Advanced Root Cause Analysis Helps Take Lost Time Rate to Zero
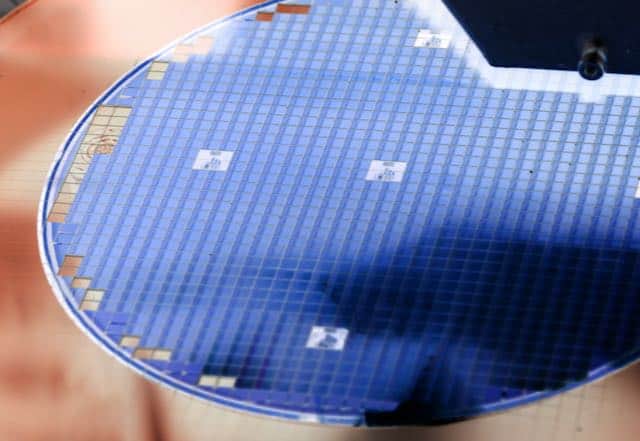
A TapRooT® User Success Story
Written By John Carpenter
Safety/ERT/Microcontamination Manager
This success story was written in the past and is being updated to our most recent blog article format and is being reposted here.
Challenge
We experienced a rather severe incident early in 1995 and recognized the need for better root cause analysis to improve our accident investigations. Our challenge was to find a better system, apply it, and thereby improve safety at our facility.
Action
We held our first on-site TapRooT® Training in mid-1995. Shortly after the training, we had an incident that allowed us to use the skills we had learned at the TapRooT® Course. It was evident to everyone participating in the investigation that the TapRooT® System was a really useful tool to help us identify the Causal Factors and ultimately the root causes and corrective actions. Our management was impressed enough with the results of the system to send two of us to a 5-Day TapRooT Advanced Root Cause Analysis Team Leader Class.
When we returned from the training, we performed several investigations using TapRooT® to help us identify fixable root causes. Our investigation work and the results we were getting came to the attention of other groups. The decision was made for our facility to obtain a TapRooT® License so that we could conduct our own on-site courses using the TapRooT® Training Material. We could then spread the techniques to a large number of employees.
Results
We held our first on-site course taught by Intel instructors in May of 1997. Within 18 months we had trained 132 employees. How did the classes go? We get frequent comments like:
“This is the best training I’ve ever had.” and
“Great class – this should have been provided years ago.”
But positive comments on course critiques are not the reason we chose to use TapRooT®. We decided to use TapRooT® to improve our root cause analysis and improve safety at our plant. And we think that the results we’ve achieved show that we made a wise decision.
First, we are frequently asked to help with investigations. The most impressive outcome is the results we’ve accomplished. When we investigate an incident using the TapRooT® System and get the corrective actions implemented, the incident does not repeat.
Second, it has become common for management to ask key TapRooT® Investigators to review other investigations (that didn’t use TapRooT®) so that they would be assured that the real root causes were identified. This is a pretty impressive indicator all by itself!
Third, TapRooT® has been so successful in helping us improve safety that we are now using it to investigate other types of incidents: yield loss, misprocessing, and audit findings.
So, how successful have we been in improving performance using TapRooT? Naturally, I can’t give TapRooT® credit for all the improvement we’ve experienced, but it is a part of some key programs that produced the following results:
Plan Safety Indicators
1995 | 1996 | 1997 | 1998 | 1999 | 2000 | 2001 | |
Lost Day Case Rate | 1.88 | 0.44 | 0.33 | 0.08 | 0 | 0.08 | 0 |
Recordable Injury Rate | 5.33 | 2.47 | 1.17 | 0.61 | 0.27 | 0.16 | 0.08 |
Safety Bulletin Incidents | 1 | 0 | 0 | 0 | 0 | 0 | 0 |
I think that these results speak for themselves.
Thanks for the great system.