3 Reasons People Avoid Root Cause Training
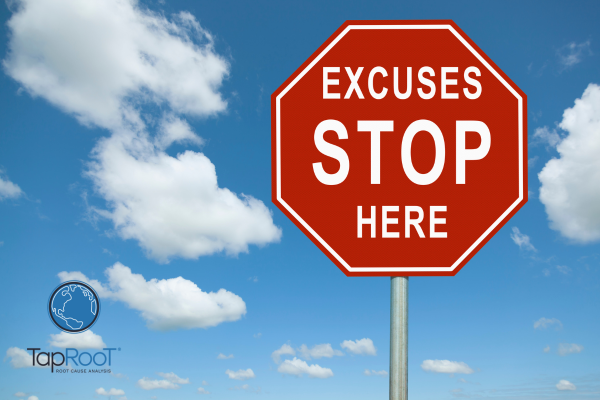
People are often surprised when they learn the reasons they avoid root cause analysis training are invalid. Here are the top three excuses people give for not pursuing training:
1. Most employers aren’t seeking that skill when hiring.
Root cause analysis is a top skill valued by employers because mistakes don’t “just happen” but can be traced to well-defined root causes that can be corrected. A bonus to root cause analysis training is that root causes identified over time across multiple occurrences can be used for proactive improvement. For example, if a significant number of investigations point to confusing or incomplete SPAC (Standards, Policies, or Admin Controls), improvement can begin. Trending of root causes allows the development of systematic improvements as well as evaluation of the impact of corrective actions. What boss doesn’t appreciate an employee who can prevent HUGE problems and losses from occurring? Promoting your root cause analysis skills is an impressive topic of conversation in any job interview.
2. It takes too long to learn it.
In just 2 days you can learn all of the essentials to conduct a root cause analysis and add this impressive skill to your resume. You will be equipped to find and fix the root causes of incidents, accidents, quality problems, near-misses, operational errors, hospital sentinel events, and other types of problems. The essential TapRooT® Techniques include:
- SnapCharT® Diagram – a simple, visual technique for collecting and organizing information to understand what happened.
- Root Cause Tree® Diagram – a systematic, repeatable way to find the root causes of human performance and equipment problems — the Root Cause Tree® Diagram helps investigators see beyond their current knowledge.
- Corrective Action Helper® Helps investigators think “outside the box” to develop effective corrective actions.
There are all kinds of training programs you can enroll in for your career development that take months, even years, to complete. A 2-day investment in this valuable training program will equip you with a powerful skill that will set you apart from the rest.
3. I don’t have enough technical knowledge to take training like that.
It doesn’t matter if you have a high school diploma or an MBA. It doesn’t matter if you do not know much about root cause analysis beyond the description provided below. Our attendees, at every level of education and technical skill, find that they can engage in the training and take away root cause analysis skills to implement immediately. It is not a “sit and listen” training – attendees do hands-on exercises to develop their new knowledge in the course.
Root cause analysis is a systematic process used in investigating and fixing the causes of major accidents, everyday incidents, minor near-misses, quality issues, human errors, maintenance problems, medical mistakes, productivity issues, manufacturing mistakes, and environmental releases.
Root cause analysis training provides:
- The knowledge to identify what, how, and why something happened, and this knowledge is vital to preventing it from happening again.
- The understanding that root causes are identifiable and can be managed with corrective actions.
- Ease of data collection, root cause identification, and corrective action recommendations and implementation.
Still not convinced root cause analysis training is for you?
GUARANTEE for the 2-Day TapRooT® Incident Investigation and Root Cause Analysis Course: Attend this course, go back to work, and use what you have learned to analyze accidents, incidents, near-misses, equipment failures, operating issues, or quality problems. If you don’t find root causes that you previously would have overlooked and if you and your management don’t agree that the corrective actions that you recommend are much more effective, just return your course materials/software and we will refund the entire course fee.
CLICK HERE to register for the 2-Day TapRooT® Root Cause Analysis Course.