Spark Observed While Removing HVAC Unit: Lockout/Tagout/Verify
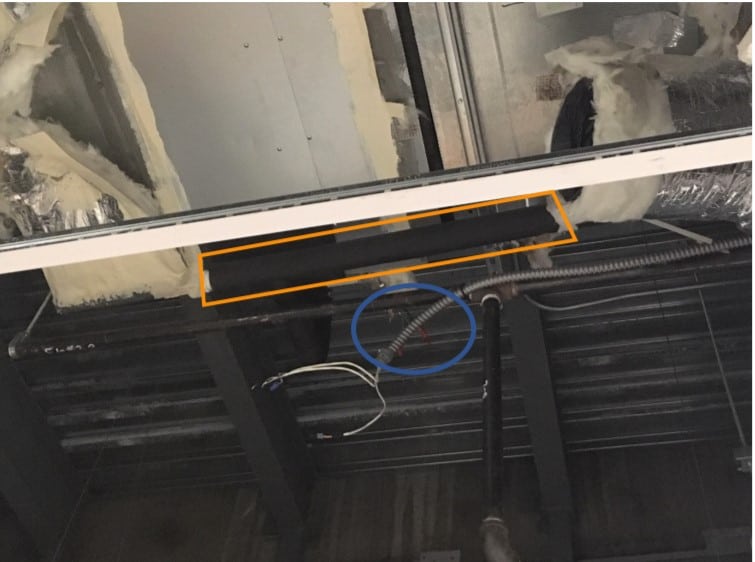
What happened to cause an electrical spark?
In October 2019, a single spark led to a concerning series of events. A University of Tennessee – Battelle, LLC (UT-B) subcontracted sheet metal worker was removing an overhead HVAC air handling unit (AHU). All electrical utilities in place to the AHUs were to be de-energized by UT-B, prior to the physical connections to each AHU being disconnected and an air gap established by subcontracted electricians.
Subcontracted sheet metal workers were to replace the old AHUs with new units
Then, the electrical connections were to be reinstalled by the subcontracted electricians. As part of the activity, a complex Lock/Tag/Verify (LTV) permit (consisting of approximately 25 locks and tags) was required and had been established by the UT-B electricians and Issuing Authority.
Since air-gapping was to be performed, the subcontractor sheet metal workers were not included in the LTV. Air-gapping of each electrical circuit was intended to eliminate the electrical hazard at each AHU and protect the sheet metal workers without the need for them to join the LTV.
The work scope also included re-energizing circuits for testing and troubleshooting. During a testing and troubleshooting activity, a sheet metal worker was verifying that the PVC condensate line beneath one of the HVAC units was disconnected as part of this authorized scope of work which was planned to be conducted with all electrical power disconnected. When the worker moved the condensate line, they observed a spark. Work was immediately stopped, and the incident was reported to UT-B management.
Incident analysis for Lesson Learned
The event occurred while performing a temporary suspension of the LTV to commission some of the new AHUs. It was determined that the system was not adequately inspected before performing the temporary suspension. The goal of this Lesson Learned is to identify the methods of placing circuits in a safe condition to allow staff, who are not Qualified Electrical Workers, to be in the immediate area.
Recommendations
NFPA 70E, Standard for Electrical Safety in the Workplace defines safe work practices for electrical construction and maintenance; the primary message of NFPA 70E is to turn off the power before working on electrical equipment. The process of turning off the power, verifying that it is off, and ensuring it stays off while work is being performed is called establishing an electrically safe work condition. Once an electrically safe condition is established, PPE is not needed and unqualified persons can perform work such as cleaning and painting on or near electrical equipment.
Acceptable methods to provide an electrically safe work condition include:
- Lockout/Tagout (LTV) methods which remove energy, verify the absence of hazardous energy, and physically control the ability to re-energize the power source
- Securing circuit parts within an enclosure requiring a tool for access
- Physically air-gapping the power to remove the energy source
At ORNL, the issuing authority is responsible for verifying the effectiveness of all energy control measures for subcontractors including LTV and air-gapping. They are also responsible for ensuring that all work is in a safe condition prior to removing energy control measures.
This Lesson Learned: “Electrical Spark Observed While Removing HVAC Unit” is shared through OPEXShare DOE Lesson from Oak Ridge National Laboratory, 2020-UTB-ORNL-0003.
Founded in 1988, the TapRooT® Root Cause Analysis System solves hurdles every investigator faces
TapRooT® Root Cause Analysis Training System takes an investigator beyond his or her knowledge to think outside the box. Backed with extensive research in human performance, incident investigation, and root cause analysis, TapRooT® is a global leader in improved investigation effectiveness and productivity, stopping finger-pointing and blame, improving equipment reliability, and fixing operating problems.
System Improvements, the creator of the TapRooT® System, has a team of investigators and instructors with years of extensive training ready to offer assistance worldwide.
TapRooT® Root Cause Analysis Training Courses are taught all over the world
If you are interested in learning how to stop repeat incidents, find a 2-Day or 5-Day course; or view the complete selection of TapRooT® courses. We are available to train you and your staff on-site at your workplace; Contact us to discuss your needs. You may also call us at 865.539.2139 to discuss any questions you may have.
Keep in Touch to Improve Your Problem-Solving Skills
We’re continually training, helping you improve your professional root cause analysis skills. Stay current with your TapRooT® Root Cause Analysis skills and training through:
- Following our blog;
- Free newsletters;
- Tuning in to TapRooT® TV Video Sessions or our podcasts;
- Connecting with us on Facebook, Twitter, Instagram, Pinterest, LinkedIn, and YouTube;
- And our annual Global TapRooT® Summit.