Where Should Your Company Apply Advanced Root Cause Analysis?

How is Root Cause Analysis Used?
Root cause analysis is frequently used by safety and quality professionals to improve performance by analyzing the causes of accidents and issues and correcting their root causes (so the accidents/issues don’t happen again).
In addition, forward-thinking companies apply root cause analysis proactively to prevent safety accidents and quality issues BEFORE they happen. (CLICK HERE for more information about proactively using TapRooT® RCA.)
More Ways to Use Advanced Root Cause Analysis
But where else should advanced root cause analysis be applied? Here are five ideas…
1. Human Relations and Human Performance
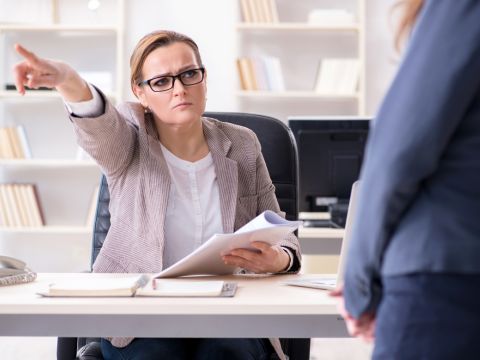
Have you ever had a union grievance because a union member was unfairly fired? Perhaps your HR department should use root cause analysis to identify the root causes of issues before deciding on disciplinary action?
We have seen many examples of problems analyzed using TapRooT® Root Cause Analysis that were thought to be someone’s “fault” but, when the root causes were discovered, were the result of system problems. Thus, advanced root cause analysis can avoid inappropriate discipline.
TapRooT® RCA includes the Root Cause Tree® Diagram, which includes an expert system to analyze human performance issues.
In addition to the expert system built into the Root Cause Tree® Diagram, we offer a special course focused on improving human performance – Stopping Human Error. See the upcoming dates and locations for upcoming public Stopping Human Error Courses HERE. Or CLICK HERE for all the other upcoming TapRooT® Courses.
2. Maintenance and Equipment Reliability
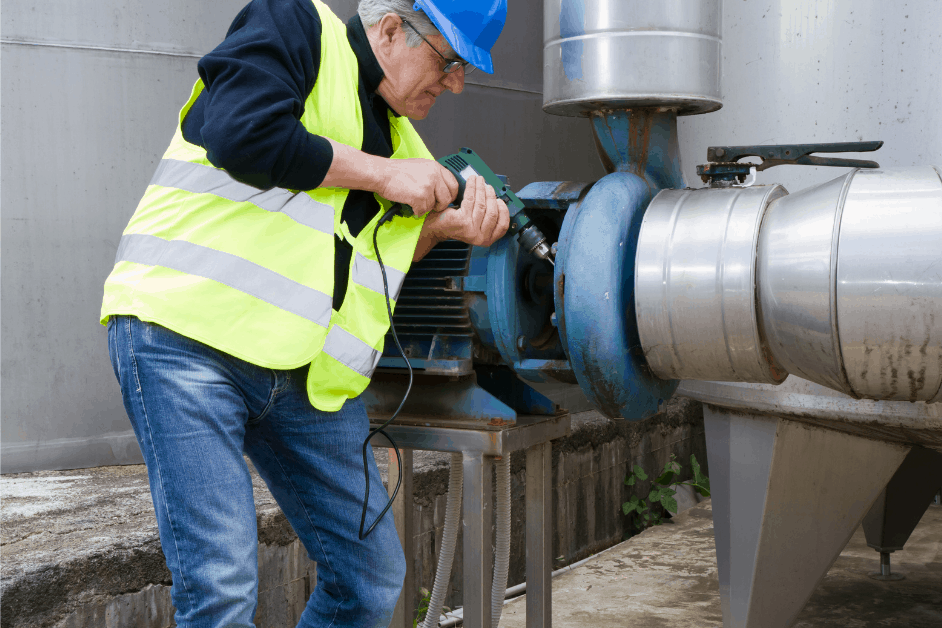
Do you wonder why you experience occasional equipment failures? Some companies have frequent repeat equipment failures because the root causes of the equipment problems are not being addressed (and, even worse, are not even being analyzed). This can be costly (expensive replacement parts and maintenance personnel time).
In addition, equipment problems left unaddressed can lead to:
- Safety incidents and accidents (when maintenance people are rushing to fix an issue that never should have happened),
- Quality issues (when equipment failures cause quality problems), or
- Cost overruns or missed schedules (because vital equipment failed, causing excessive downtime).
Isn’t it time your maintenance folks and equipment reliability professionals had a systematic troubleshooting/root cause analysis method? They should apply Equifactor Equipment Troubleshooting and TapRooT® Root Cause Analysis Techniques to stop needless equipment failures by improving equipment reliability with effective corrective actions.
Plus, systematic equipment troubleshooting can save your maintenance folks time when analyzing equipment failures and get equipment back up and running in record time.
What if one of the standard equipment troubleshooting tables doesn’t cover your equipment? You can develop a custom troubleshooting table and add it to those already in the TapRooT® Software.
CLICK HERE to see the upcoming public Equifactor® Course dates and locations.
3. IT/Cyber Security
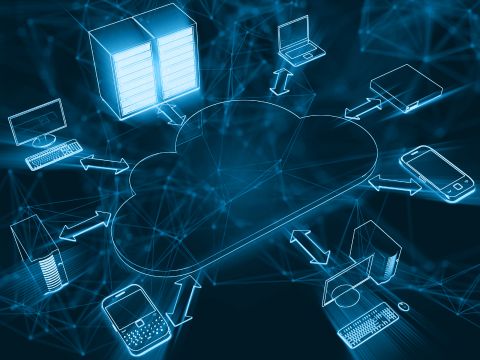
Does your company have network issues, computer security problems, or other tech issues? These problems are often caused by human performance issues (human errors). These are excellent targets for a solution using TapRooT® Root Cause Analysis. People have sent their IT folks to our public TapRooT® Courses or trained their whole department in onsite TapRooT® Courses to have better root cause analysis of IT issues. To schedule a course at your site, CLICK HERE. Or CLICK HERE to see all the upcoming public course dates and locations.
4. Operations/Facility Management
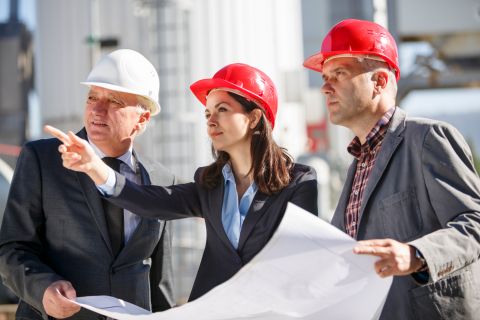
Safety and quality issues aren’t the only problems that operations and facility managers face. Process downtime, upsets, schedule slippage, and facility issues need advanced root cause analysis to ensure effective, practical corrective actions.
5. Engineering
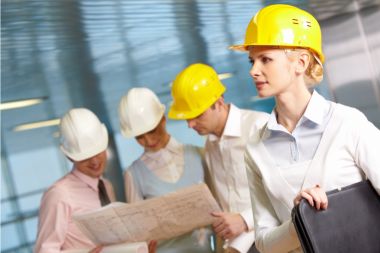
Engineers often investigate problems. They need systematic root cause analysis (TapRooT® RCA).
One engineer taking our 5-Day TapRooT® Advanced Root Cause Analysis Team Leader Training told me that by the third day of the course, he had an idea based on the course material that would save his company over $1 million. He said the course had paid for itself many times over and should be a standard part of any engineer’s career development.
Do you need to set up on-site training for your engineers? Contact us by CLICKING HERE. Or send your engineers to one of our public 5-Day Courses. See the dates and locations of upcoming 5-Day Courses by CLICKING HERE.
That’s Just a Start
Those are a few ideas to get you started. When systematically applied to problems, you will be amazed at how much TapRooT® Root Cause Analysis can help your company:
- Save money,
- Solve tech issues,
- Stop quality issues,
- Improve operations,
- Improve equipment reliability,
- Avoid unnecessary discipline,
- Save lives and stop injuries.
Call us at 865-539-2139 to discuss how advanced root cause analysis can benefit your company the most. Our implementation experts will happily schedule an executive briefing to explain how TapRooT® Root Cause Analysis can be applied across your company.
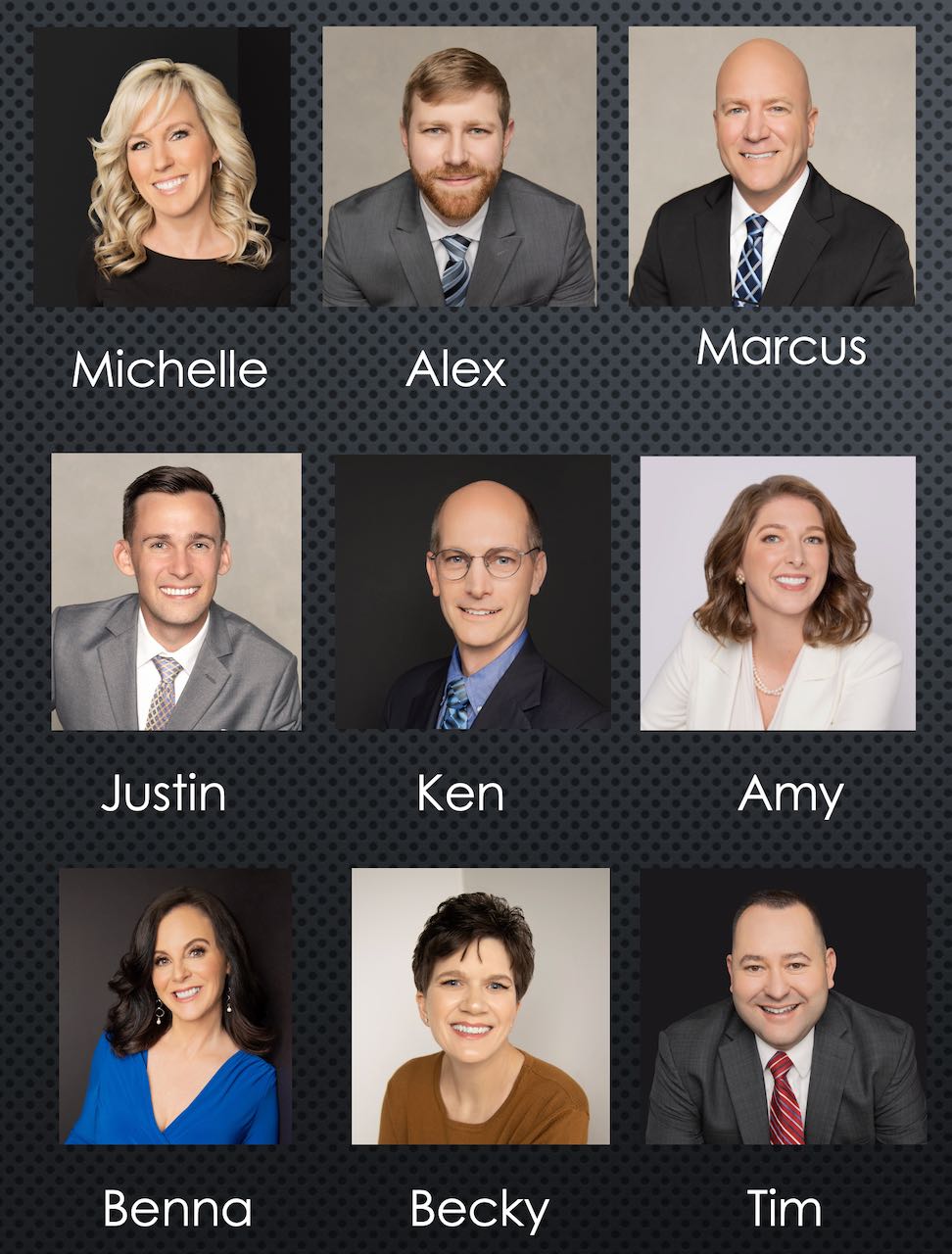