Using TapRooT® to Reduce the Severity of Ergonomic Illnesses/Injuries & Cut Workers Comp Costs
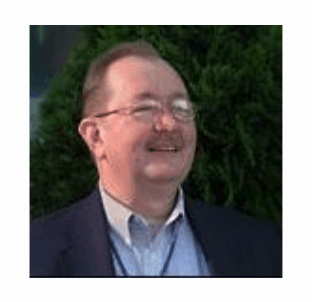
TapRooT® User Success Story
By Denis Osmer
I decided to republish some of our user success stories that needed their formats updated to our new blog style. This one is from a production, distribution, administration, and research facility. Their efforts ended up saving over $1 million per year. Read on for more information.
Challenge
I took over responsibility for HSE at a research, production, administration, and distribution facility that was having problems with ergonomic illnesses. These types of illnesses were especially troubling in our order entry and distribution areas. I had previously been trained in TapRooT® and knew how it could help people to quickly find root causes without the negative connotations usually found in investigations. Therefore, I thought that this would be an excellent candidate for a pilot program.
Action
We licensed our facility and had System Improvements personnel train a core group of 25 investigators from the various organizational units that would be investigating these and other incidents. We then performed a root cause analysis of the ergonomic incidents and implemented immediate corrective actions. One of the actions was to encourage earlier reporting of these injuries/illnesses.
Results
The reporting of ergonomic illnesses increased by up to 40% in some areas. This was even higher than expected, but the early reporting of ergonomic illnesses helped us reduce the illness’s severity. By fixing the root causes and getting early treatment, we could avoid surgery. This was a positive step for employees and our company. The severity of ergonomic incidents for the entire facility was reduced while the frequency of reporting the incidents increased. The most dramatic improvement was in the customer service department. The severity decreased from 96.4 to 0.0!
The impact of this improvement is significant. It means much less pain and suffering for our employees by fixing problems early – before significant injuries occur. Long term it also means reduced cost for ergonomic illness-related surgeries and lost time during rehabilitation. This is reflected in the cost of our self-insured worker’s compensation costs which we have saved on average over $1 million per year for the past six years.