Troubleshoot Equipment Problems: “I wish I had this when I was in the Nuclear Navy.”
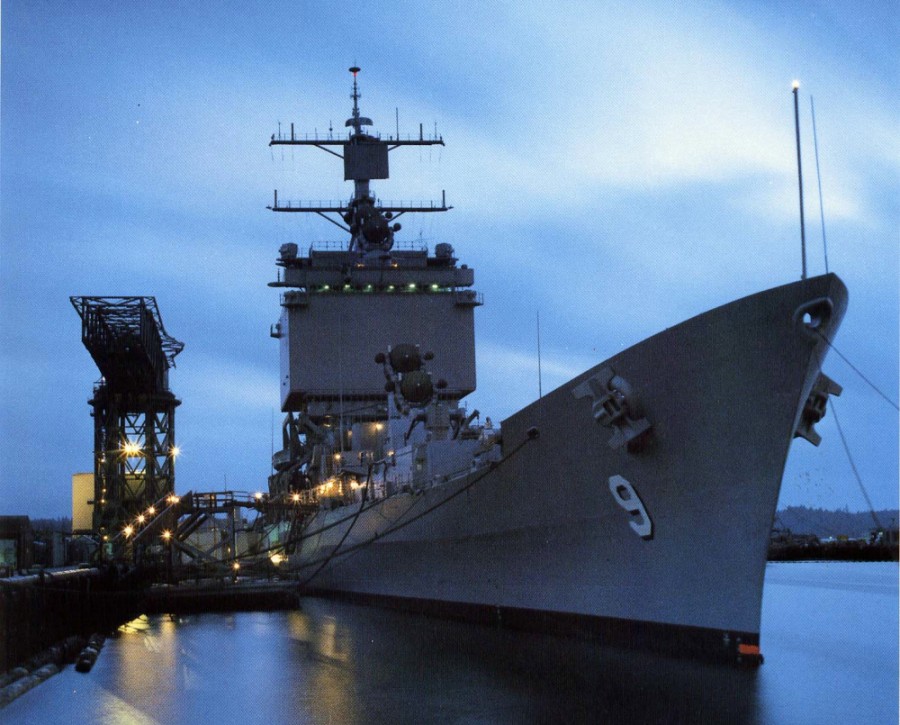
Troubleshooting Equipment Problems in the Navy
I served in the Nuclear Navy from 1978 to 1985. During that time, I was the Main Propulsion Assistant on the USS Long Beach (CGN-9), with over 100 officers, chiefs, and mechanics working for me. Troubleshooting equipment problems was an important part of their job.
Of course, we didn’t have computers, laptops, or iPads back then. Therefore, I could not have used the computerized Equifactor® Troubleshooting Tables built into the TapRooT® Software. However, even the paper-based tables in Book 5: Using Equifactor® Troubleshooting Tools and TapRooT® Root Cause Analysis to Improve Equipment Reliability would have helped.

and Corrective Action Helper® Guide
Why Would Equifactor® Troubleshooting Be So Helpful?
First, the troubleshooting tables take the knowledge of equipment expert Heinz Bloch and put it in a readily usable form. I could have used those tables (or had my guys could have used them) when troubleshooting pump, turbine, bearing, and compressor problems.
Second, Equifactor® Troubleshooting provides a systematic troubleshooting process that everyone can understand. This is a common point for discussing issues and troubleshooting plans/procedures.
Third, finding the real root causes of equipment issues using the Root Cause Tree® would have been a big step forward, especially when confronting human errors. I didn’t have any training in understanding human errors, so discipline, training, and procedures seemed like the only corrective actions for human errors.
Would You Like Advanced Troubleshooting and Root Cause Analysis?

Of course, you can order the book above to learn about Equifactor® Troubleshooting. Still, the best, fastest way to learn advanced equipment troubleshooting and root cause analysis is in the Equifactor® Equipment Troubleshooting & TapRooT® Root Cause Analysis Training.
When is the next public course? CLICK HERE to find out.
Register now to start getting a helping hand fixing equipment problems.
