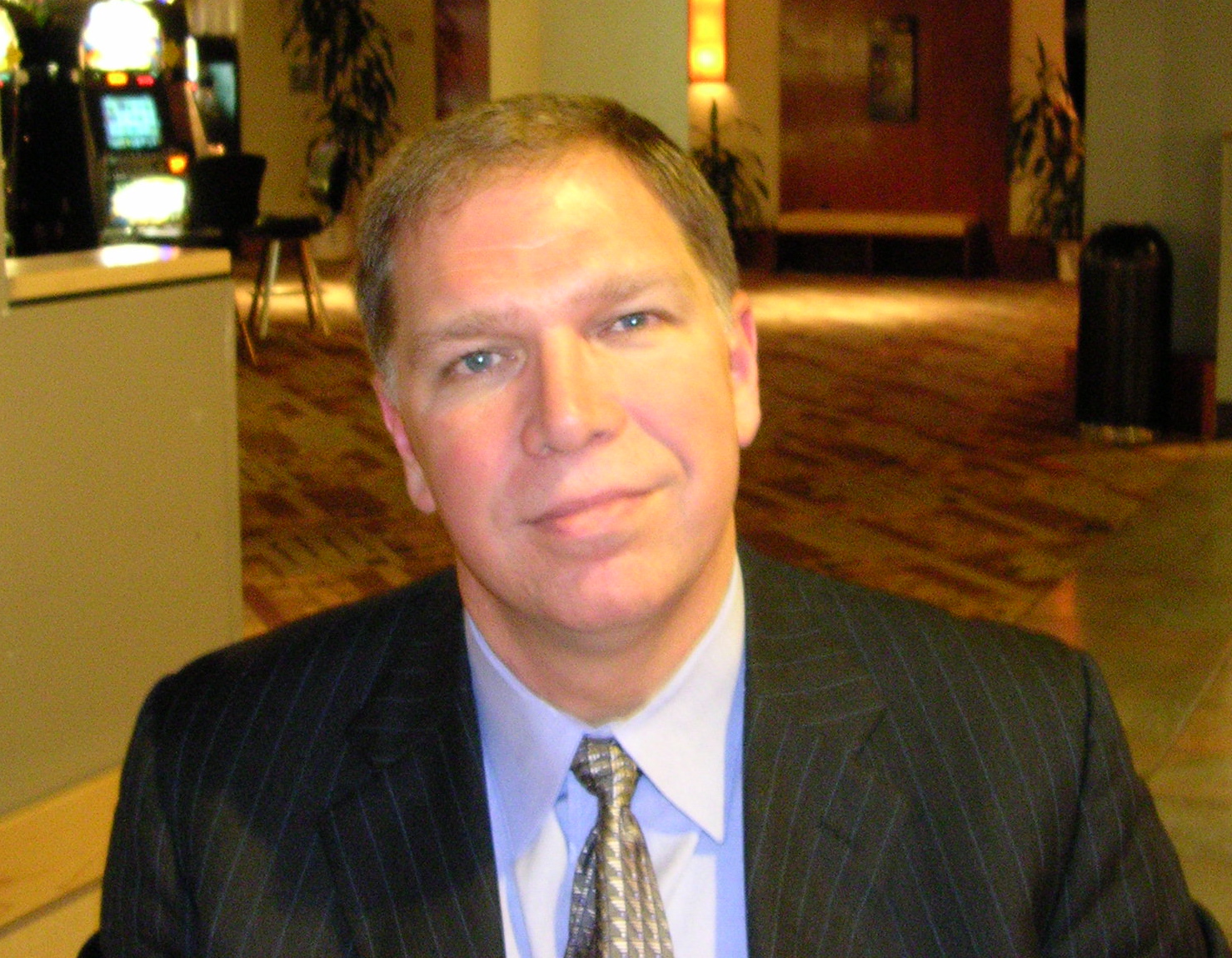
I’m in Gothenburg, Sweden, teaching an Equifactor® Equipment Troubleshooting and TapRooT® Root Cause Failure Analysis Course co-sponsored by SKF. More than half of the students in the course are SKF manufacturing, customer service, and application design engineers—a really smart bunch of people.
It is humbling to teach root cause analysis to people who know so much about bearings and equipment. But as usual, the TapRooT® System helps even experts do better root cause analysis.
The TapRooT® System “expands the universe” of potential ideas for correcting serious problems by giving experts additional ideas of possible root causes. I see this happen in all kinds of industries worldwide.
That’s why it is such a good job being a TapRooT® Instructor. Equifactor® and TapRooT® RCA come through in every case to help experienced and inexperienced investigators find root causes that they previously would have overlooked.
Another strength of the TapRooT® System that is highlighted in this course is its ability to analyze the causes of equipment problems caused by the human performance of the operators, installers, or maintainers. Machinery experts often know an amazing amount about the engineering of the machine, but they really appreciate the root cause analysis assistance they get analyzing human performance problems.
Perhaps the exercise on a pump failure was the most surprising aspect of teaching Equifactor® Troubleshooting to bearing experts.
I thought that these bearing experts might think the troubleshooting guidance provided by the Equifactor® Troubleshooting Tables might seem too simplistic to these experts. But it was gratifying to see the “lightbulbs turning on.”
After the exercise, one of the senior experts complimented me on the thoroughness of the pump and bearing troubleshooting tables. He said that, of course, he knew all the information in the tables, but he really appreciated it all in one place. The tables were an excellent way to second-check his knowledge and ensure that he didn’t leave anything out of his troubleshooting process.
This is probably the highest praise I could have asked for.
For more information about Equifactor® Troubleshooting, see THIS LINK.